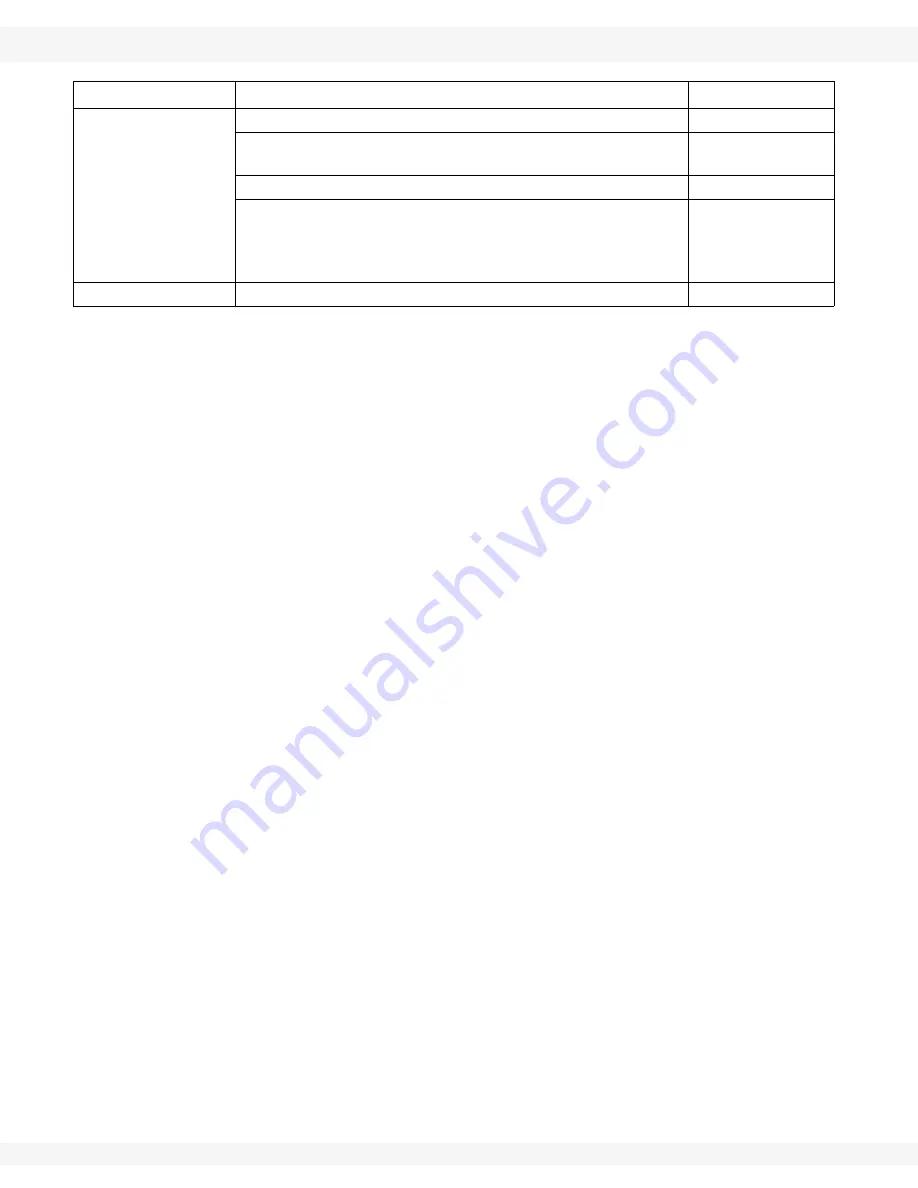
6. M
AINTENANCE
& S
TORAGE
W
ESTFIELD
- G
RAIN
A
UGERS
W130 - 31’ & 36’ PTO-SD & EMD
42
30749 R0
Winch
Note: Service
winch with auger in
fully lowered posi-
tion and cable
slack.
Keep a film of grease on gears.
Regularly
Oil the ratchet pawl pivot, bushings, and pinion threads.
Do not get oil or grease on brake discs.
Occasionally
Replace brake discs if less than 1/16” thick.
As required
Check for proper ratchet pawl operation.
When cranking in (clockwise) = loud clicking
When cranking out (counterclockwise) = no clicking and
ratchet pawl fully engaged into gear teeth
Regularly
Truss Cables
Adjust to keep auger tube reasonably straight.
As necessary
Area
Maintenance
Frequency
Summary of Contents for W130-31
Page 6: ...1 INTRODUCTION WESTFIELD GRAIN AUGERS W130 31 36 PTO SD EMD 6 30749 R0 ...
Page 14: ...2 SAFETY WESTFIELD GRAIN AUGERS W130 31 36 PTO SD EMD 14 30749 R0 ...
Page 30: ...3 ASSEMBLY WESTFIELD GRAIN AUGERS W130 31 36 PTO SD EMD 30 30749 R0 ...
Page 34: ...4 TRANSPORT PLACEMENT WESTFIELD GRAIN AUGERS W130 31 36 PTO SD EMD 34 30749 R0 ...
Page 40: ...5 OPERATION WESTFIELD GRAIN AUGERS W130 31 36 PTO SD EMD 40 30749 R0 ...
Page 44: ...6 MAINTENANCE STORAGE WESTFIELD GRAIN AUGERS W130 31 36 PTO SD EMD 44 30749 R0 ...