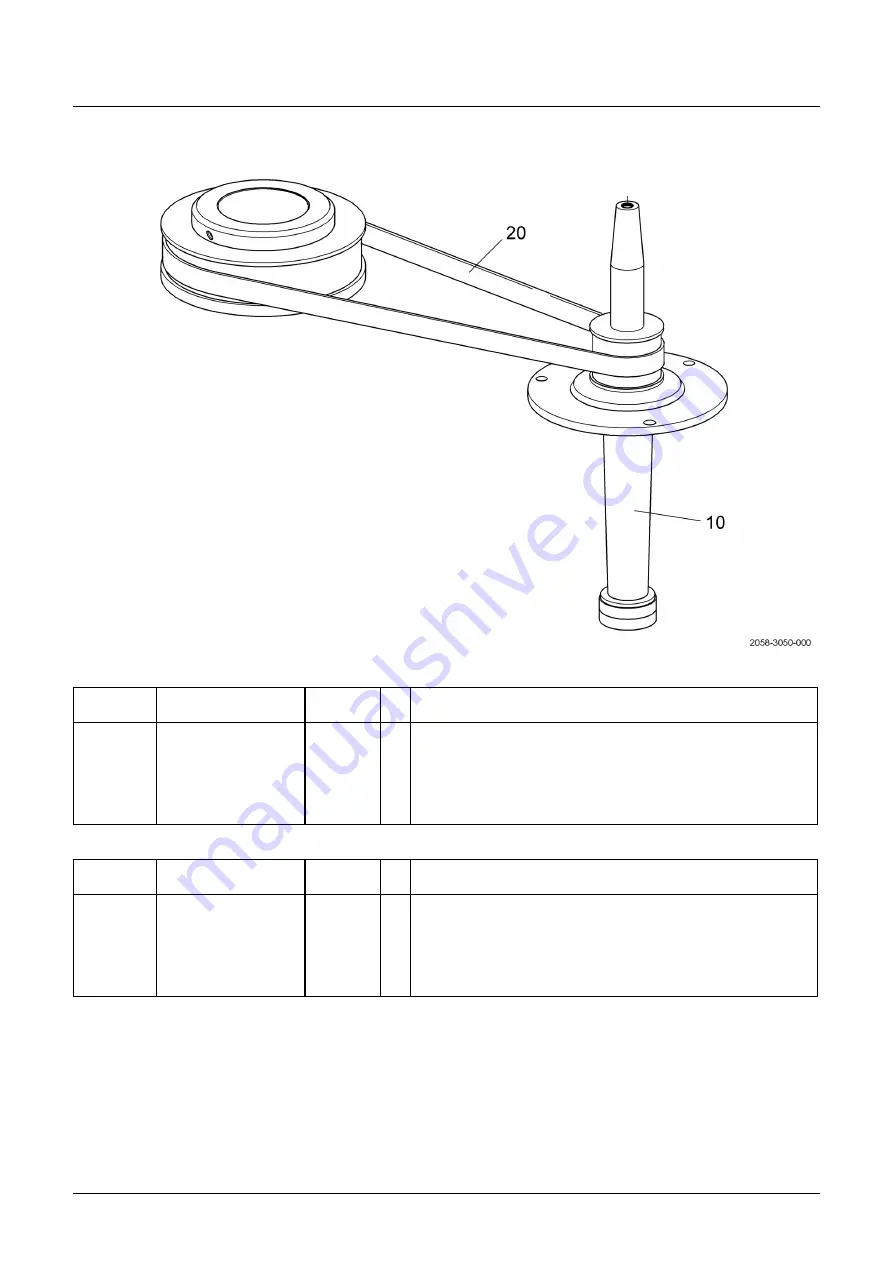
Westfalia Separator
180
Mineraloil Systems GmbH
2058-9001-101
/
0506
Fig. 279
Pos. Part
Number
Qty.
Designation
- 2058-3050-000
1
Set of drive parts – 50 Hz
10 See
1
Spindle assembly
20 0021-3345-900
1
Drive belt
Pos. Part
Number
Qty.
Designation
- 2058-3060-000
1
Set of drive parts – 60 Hz
10 See
1
Spindle assembly
20 0021-3344-900
1
Drive belt
Summary of Contents for OSD 6-91-067
Page 8: ...Westfalia Separator 8 Mineraloil Systems GmbH 2058 9001 101 0506 ...
Page 70: ...Westfalia Separator 70 Mineraloil Systems GmbH 2058 9001 101 0506 ...
Page 79: ...Westfalia Separator Mineraloil Systems GmbH 79 2058 9001 101 0506 ...
Page 157: ...Westfalia Separator Mineraloil Systems GmbH 157 2058 9001 101 0506 ...
Page 160: ...Westfalia Separator 160 Mineraloil Systems GmbH 2058 9001 101 0506 ...
Page 168: ...Westfalia Separator 168 Mineraloil Systems GmbH 2058 9001 101 0506 ...
Page 170: ...Westfalia Separator 170 Mineraloil Systems GmbH 2058 9001 101 0506 Fig 273 ...
Page 172: ...Westfalia Separator 172 Mineraloil Systems GmbH 2058 9001 101 0506 Fig 274 ...
Page 177: ...Westfalia Separator Mineraloil Systems GmbH 177 2058 9001 101 0506 ...
Page 178: ...Westfalia Separator 178 Mineraloil Systems GmbH 2058 9001 101 0506 Fig 278 ...
Page 181: ...Westfalia Separator Mineraloil Systems GmbH 181 2058 9001 101 0506 ...
Page 182: ...Westfalia Separator 182 Mineraloil Systems GmbH 2058 9001 101 0506 Fig 280 ...
Page 184: ...Westfalia Separator 184 Mineraloil Systems GmbH 2058 9001 101 0506 Fig 281 ...
Page 186: ...Westfalia Separator 186 Mineraloil Systems GmbH 2058 9001 101 0506 Fig 282 ...
Page 190: ...Westfalia Separator 190 Mineraloil Systems GmbH 2058 9001 101 0506 Fig 285 ...
Page 196: ...Westfalia Separator 196 Mineraloil Systems GmbH 2058 9001 101 0506 Fig 290 ...
Page 198: ...Westfalia Separator 198 Mineraloil Systems GmbH 2058 9001 101 0506 Fig 291 ...
Page 200: ...Westfalia Separator 200 Mineraloil Systems GmbH 2058 9001 101 0506 Fig 292 ...
Page 202: ...Westfalia Separator 202 Mineraloil Systems GmbH 2058 9001 101 0506 Fig 293 ...
Page 204: ...Westfalia Separator 204 Mineraloil Systems GmbH 2058 9001 101 0506 ...
Page 205: ...Westfalia Separator Mineraloil Systems GmbH 205 2058 9001 101 0506 ...