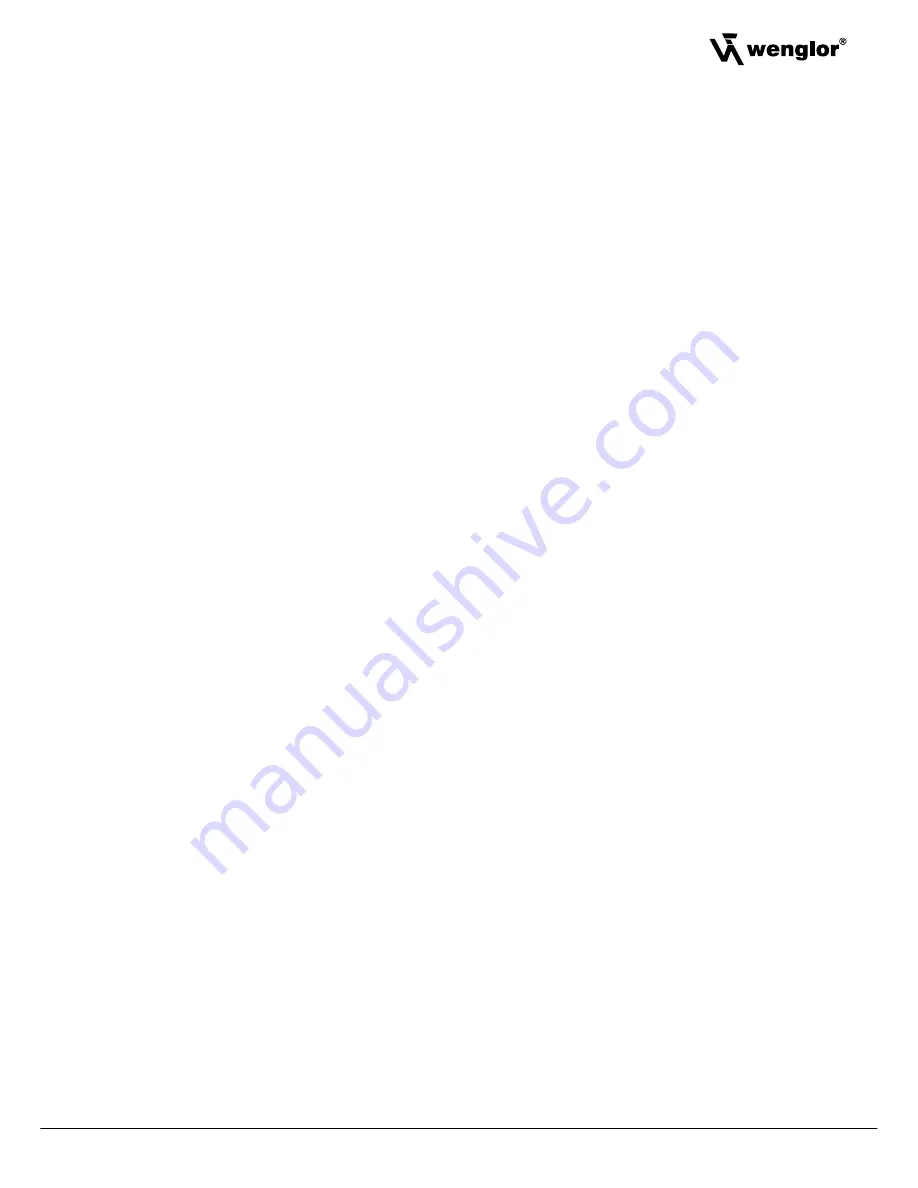
10
Sensors for your success
www.wenglor.com
Sensors for your success
www.wenglor.com
EN
External Teach-In
If the control panel is inaccessible, the Sensor can be configured via the external Teach-In input (pin 1).
The last Teach-In mode selected at the control panel is always active (i.e. Two-Point or dynamic Teach-In).
External Two-Point Teach-In
Teach in the first intensity value:
Teach in the second intensity value:
• Set the rotary selector switch
Ý
to
RUN
• Align the Sensor spot to the background
• Apply a voltage of 10 to 30 V to external
• Apply a voltage of 10 to 30 V to external
Teach-In input T (pin 1) for at least 0.3 s
Teach-In input T (pin 1) for at least 0.3 s
• Disconnect voltage from Teach-In input T (pin 1)
• Disconnect voltage from Teach-In input T (pin 1)
è
The LED at the minus key blinks
è
The switching threshold is calculated
è
The intensity value of the marking is
and saved to memory
saved to buffer memory
è
The LED at the minus key stops blinking
•
• Check for correct function
If the difference between the two acquired intensity values is too small, the output switching status indicator
A
blinks rapidly for approximately 3 seconds, and switching thresholds are not updated.
External Dynamic Teach-In
Objects to be scanned move at a constant speed.
If no continuous alternating back and forth between the marking and the background occurs during recording,
the spot must be aligned to the background when the Teach-In mode is first initialised.
Initialise recording mode operation:
• Set the rotary selector switch
Ý
to
RUN
• Apply a voltage of 10 to 30 V to external Teach-In input T (pin 1) for at least 0.3 s
• Disconnect voltage from Teach-In input T (pin 1)
è
The LED at the minus key blinks: recording mode operation is active
è
Intensity values are continuously recorded
Exit recording mode operation:
• Apply a voltage of 10 to 30 V to external Teach-In input T (pin 1) for at least 0.3 s
• Disconnect voltage from Teach-In input T (pin 1)
è
Recording is stopped
è
The switching threshold is calculated and saved to memory
• Check for correct function
If the difference between the two acquired intensity values is too small, the output switching status indicator
A
blinks rapidly for approximately 3 seconds, and switching thresholds are not updated.