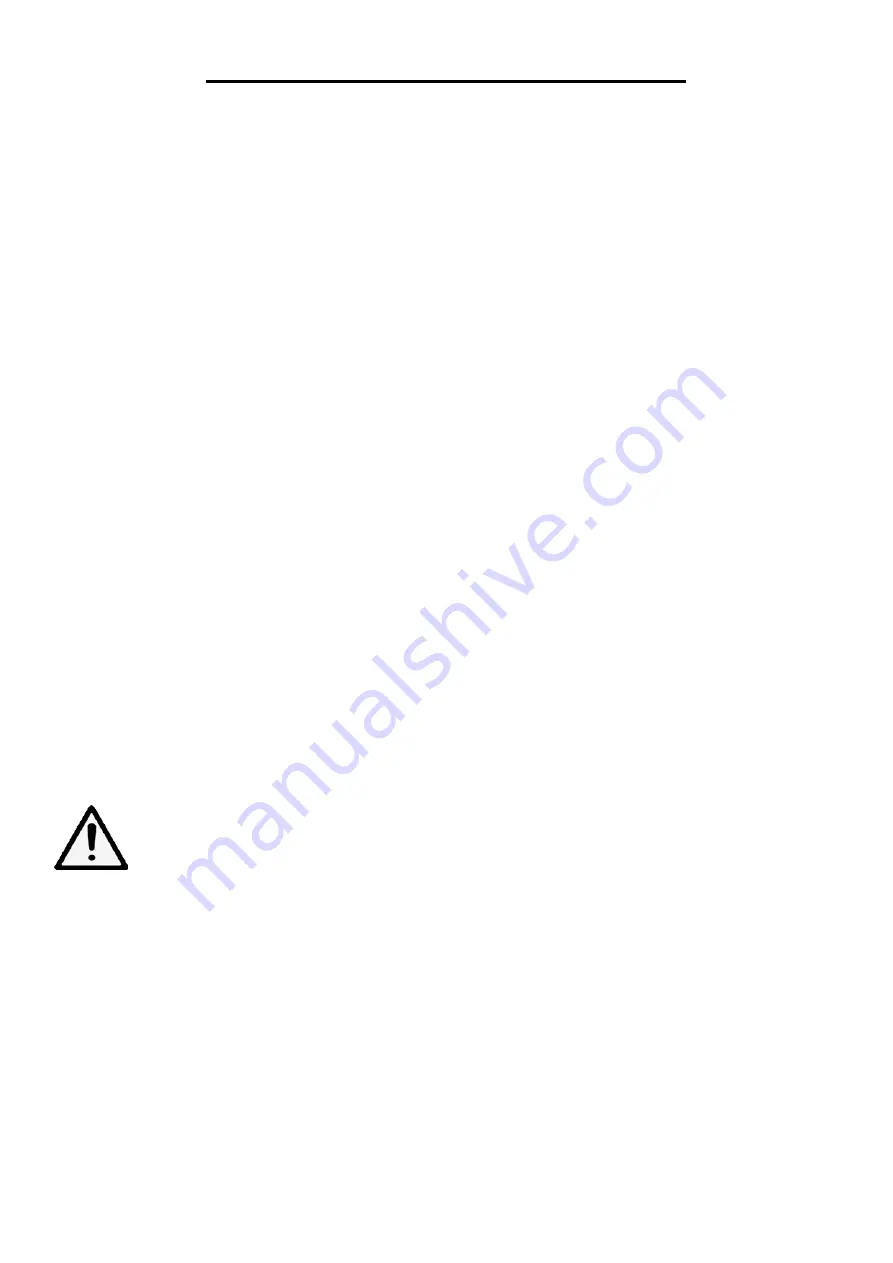
SAFETY RULES
Safety is a combination of common sense, staying alert and knowing how your item works.
SAVE THESE
SAFETY INSTRUCTIONS.
WARNING:
To avoid mistakes and serious injury, do not use your tool until the following steps have been
read and understood
1. READ and become familiar with this entire instruction manual, no matter how boring it may be. LEARN
the tool’s applications, limitations, and possible hazards.
2. REGULATE AIR PRESSURE. Use air pressure that is compatible with the ratings on the nameplate of the
tool. Do not connect the tool to a compressor rated at over 175 psi even in the event of a regulator failure.
3. USE ONLY clean, dry and regulated air. Condensation from an air compressor can rust and damage the
internal workings of the tool.
4. ALWAYS keep your work area clean, uncluttered, and well lit. DO NOT work on floor surfaces that are
slippery with sawdust or wax.
5. KEEP BYSTANDERS AT A SAFE DISTANCE from the work area, especially when the tool is operating.
NEVER allow children or pets near the tool.
6. DO NOT FORCE THE TOOL to do a job for which it was not designed.
7. DRESS FOR SAFETY. Do not wear loose clothing, gloves, neckties, or jewelry (rings, watches, etc.)
when operating the tool. Inappropriate clothing and items can get caught in moving parts and draw you in.
ALWAYS wear non-slip footwear and tie back long hair.
8. WEAR A FACE MASK OR DUST MASK to fight the debris produced by operation and ear protection to
fight hearing loss. Everyone in the work area MUST wear safety glasses with side shields. These safety glasses
must conform to ANSI Z87.1 requirements (approved glasses have “Z87” printed or stamped on them). It is
the employer’s responsibility to enforce the use of eye protection equipment by both the tool operator and
others in the work area.
WARNING:
Dust generated from certain materials can be hazardous to your health. Always
operate the tool in a well-ventilated area and provide for proper dust removal. Use dust collection
systems whenever possible.
9. ALWAYS USE an air hose that is rated at a maximum working pressure of at least 150 psi (10.3 bar) or
150% of the maximum system pressure.
10. DO NOT USE BOTTLED GASES to power this tool. Bottled compressed gases such as oxygen,
carbon dioxide, nitrogen, hydrogen, propane, acetylene or air are not for use with pneumatic tools. Never use
combustible gases or any other reactive gas as a power source for this tool. Danger of explosion and/or serious
personal injury may result.
11. USE COUPLINGS that relieve all pressure from the tool when it is disconnected from the power supply.
Use hose connectors that shut off the air supply from the compressor when the tool is disconnected.
12. DISCONNECT tool from air supply when not in use. Remove fasteners from magazine before leaving
the area or passing the tool to another operator. Do not climb ladders, stairs, scaffoldings, etc. without
disconnecting the tool. Do not carry a connected tool to another work area. Do not make adjustments, remove
4
Summary of Contents for 61741
Page 12: ...EXPLODED VIEW AND PARTS LIST 12 ...
Page 16: ...THANKS FOR REMEMBERING ...