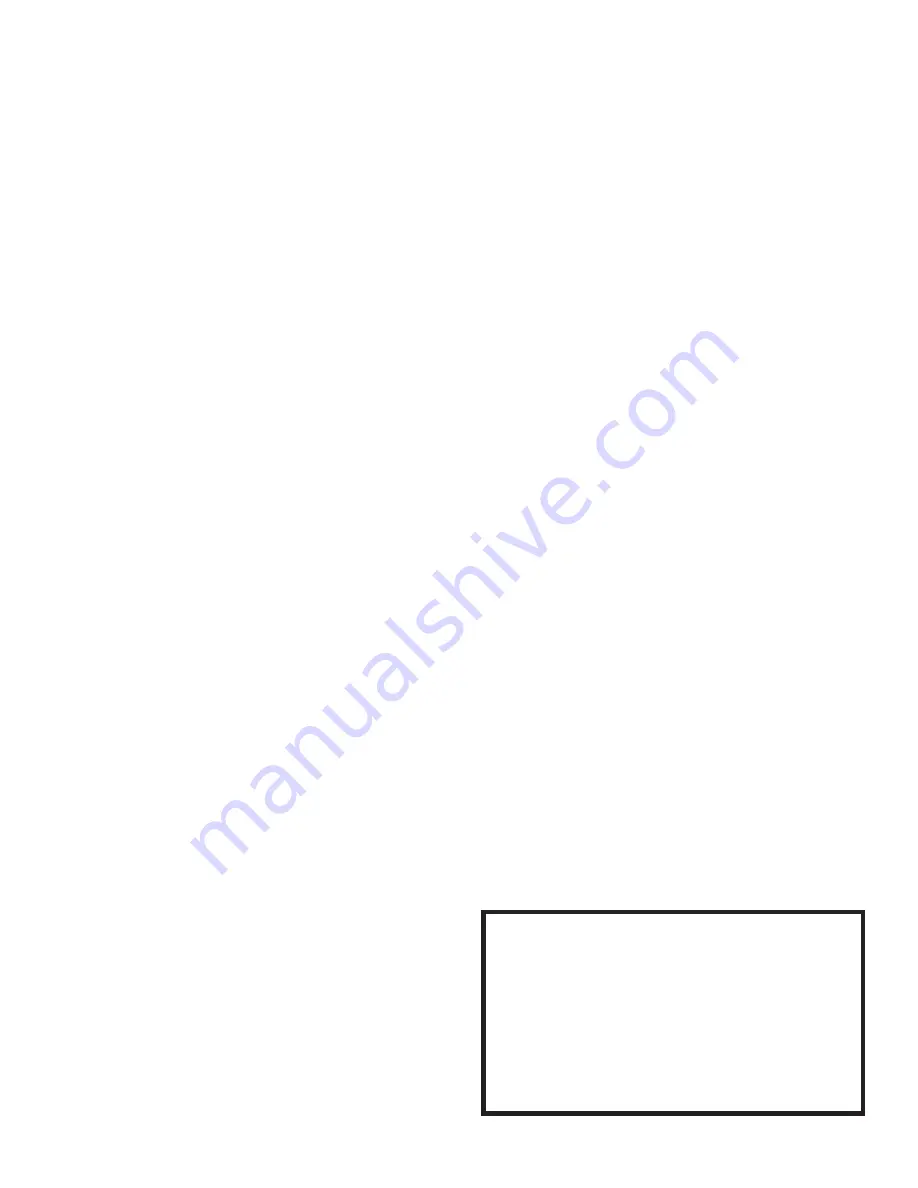
7
BLADE BRUSHES
Blade brushes should be cleaned frequently with
kerosene or a good solvent. To take advantage of both
rows of bristles, invert blade brushes and install them
on the opposite side of the blade.
For best results, replace worn, fi lled or sticky brush-
es. When bolting brushes to the mounting angles, be
sure wire bristles are turned in the same direction that
the blade travels.
BLADE GUIDE ADJUSTMENT
1. Check the blade fi t between guide bearings by
grasping the blade between the guide and the band
wheel.
2. Twist blade back and forth.
3. If too much clearance is found, rotate the eccentric
axle (34), page 12, until the bearing (32) is snug
against blade and all clearance has been removed.
4. Check guide bearing (32) with thumb by applying
force against bearing. It should be possible to rotate
the bearing while it is snug against the blade and all
clearance has been removed.
5. When looseness has been corrected, make another
cut. If the cut is not straight, further adjustment must
be made.
6. Place a square on the cut. Determine if the blade is
cutting toward or away from the bed or if it is out of
square with the vise.
7. If the vise is out of square, correct this by squaring
the vise with the slot in the saw bed.
8 If the cut is out of square on the vertical dimension,
correct this by moving the guides either away from
or towards the saw bed. This is accomplished as
follows:
a. Loosen the 2 cap screws (31), which hold the
guide (28) to the guide brackets (23 & 37). Hold
the guide from twisting and tap it in the desired
direction until the blade is square with the saw
bed. To do this:
1. Place a spacer between the frame wheel
guard and the switch box raising the blade
teeth just over the saw bed.
2. Place a machinist’s square on the saw bed
and move it to touch the body of the saw
blade - making sure it does not touch the
blade
teeth.
3. Use a feeler gauge, .002” or less, to see that
the lade is square from top to bottom. If
further adjustment is needed, loosen cap
screws on one blade guide and rotate guide
so the feeler gauge will not enter at top or
bottom. Do not move guide sideways. This
may move the blade out of square with the
vise. Tighten cap screws.
LUBRICATION
Correct and adequate lubrication is very important
to achieve maximum service. It is imperative that all
dust and dirt be removed before lubricating.
Marfak Grade “O” Grease, or equivalent, is used
in the gear case. Other parts of the saw may be lubri-
cated as follows:
1. Vise adjusting screw. Use a heavy oil or light
grease.
2. Keep internal ring gear and pinion well lubricated
with a good quality, medium grade, fi brous grease.
3. Wheel ball bearings are sealed and permanently
lubricated.
4. For proper motor lubrication, follow the motor man-
ufacturer’s instructions.
LUBRICATION SUMMARY
GEAR CASE:
Service interval; inspect after 3 years and
annually
thereafter.
Lubricant: Mobilgrease XHP220 or
equivalent.
VISE SCREW, RING GEAR, PINION:
Inspect monthly
Lubricant: Use Anti-seize on vise screw
Use Extreme Pressure Open Gear Lube on ring
and pinion gears sparingly.
HELPFUL SUGGESTIONS
1. To select proper blade, consider the type of mate-
rial to be cut as well as to its size and shape. The
SELECT-O-CHART
is a handy reference guide.
2. Use the correct blade speed and correct pressure
for each type of material cut.
3. Always maintain proper blade tension.
4. Lower saw frame carefully so that the blade will
start cutting before full frame feed pressure is ap-
plied to the blade.
5. Reduce feeding pressure for the fi rst two or three
cuts with a new blade.
6. Keep the adjustable blade guide as close as pos-
sible to the material being cut.
7. Keep blade brushes in contact with the blade teeth
at all times.
Recommended Service Kit
for Insurance Against Downtime
2 years
100406-001 Bearing
6
req’d
100066-002
“V” Belt
1 req’d
M-426
Blade Brush
2 req’d