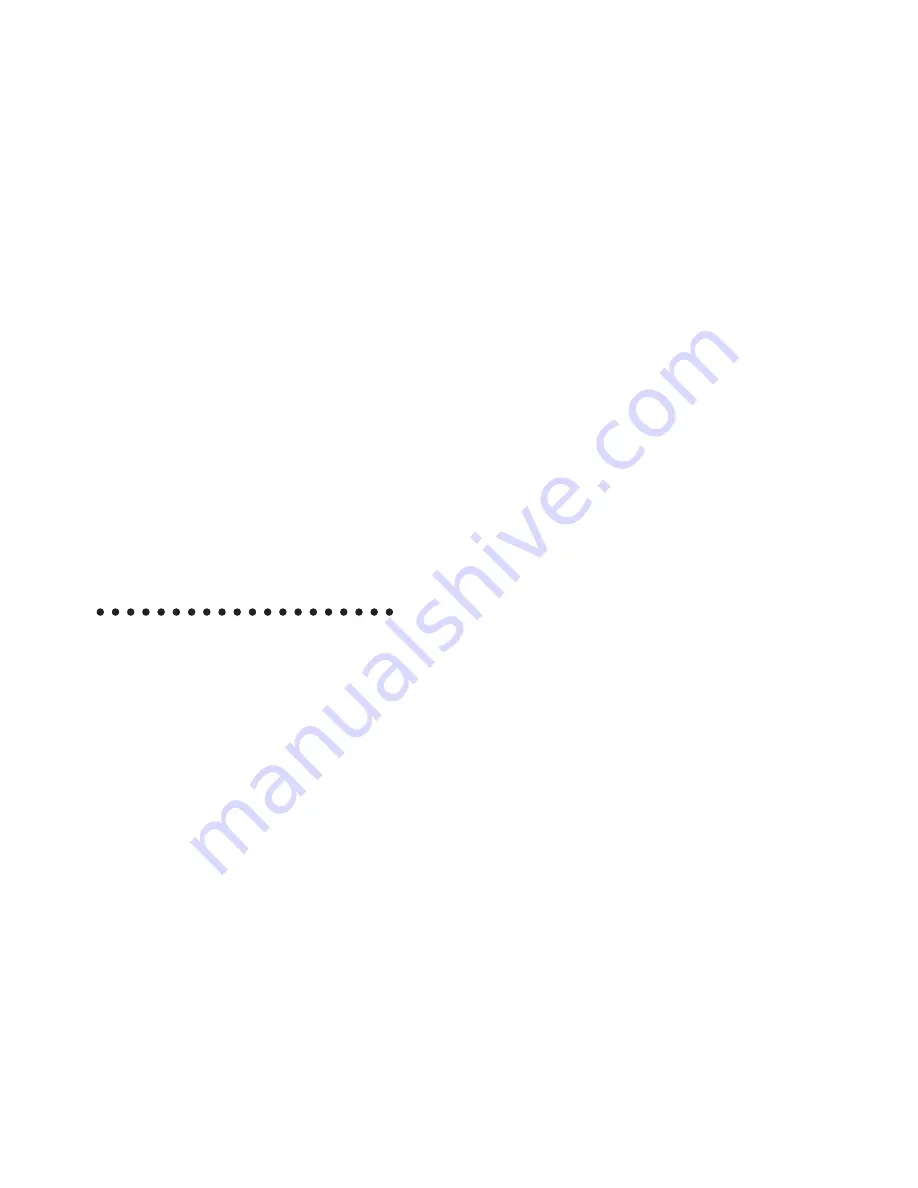
4
DON’T OVER REACH
. Keep proper footing and bal-
ance at all times.
MAINTAIN TOOLS WITH CARE
. Keep tools sharp
and clean for best and safest performance. Follow in-
structions for lubricating and changing accessories.
DISCONNECT TOOLS
before servicing or when
changing accessories such as blades, bits, cutters, etc.
AVOID ACCIDENTAL STARTING
. Make sure the
switch is in OFF position before connecting power
tools.
USE ONLY RECOMMENDED ACCESSORIES
. Con-
sult the owner’s manual for recommended accessories.
The use of improper accessories may be hazardous.
NEVER STAND ON A TOOL
. Serious injury can oc-
cur if the tool is tipped or the cutting tool is accidentally
contacted.
CHECK DAMAGED PARTS
. Before further use of the
tool, a guard, or other part that is damaged, should be
carefully checked to ensure that it will operate prop-
erly and performed its intended function. Check for
alignment of moving parts, breakage, mounting and
any other condition that may affect the tool’s proper
operation. Any guard or part that is damaged should
be properly repaired or replaced.
This excerpt from a survey report does not necessar-
ily refl ect the views and policies of OSHA however it is
presented for your consideration in maintaining work-
place safety.
From
“Machine Guarding -
Assessment of Need”
HEW publication No. (OSHA) 75-173
SUMMARY:
The previous information discussed specifi c machines
and their inherent characteristics and hazards. All ma-
chines, however, require proper power installation and
maintenance. High-speed, rotating cutting tools must
be properly sharpened and well balanced to eliminate
vibration. Saw blades must be properly sharpened
and set to eliminate binding and ensure clean cuts.
Any cutting tool that is cracked or chipped must be dis-
carded.
The work area should be neat, well lighted, properly
ventilated and free of pedestrian or vehicle traffi c. Am-
ple room is needed for stock handling and storage,
the fl oors must be free of slipping or tripping hazards
as many machines have exposed tooling that can be
fallen on.
These items, though they are not specifi c machine
guard needs, are equally important.
It is also interesting to note that operators observed
and questioned by the survey representatives and em-
ployed on some woodworking and metalworking equip-
ment are often new hires with little or no experience
with machine operation. This is substantiated by the
fi nding that proper training programs are almost absent
from industry (Field Supplement, page 8) and by the
fact that the highest percentage of accidents occurs
at a young age (see Field Survey Supplement, page
8). The best example of this is with operators of saws
where the operation seems self-explanatory through
observation. Perhaps the operation is basically sim-
ple; nevertheless, operators should be carefully trained
and enthusiastically motivated to perform safely.
A fi nal observation found through fi eld surveys has to
do with the size of the company versus the number
of unguarded machines (see Field Survey Supple-
ment, page 2). The smaller the company in number
of employees, the larger the percentage of unguarded
machines observed. This illustrates a further need for
machine guards.
The age of the operator, the size of the company, and
the lack of training programs, along with the investiga-
tion of specifi c machines to identify inherent hazards,
establishes a defi nite need for machine guarding. The
fact that a hazard exists and a worker performs in prox-
imity to that hazard will undoubtedly result in an injury.
Because of this, the use of machine guards to divorce
the operator from the hazard to the highest possible
degree is not only desirable but needed. It is the moral
responsibility of the employer and expected benefi t to
the employee to be able to manufacture goods without
occupational injuries.