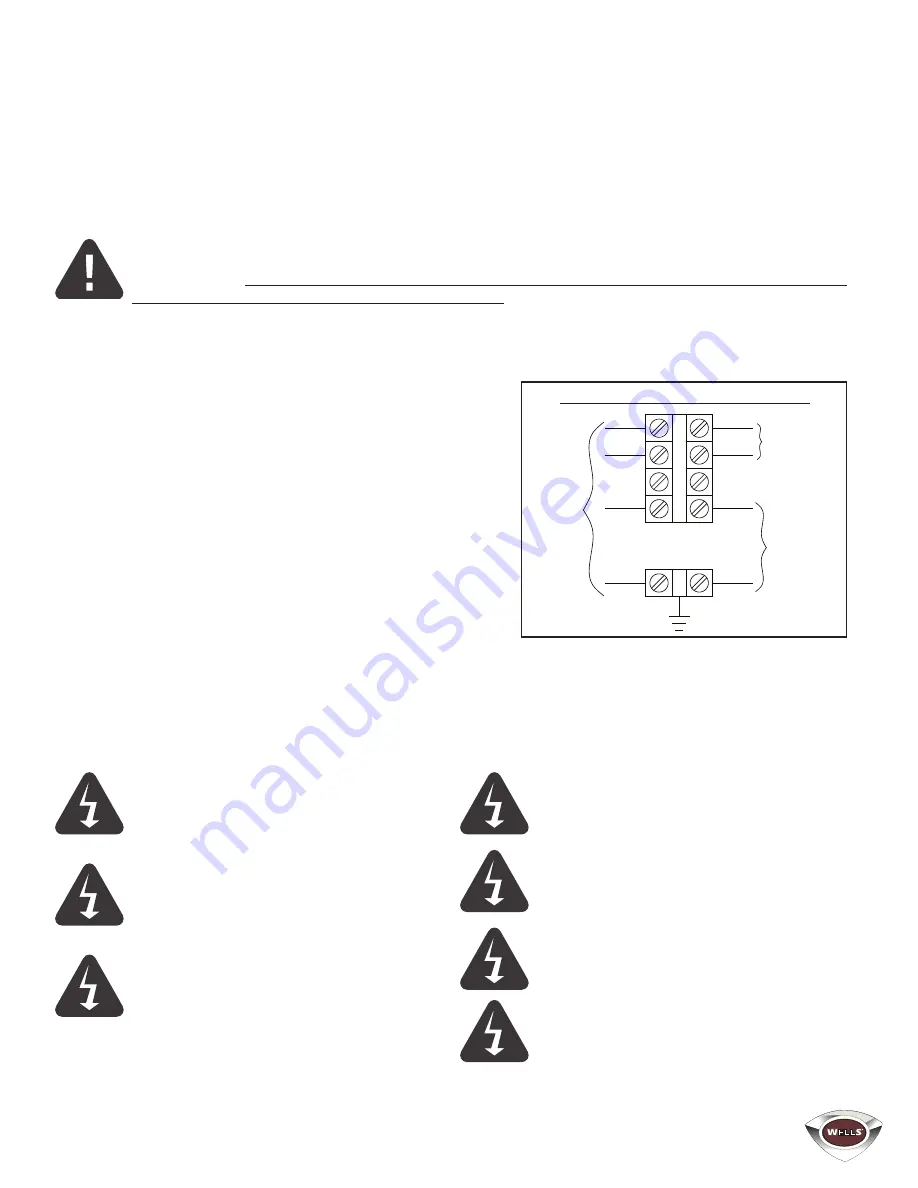
1
GENERAL INSTALLATION INFORMATION
The unit is shipped ready to be hardwired to an electrical box specified for its voltage and amp
draw. If improper electrical supply can not be determined through troubleshooting, contact a
qualified electrician prior to using the unit. Improper electrical installation can void the warranty.
Should you require assistance, contact your local authorized service agent for any service or
required maintenance.
Allow enough space around the induction unit for adequate ventilation and make certain the
cooling fan is not blocked. Additional space from extremely hot devices is recommended as this
unit’s intake air temperature cannot exceed 104° F (40° C). Doing so may result in damage to the
induction unit. Make certain this induction unit is not located near other appliances which may
produce grease vapor, such as fryers, griddles, etc.
Before using the induction unit for the first time, ensure to clean it properly. Refer to the Cleaning
section for cleaning instructions.
ELECTRICAL CONNECTION
Before making any electrical connections to this
unit, check that the power supply is adequate for
the voltage, amperage, phases, and requirements
stated on the rating plate. This equipment must
be installed and connected in accordance with all
applicable federal, state, province, and/or local
electrical codes having jurisdiction by a licensed
electrician. All electrical connections must be
made with COPPER WIRE ONLY in the correct
wire gauge for the application. The induction units
will utilize a terminal block ready to be connected
through a plug and receptacle-type connection or
direct flexible conduit. Do not use rigid conduit to
connect to the supply. ALLOW ENOUGH SLACK in
the wiring to allow for equipment to be moved during installation or any required maintenance and
servicing. Be absolutely certain that the ground connection for the receptacles is properly wired.
Do not connect equipment to power without proper ground connections. Improper grounding
may result in a void to warranty, personal injury, or fatality.
DO NOT CUT OR REMOVE THE
PLUG OR GROUNDING PRONG
FROM THE PLUG ON THE
INDUCTION UNITS.
CONNECT/PLUG UNIT INTO
DEDICATED AC LINE ONLY
SPECIFIED ON THE DATA PLATE
OF THE UNIT.
MAKE CERTAIN THE UNIT IS
POWERED OFF AND UNPLUGGED
PRIOR TO ANY REPAIRS OR
MOVEMENT. ALL REPAIRS SHOULD
BE PERFORMED BY AUTHORIZED
SERVICE TECHNICIANS ONLY.
DO NOT HOSE DOWN
THE UNIT OR THE TABLE/
COUNTER IF THE UNIT IS ON
THE TABLE/COUNTER.
DO NOT IMMERSE OR LET
THE UNIT STAND IN WATER.
KEEP AWAY FROM RUNNING
WATER.
WARNING: Do Not connect
to a circuit operating at more
than 150 volts to ground.
BLACK
RED
WHITE
GREEN
OR BARE
COPPER
BLACK
RED
WHITE
GREEN
RECEPTACLES
MAIN CONTACTOR
L1
L2
N
MAIN SUPPLY
SUPPLY CONNECTION DIAGRAM