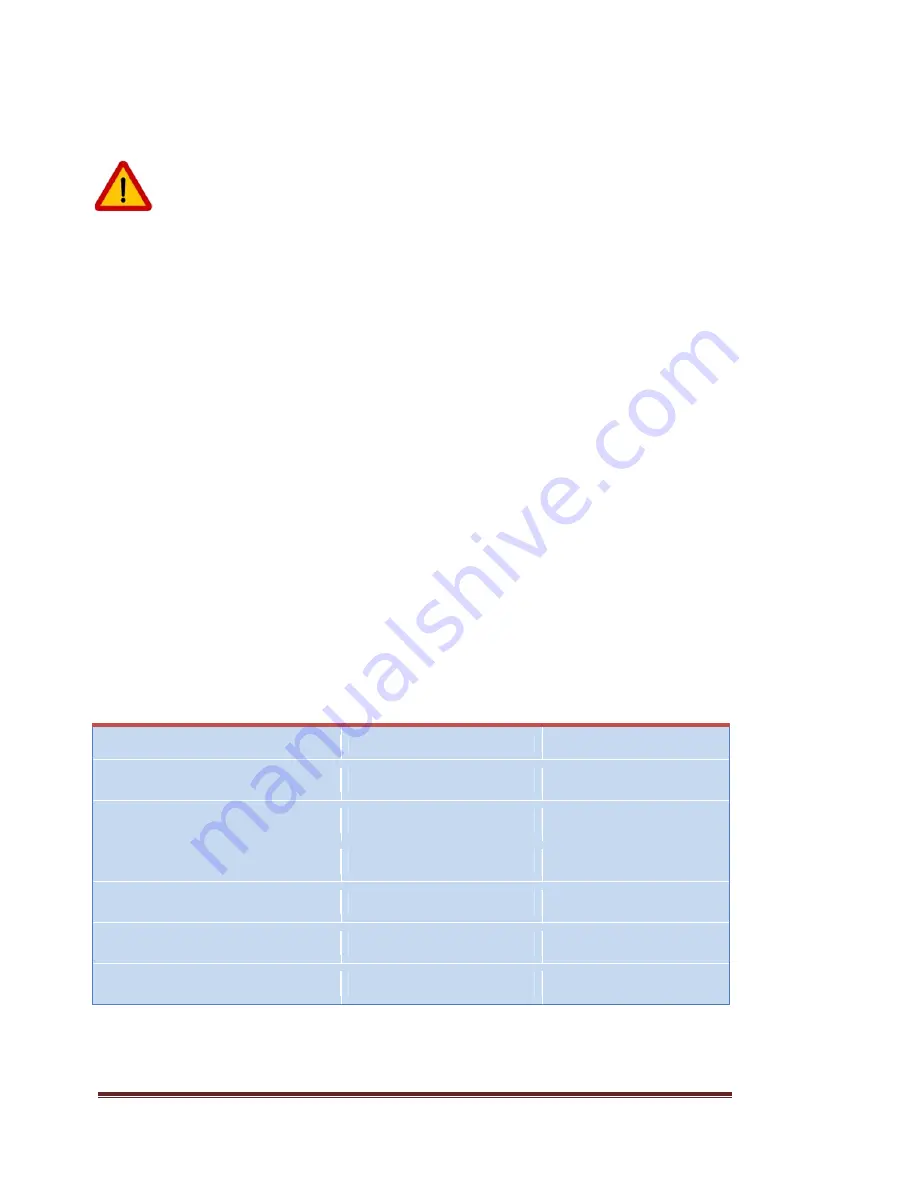
Page 18
Manual no. WM070401
5-2.
Operation
USE SINGLE PHASE 115V/208V/230V POWER SUPPLY.
5-2.1.Switch on the power source.
5-2.2.Set Welding Current to desired value (refer to 5-3 Welding Parameter selection chart).
5-2.3.The display value of digital voltage meter will change when you turn the current knob to
pre-set the welding current. During welding, the meter will reflect actual welding current
output.
5-2.4.When stick welding, drag electrode across workpiece like striking a match; lift electrode
slightly after touching work. If arc goes out electrode was lifted too high. If electrode sticks to
workpiece, use a quick twist to free it.
5-2.5.When TIG welding. Turn on the gas valve on the torch; adjust gas volume to 3-5L/MIN. check
if there is gas leaking.
5-2.6.Touch tungsten electrode to workpiece at weld start point.
Hold electrode to Workpiece for
1-2 seconds
, and then slowly lift electrode. Arc is formed when electrode is lifted. Aim
Tungsten electrode to the welding seam.
5-2.7.After arc is ignited, move the torch along seam evenly. Fine tune the welding parameter to
obtain exquisite welding seam.
5-2.8.After finish operation, turn off the gas valve (for TIG). At the end, turn off welding power
source and wall switch.
5-3. Welding Parameter selection chart
The setting listed below is just for initial commission of the machine. The parameter can be refined
during welding.
STICK:
Electrode diameter (mm)
Welding current (A)
Welding voltage(V)
1.0
20~60
20~23
1.6
44~84
22~24
2.0
60~100
22~24
2.5
80~120
23~25
3.2
100~150
24~26
4.0
140~180
25~27
Table 5.1
TIG:
Summary of Contents for COOLARC 200
Page 1: ...COOLARC 200 Owner s Manual STICK SMAW TIG GTAW ...
Page 3: ......
Page 34: ...Manual no WM070401 Page 29 CoolArc200 Figure 8 1 ...
Page 35: ...Page 30 Manual no WM070401 NOTES WELDKING CoolArc200 power source ...
Page 36: ...Manual no WM070401 Page 31 CoolArc200 SECTION 9 ELECTRIC DIAGRAM Figure 9 1 ...