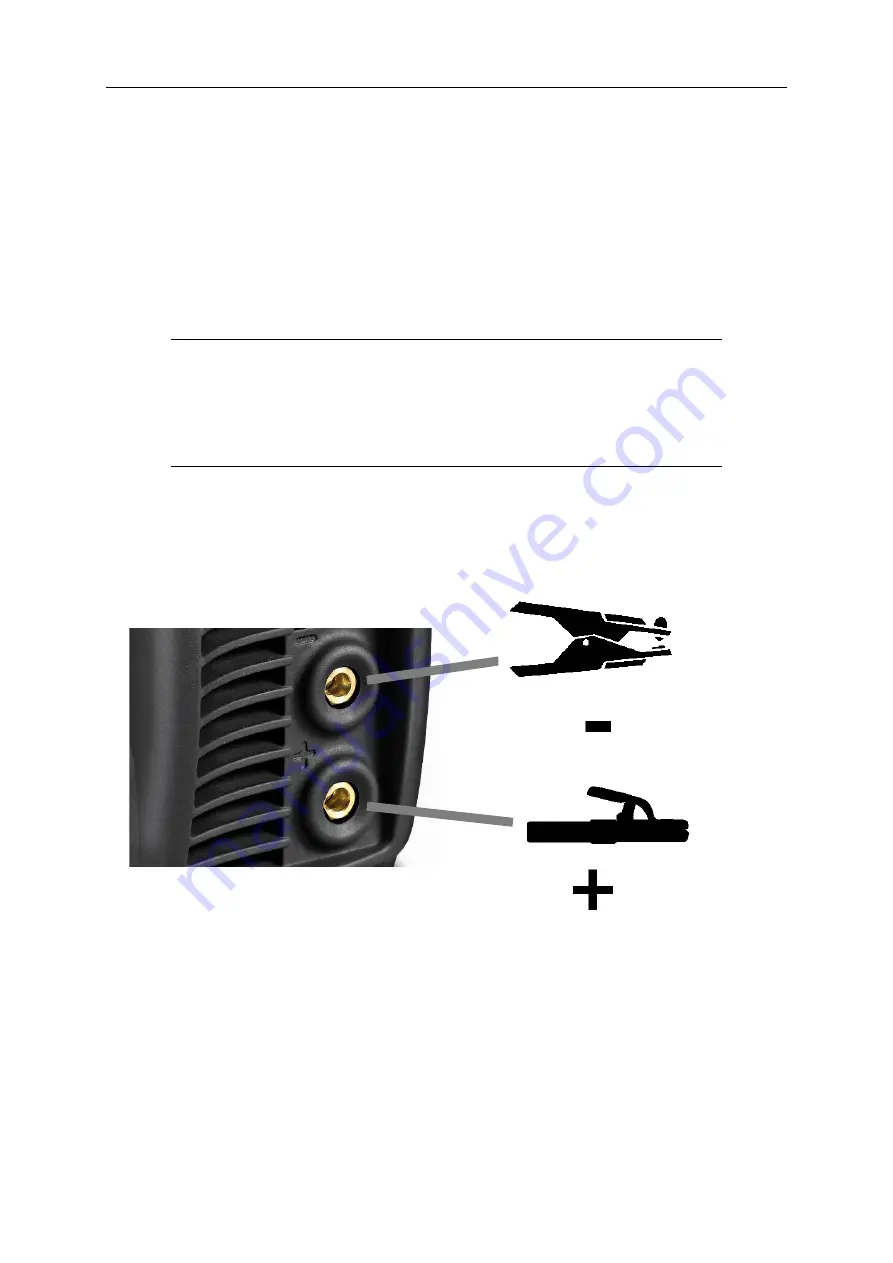
Weldforce 136S & 181S
© Weldclass | E.&O.E.
11
7
BASIC OPERATION
7.1
Stick (MMA) Welding Operation
1.
Connect the earth cable quick connector to the Negative (-) Welding Power Output Socket (5)
2.
Connect the earth clamp to the work piece. Contact with the work piece must be firm contact
with clean, bare metal, with no corrosion, paint or scale at the contact point.
3.
Insert an electrode into the electrode holder and connect the electrode holder and work lead to
the Positive (+) Welding Power Output Socket (1).
NOTE:
This polarity connection configuration is valid for most GP (General Purpose)
MMA electrodes. There are variances to this, also many electrodes will run in either
polarity setting (electrodes positive or electrode negative, with slight difference in
performance. If in doubt, check the electrode specifications or consult the electrode
manufacturer.
4.
Connect the machine to suitable power. Switch the mains power switch (1) to ‘on’ to power up
the machine.
5.
Select the required output current using the Adjustment Knob (4).
6.
You are now ready to weld!
Figure 6