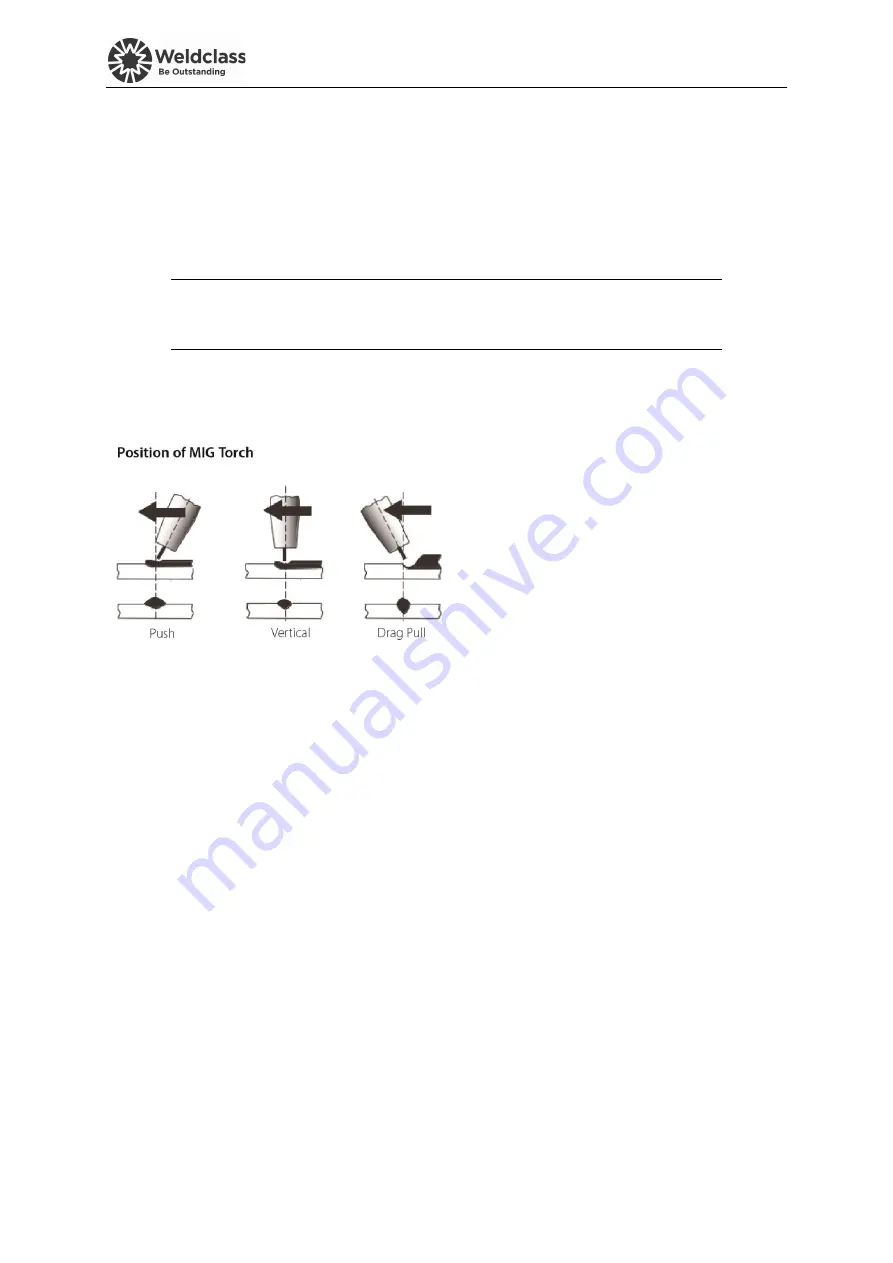
.
52
© Weldclass 2020 | E.&O.E.
11.4
Position of MIG Torch
The angle of MIG torch to the weld has an effect on the width of the weld. The welding torch should be
held at an angle to the weld joint. (See Secondary Adjustable Variables below). Hold the torch so that the
welding seam is viewed at all times. Always wear the welding helmet with proper filter lenses and use the
proper safety equipment.
CAUTION!
Do not pull the welding torch back when the arc is established. This will
create excessive wire extension (stick-out) and make a very poor weld.
The welding wire is not energized until the torch trigger switch is depressed. The wire may therefore be
placed on the seam or joint prior to lowering the helmet.
Figure 40
11.5
Distance from the MIG Torch Nozzle to the Work Piece
The welding wire stick out from the MIG Torch nozzle should be between 10mm to 20mm. This distance
may vary depending on the type of joint and type of wire that is being welded. Generally solid wire is about
10mm and flux-cored/gasless wire about 15-20mm.
11.6
Travel Speed
The speed at which the molten pool travels influences the width of the weld and penetration of the welding
run.
Summary of Contents for WC-210MST
Page 41: ...Weldforce 210MST 250MST Weldclass 2020 E O E 41 Figure 25 Figure 26...
Page 43: ...Weldforce 210MST 250MST Weldclass 2020 E O E 43...
Page 44: ...44 Weldclass 2020 E O E 8 6 Primary Schematic Circuit Diagram Weldforce 210MST Figure 27...
Page 45: ...Weldforce 210MST 250MST Weldclass 2020 E O E 45 Weldforce 250MST...
Page 50: ...50 Weldclass 2020 E O E Figure 34 Figure 35 Figure 36 Figure 37...
Page 83: ...Weldforce 210MST 250MST Weldclass 2020 E O E 83 NOTES...