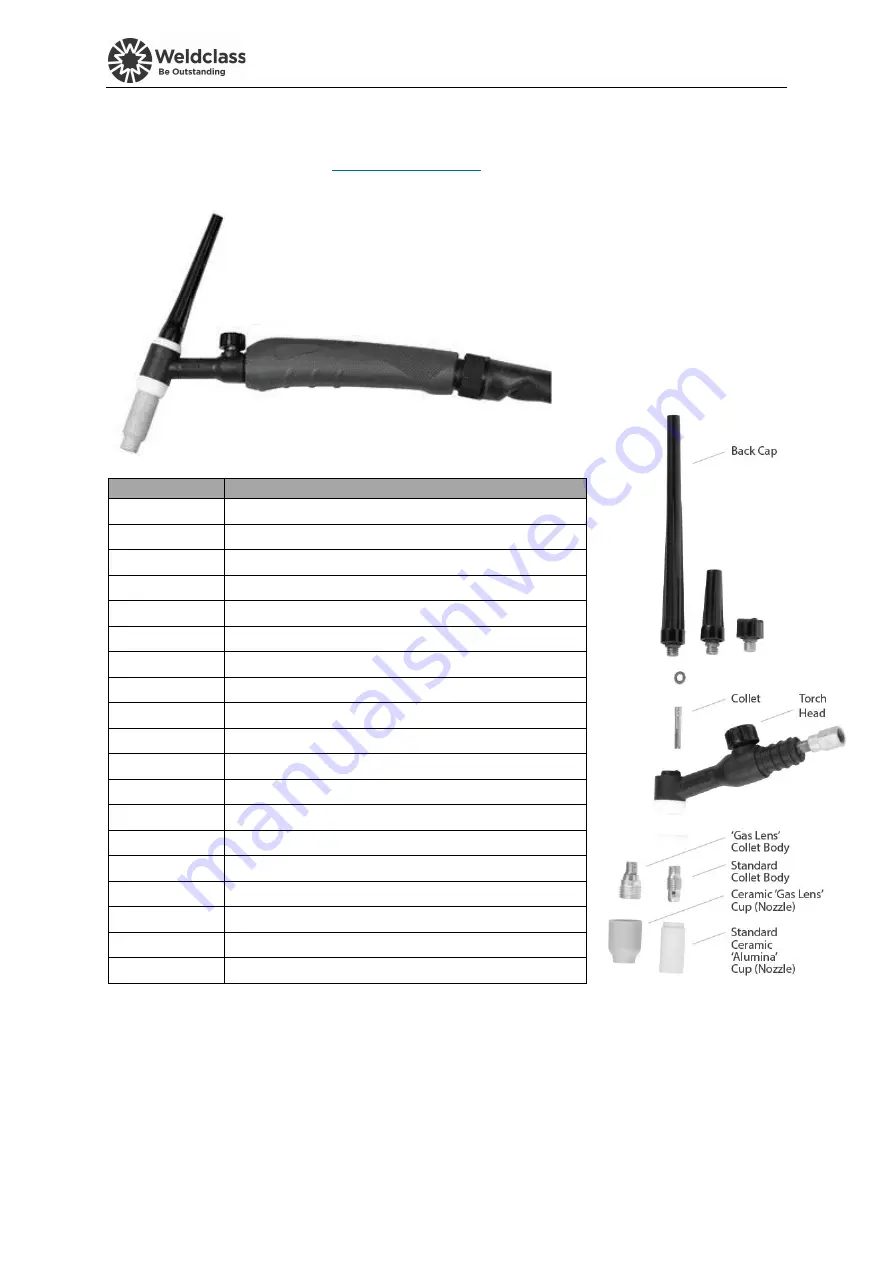
.
38
© Weldclass 2020 | E.&O.E.
8.2
TIG Torch and Spares (Optional Extra):
The compatible TIG torch for this machine is the Weldclass 3-TTU2917V/4 torch.
To view this torch and parts, go to:
Part No.
Description
WC-00992
Complete TIG Torch – 17 Series with Valve 4m
P3-TB17FV
Torch Body - 17FV Flexible (With Valve)
WC-57Y02P
Back cap – Long Pk2
WC-57Y05P
Back cap – Medium Pk2
WC-57Y04P
Back cap – Short Pk2
P3-10N23
Collet – 1.6mm
P3-10N24
Collet – 2.4mm
P3-10N25
Collet – 3.2mm
P3-10N31
Collect Body – 1.6mm Pk2
P3-10N32
Collect Body – 2.4mm Pk2
P3-10N28
Collect Body – 3.2mm Pk2
P3-10N49
TIG Ceramic Cup - #5 7.9mm Pk2
P3-10N48
TIG Ceramic Cup - #6 9.5mm Pk2
P3-10N47
TIG Ceramic Cup - #7 11.1mm Pk2
P3-10N46
TIG Ceramic Cup - #8 12.7mm Pk2
P3-10N45
TIG Ceramic Cup - #10 15.8mm Pk2
WC-05192
TIG Tungsten RE4 – 1.6mm Pk10
WC-05193
TIG Tungsten RE4 – 2.4mm Pk10
WC-05194
TIG Tungsten RE4 – 3.2mm Pk10
Table 12
Figure 24
Summary of Contents for WC-210MST
Page 41: ...Weldforce 210MST 250MST Weldclass 2020 E O E 41 Figure 25 Figure 26...
Page 43: ...Weldforce 210MST 250MST Weldclass 2020 E O E 43...
Page 44: ...44 Weldclass 2020 E O E 8 6 Primary Schematic Circuit Diagram Weldforce 210MST Figure 27...
Page 45: ...Weldforce 210MST 250MST Weldclass 2020 E O E 45 Weldforce 250MST...
Page 50: ...50 Weldclass 2020 E O E Figure 34 Figure 35 Figure 36 Figure 37...
Page 83: ...Weldforce 210MST 250MST Weldclass 2020 E O E 83 NOTES...