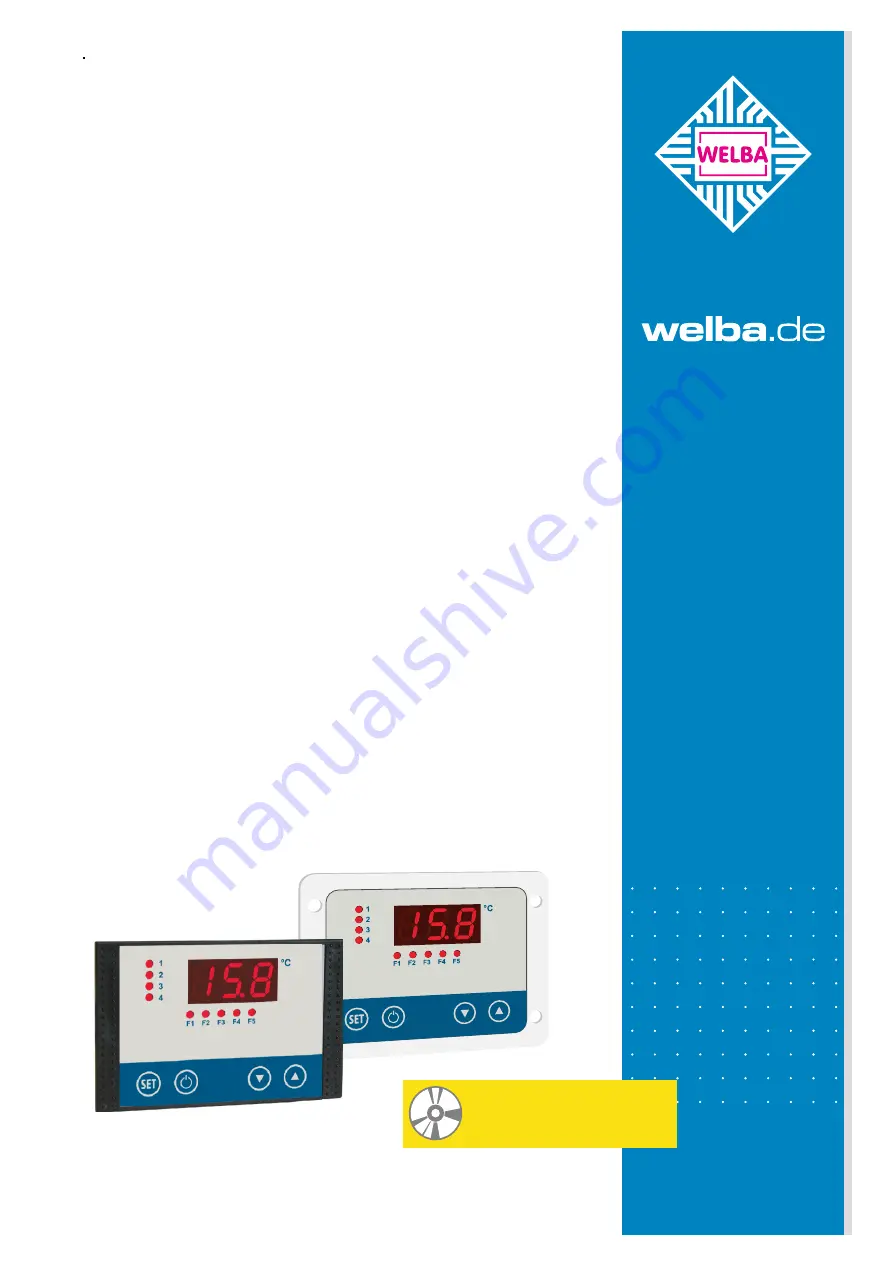
1. Introduction
104781 - MRF-2 | MRH-2 - V2.4 - 22.07.2020
Page 1
Programmable PID multichannel
temperature controller
MRF-2 ...
MRH-2 ...
Installation and operating instructions
for plant engineering companies
Software version V2.4
Programmable via
configuration software
WELBA „KONSOFT"
Measuring - Controlling - Regulating
All from the same source