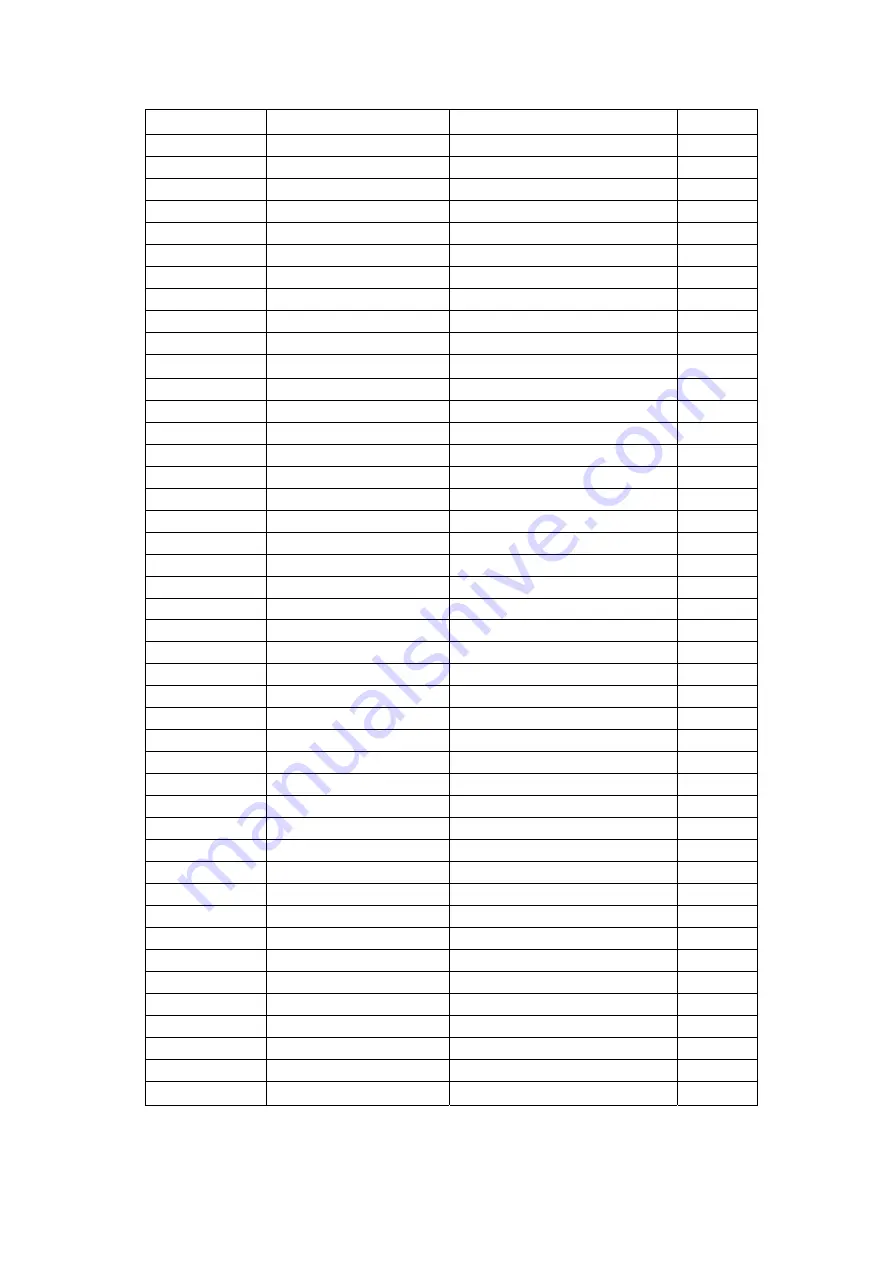
42
ELECTRICAL BOX ASSEMBLY
Parts No.
Description
Specification
Qty
1
Timing Knob
1
2
Screw
4
3
Nut
4
4
Lable
1
5
R/F Swich
ZH-A EN61058
1
6
Speed Display
Optional
1
7
Screw
2
8
Magnetic Swich
1
9
Screw
4
10
Electrical Plate
1
11
Potentiometer
WX 14-12
1
12
Electrical Box
1
13
Emergency Stop
XB2-BS542
1
14
Limited Switch
LXW5-11Q1
6
15
Nut
4
16
Speed Control Board
1
17
Cover
1
18
Screw
4
19
Fuse Holder
1
20
Fuse (10A)
1
21
Strand Relief
1
22
Plug
1
Summary of Contents for WBL290F
Page 1: ...WBL290F 11 1 2 x 29 METAL LATHE with DRO User Manual...
Page 27: ...Threading Feed TabIe...
Page 29: ...PARTS LISTS...
Page 30: ......
Page 31: ...25 Headstock and Driving Assembly...
Page 34: ...28 Gearbox Assembly Gearbox Assembly...
Page 37: ...31 Top slide Cross slide Carriage Assembly...
Page 40: ...34 Apron Assembly...
Page 43: ...37...
Page 45: ...39 Bed Assembly...
Page 47: ...ELECTRICAL BOX ASSEMBLY 2...