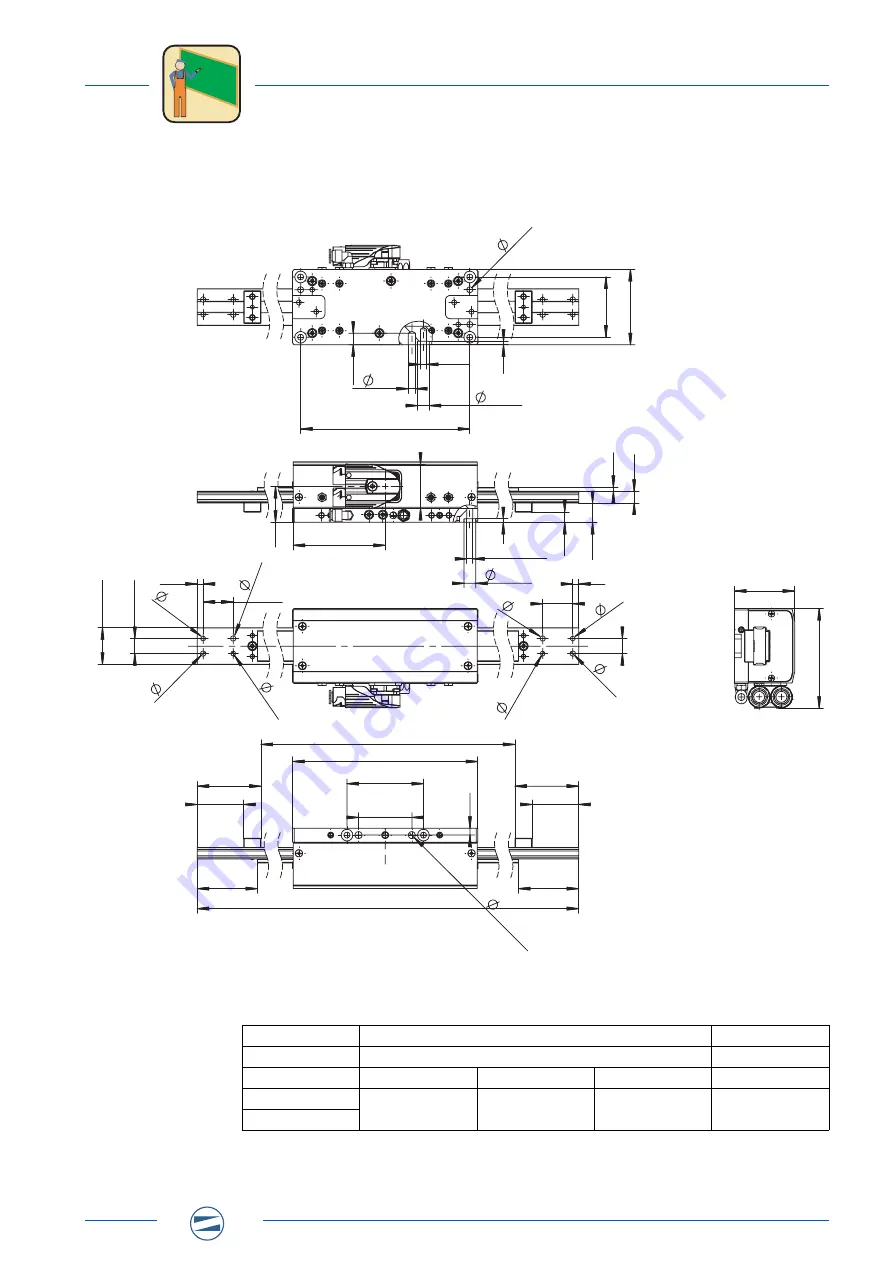
Linear motor shafts HL50 - HL100 R07-2011
18/48
WEISS
Product description
3.3 Technical data
3
3.3.7
Dimensions
3.3.7.1 Linear motor shaft HL50
Tolerance of the drill holes and pinholes:
±
0.02 mm
Measurement table:
Dimensions in mm
3
,3
1
0
H7
79,5
x 9 tief
8
,7
1
6
,7
10
3
M6
3
8
3
1
5
1
3
4
H
7
26
4,5
5
3
1
,8
1
3
4
4,
5
H
7
26
52
8
6
,3
6
46
40
40
160
x1
0
H
7
52
66
55
A
55
L
2x
6
52
H7
146
6
5
2
3
6
6
5
1
0
M
10
H7
3x
5
H
7
4,5
4
H7
4
H
7
4
,5
Stroke
L
A
at numbers holding brake
0
1
2
150
Hub + 160
Hub + 209
Hub + 258
L + 110
300
i i i i i i i i i i i i i i i i i
i i i i i i i i i i i i i i i i i
i i i i i i i i i i i i i i i i i
i i i i i i i i i i i i i i i i i