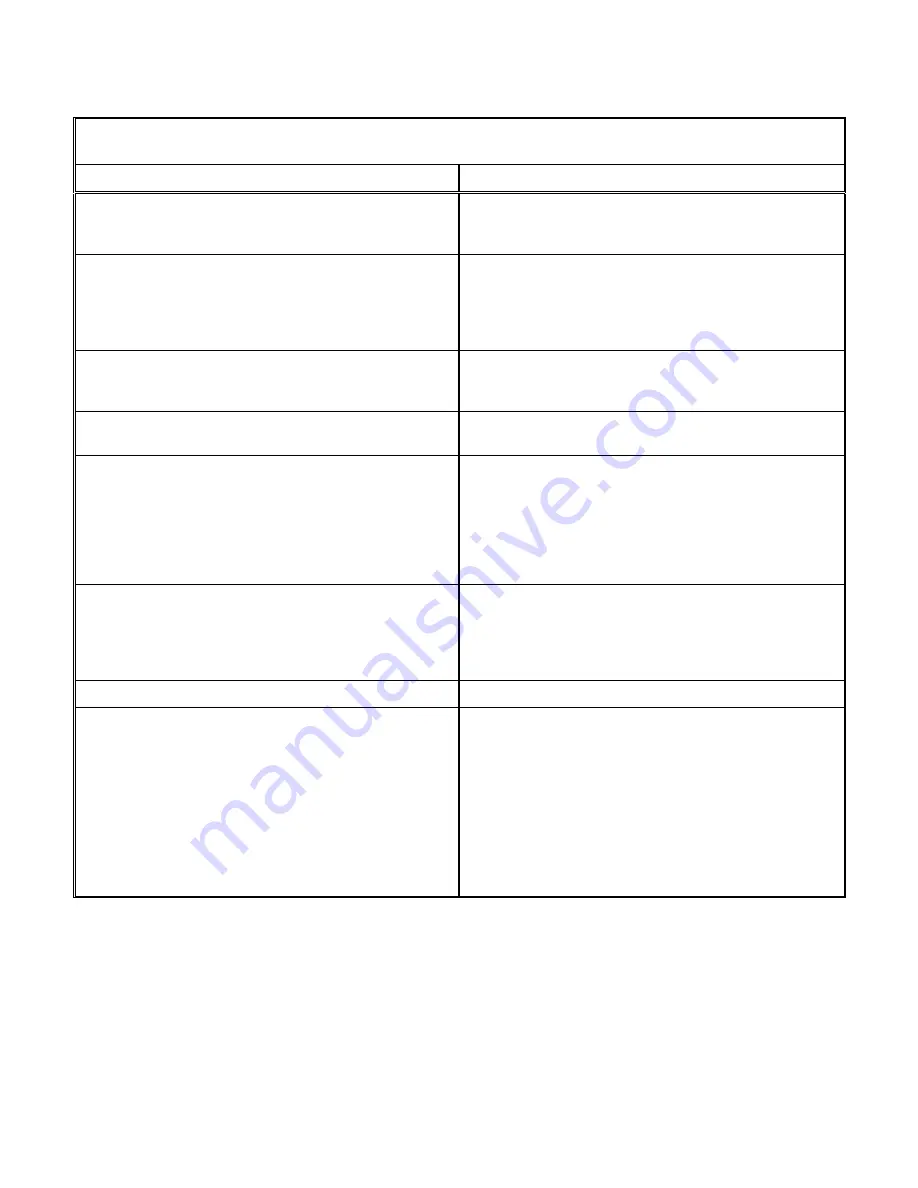
27
B.
NOT ENOUGH LIQUID DELIVERED AT END DELIVERY POINT
OR THROUGH FLOW METER
Possible Causes
Corrective Action
1. Air Leak in Suction Line.
Suction line can be tested by shutting off or plugging
inlet and putting line under pressure. A gauge will
indicate a leak with a drop of pressure.
2. Speed Too Low.
Slipping drive belts – check belt tension. Check driver
sheave and verify correct size for required speed.
Check whether motor is directly across-the-line and
receiving full voltage. Frequency may be incorrect,
motor may have an open phase.
3. Wrong rotation.
Check motor rotation with required pump rotation.
Pump rotation is clockwise viewed from manifold end of
pump.
4. Obstruction in Liquid Passages.
Dismantle pump and inspect passages of pick-up tube,
rotor cover and manifold. Remove obstruction.
5. Discharge Head Too High.
Total system head greater than head for which pump
designed. Check pipe friction losses. Larger piping
may correct condition. Are valves wide open? Increase
pump speed to develop greater differential pressure.
CAUTION – Brake HP of pump varies as the cube of
the speed; therefore, any increase in speed means
considerable increase in power demand.
6. Suction Lift Too High.
If no obstruction at inlet, check pipe friction losses.
However, static lift may be too great. Measure with
mercury column or vacuum gauge while pump
operates. If static lift is too high, liquid to be pumped
must be raised or pump lowered.
7. Suction or Discharge Line Partially Plugged.
Unplug line.
8. Inlet Cavitation.
Insufficient NPSH (Net Positive Suction Heat) available.
Available NPSH must always equal or exceed the
required NPSH of the pump. Depending on installation:
A.
Increase inlet pressure to pump.
B.
Reduce inlet pipe friction losses.
C. Increase height of suction vessel.
D. Pressurize suction vessel.
E. Lower the pump.