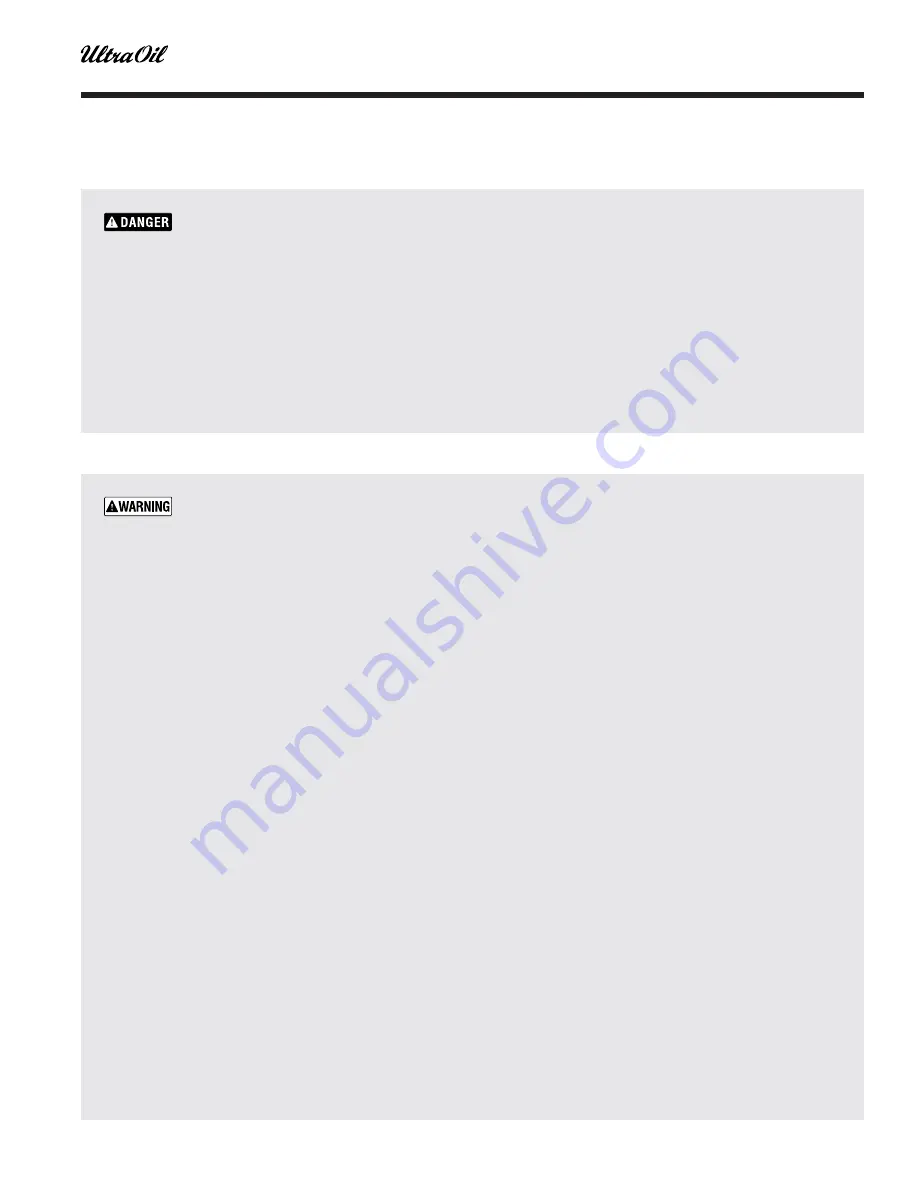
®
WATER
BOILER
—
Boiler Manual
Please read before proceeding
Read all instructions —
s 2EADALLINSTRUCTIONSINCLUDINGTHISMANUALTHEBURNER
manual and any related supplements. Perform steps in
the order given. Failure to comply could result in severe
personal injury, death or substantial property damage.
When servicing boiler —
s 4OAVOIDELECTRICSHOCKDISCONNECTELECTRICALSUPPLYBEFORE
performing maintenance.
s 4OAVOIDSEVEREBURNSALLOWBOILERTOCOOLBEFOREPERFORM
-
ing maintenance.
Boiler operation —
s $ONOTBLOCKmOWOFCOMBUSTIONORVENTILATIONAIRTO
burner.
s 3HOULDOVERHEATINGOCCURORFUELSUPPLYFAILTOSHUTOFFDO
not turn off or disconnect electrical supply to circulator.
Instead, shut off the fuel supply at a location external to
the appliance.
s $ONOTUSETHISBOILERIFANYPARTHASBEENUNDERWATER
Electrical and mechanical failures may cause electric
shock and fire risks. Immediately inspect chimney or vent,
boiler, burner and controls. Clean the boiler flueways and
replace all electrical and mechanical controls; all electrical
wiring; oil burner and controls; insulation and chamber
lining.
Boiler firing rate —
s $ONOTREDUCETHElRINGRATEOFTHEBOILER5SEONLYTHEOIL
NOZZLESIZESPECIlED2EDUCEDINPUTWILLCAUSECONDENSA
-
tion in the boiler and vent piping.
Ceramic fiber materials —
s 4HEBOILERCONTAINSCERAMIClBERMATERIALS5SECARE
when handling these materials per instructions on
page 26 of this manual. Failure to comply could result
in severe personal injury.
Boiler water —
s 4HOROUGHLY mUSH THE SYSTEM WITHOUT BOILER CON
-
nected) to remove sediment. The boiler heat exchanger
can be damaged by build-up or corrosion due to sedi-
ment.
s $O NOT USE PETROLEUMBASED CLEANING OR SEALING
compounds in boiler system. Gaskets and seals in the
system may be damaged. This can result in substantial
property damage.
s $ONOTUSEhHOMEMADECURESvORhBOILERPATENTMEDI
-
CINESv 3ERIOUS DAMAGE TO BOILER PERSONNEL ANDOR
property may result.
s #ONTINUAL FRESH MAKEUP WATER WILL REDUCE BOILER
life. Mineral buildup in boiler sections reduces heat
transfer, overheats the sections, and causes failure.
Addition of oxygen carried in by make-up water can
cause internal corrosion. Leaks in boiler or piping
must be repaired at once to prevent make-up water.
s $ONOTADDCOLDWATERTOHOTBOILER4HERMALSHOCK
can cause heat exchanger to crack.
Freeze protection fluids —
s 7HENUSINGANTIFREEZE$ONOTUSEAUTOMOTIVEETH
-
YLENEGLYCOLUNDILUTEDORPETROLEUMBASEDANTIFREEZE
3EETHE7!2.).'ONPAGEFORMOREINFORMATION
Follow the guidelines below to prevent possible severe personal injury, death or substantial property damage.
Follow the guidelines below to prevent severe personal injury, death or substantial property damage.
Fuel
s $O NOT USE CRANKCASE DRAININGS OR ANY OIL CONTAINING
GASOLINE3EEBURNERMANUALFORPROPERFUELOIL
s .EVERBURNGARBAGEORPAPERINTHEBOILER.EVERLEAVE
combustible material around boiler.
Do not tamper with burner/controls
s !LWAYS FOLLOW SPECIlC INSTRUCTIONS WHEN STARTING UP
boiler or performing routine maintenance or service.
Do not start burner if:
s $ONOTATTEMPTTOSTARTBURNERWHENEXCESSOILHASAC
-
cumulated in combustion chamber, when unit is full of
vapor, or when combustion chamber is very hot.
s $ONOTSTARTBURNERUNLESSBREECHINGANDBURNERMOUNT
-
ing door are secured in place.
Part number 550-141-986/0112
5