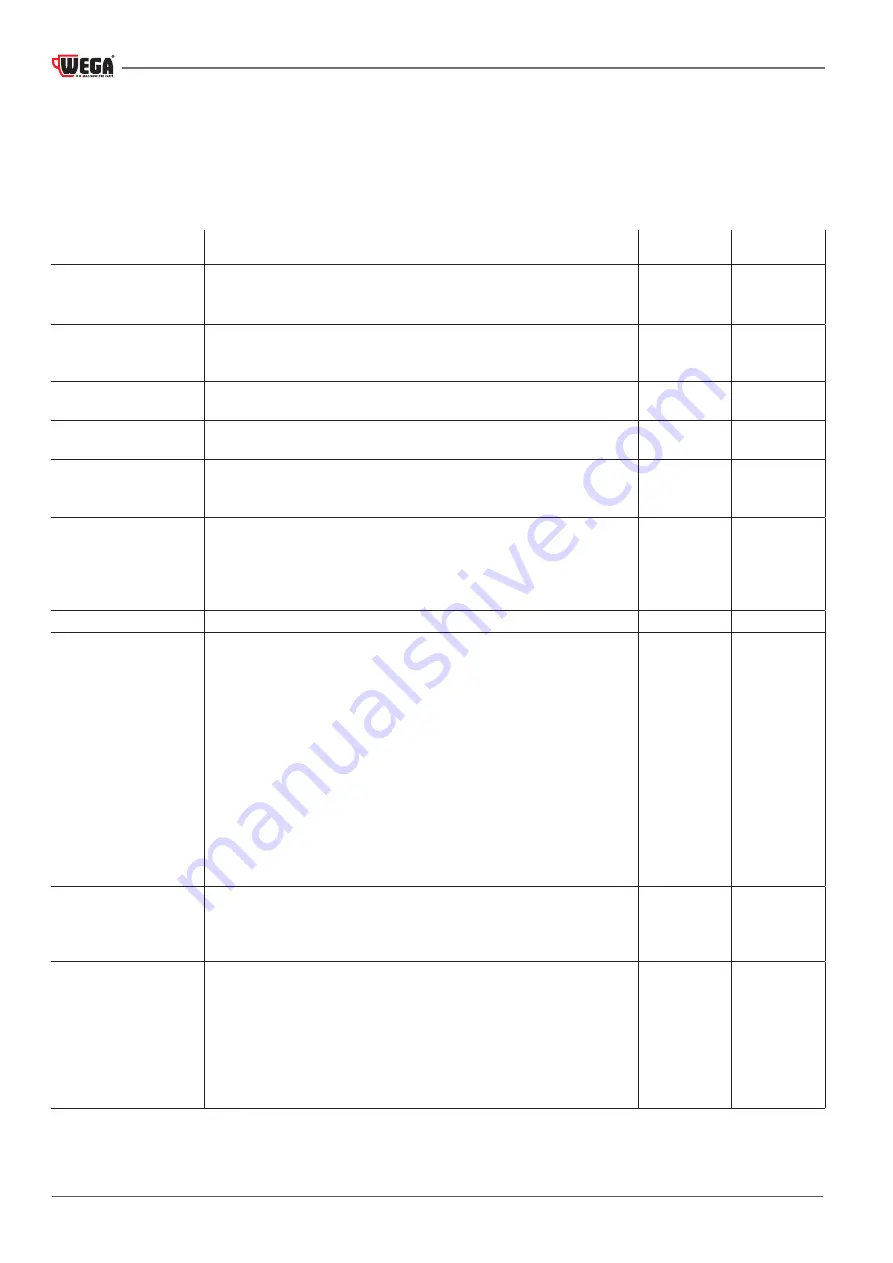
34
of
68
TECHNICIANS manual
8.3
Maintenance
8.3.1 Scheduled
maintenance
Perform the following maintenance according to the
specified frequency.
In case of intensive use of the machine the checks
need to be performed in smaller intervals.
Component
Type of intervention
Quarterly
Yearly
GAUGE
Check the boiler pressure, which must be between 0.8 and 1.4 bar.
Periodically check water pressure during coffee dispensing: check the pressure
indicated on the gauge, which must be between 8 and 9 bar inclusive.
X
FILTERS and PORTAFILTERS
Check the condition of the filters. Check for any damage on the edge of the filters
and check whether any coffee grounds settle in the coffee cup and replace filters
and/or filter holders, as required.
X
DISPENSING UNIT
Replace the perforated disk and under cup seal, as indicated in par. "8.3.4
Dispensing group maintenance" on page 34 .
X
WATER FILTER
Replace the water filter cartridge at the frequency indicated by the manufacturer.
The presence of scale in the hydraulic system indicates the need for its replacement.
X
WATER SOFTENER
Carry out the regeneration as indicated by the Manufacturer.
Use care in areas where the water is very hard. It will be necessary to regenerate at
more frequent intervals, especially in case of intensive use of the machine.
X
GRINDER-DOSER
Check the ground coffee dose (about 7 grams per time); check the degree of
grinding. The grinders must always have sharp cutting edges. Their deterioration
is indicated by the presence of too much powder in the grounds. We recommend
calling the Qualified Technician to replace the flat grinders after every 400/500 kg of
coffee. For conical grinders, replace every 800/900 kg.
X
BOILER
Replace the water in the boiler as indicated in par. 6.11 on page 34.
X
BOILER
Replace the heating element in case of failure or malfunctioning.
Do not replace the heating element with a more powerful one. Before making any
changes, contact the Manufacturer.
If the thermostat of the heating element is triggered, reset it by pressing the central
button of the thermostat. However, before trying to operate the machine, verify the
causes of the blockade of the water feeding the boiler.
If the boiler insulation needs to be removed, restore the insulation after
maintenance.
Remove and clean the boiler level probes.
Check for lime scale deposits on the heating element, on the exchanger (inside and
out).
A strong presence of limestone indicates that the water filter has not been replaced,
or that the softener has not been regenerated.
When replacing any components, always replace the relative gasket as well.
X
SAFETY VALVE
SCNR VALVE
NEGATIVE PRESSURE VALVE
Check that the safety valves, non-return drain valves, and pressure valves are
operating properly, as indicated in par. 8.3.5 - 8.3.6 - 8.3.7 on page 34 .
If their replacement becomes necessary due to failure, repeat the check with the
new valve installed.
X
HYDRAULIC CIRCUIT
Verify the presence of lime scale deposits in the hydraulic circuit.
When replacing any components, always replace the relative gasket as well.
A strong presence of limestone in the hydraulic circuit of the machine indicates
that the water filter has not been replaced, or that the softener has not been
regenerated.
Use care in areas where the water is very hard. It will be necessary to replace the
water filter more frequently, or regenerate the softener at more frequent intervals,
especially in case of intensive use of the machine.
X
Summary of Contents for 1GR Series
Page 67: ......