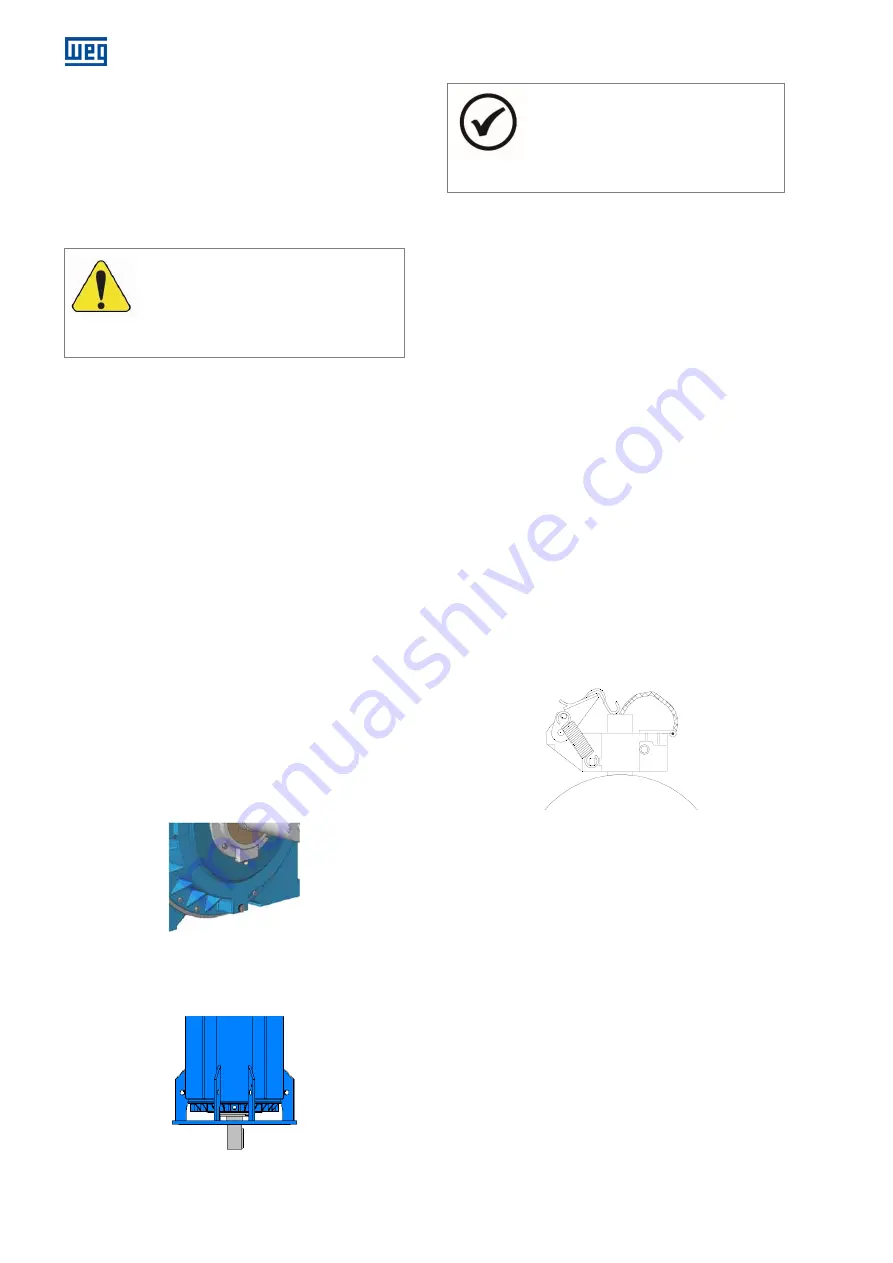
38 l
Installation, operation and maintenance manual – Squirrel cage motor – W Line - Horizontal and vertical 11239449
7.4.2
Reimpregnation
If any layer of resin on the windings is damaged during
cleaning or inspection, such parts must be corrected with
adequate material (in this case, consult WEG).
7.4.3
Insulation Resistance
The insulation resistance must be measured after the
completion of all of the maintenance procedures.
ATTENTION
Before putting the motor back into operation,
it is essential to measure the winding
insulation resistance and ensure that the
measured values meet the specifications.
7.5
COOLING SYSTEM
MAINTENANCE
Inspect and clean the cooling channels periodically
according to the maintenance plan of this manual;
The external part of the frame and the water
connections must be kept in good conditions;
If there is a freezing risk, antifreeze additive must be
used in the cooling water.
Add additives to the cooling water in proper quantities
for protection against corrosion and algae growth;
The type and amount of additives used must be
specified by the manufacturer of these additives and in
accordance with the environmental conditions where
the motor is installed.
7.6
VIBRATION
Any evidence of increase in the unbalance or vibration of
the motor must be investigated immediately.
7.7
MOTOR OUT OF OPERATION
When the motor is stopped, water may condense inside.
In horizontal motors, this water must be removed through
the drain located at the lowest point of the end shields, as
shown in Figure 7.1.
Figure 7.1: Drain of horizontal motors
In vertical motors, the drain is located in the motor lower
end shield, as show in Figure 7.2.
Figure 7.2: Drain of vertical motors
NOTE
When the motor is equipped with a water
leak sensor, it also serves as a drain, and
must be removed in order to drain the
condensed water from inside the motor.
If the motor remains stopped in environments with
negative temperatures, the freezing of the motor cooling
circuit water must be prevented. This can be done by
draining all the water from the frame or by using
antifreeze additives in the water;
In order to remove the water from the frame of
horizontal motors, disconnect the water supply hoses
and inject compressed air into one of the water inlets
until it drains out completely;
In order to remove the water from the frame of vertical
motors, disconnect the water supply hose and allow it
to drain completely through the lower opening;
For storage during long periods, follow the procedures
described in this manual;
Turn on the space heaters so that the temperature
inside the motor be kept slightly above the ambient
temperature, avoiding water condensation and
consequent drop of the winding insulation resistance
and oxidation of metallic parts.
7.8
SHAFT GROUNDING DEVICE
The shaft grounding brush (if any) avoids the circulation of
electric current through the bearings, which is detrimental
to their operation. The brush is put in contact with the
shaft and connected by a cable to the motor frame, which
must be grounded. Make sure that the brush holder
fastening and its connection to the frame have been made
correctly.
Figure 7.3: Shaft grounding brush
Drying oil is used to protect the motor shaft against rust
during transportation. In order to ensure the proper
operation of the grounding brush, this oil, as well as any
residue between the shaft and the brush, must be
removed before starting the motor. The brush must be
constantly monitored during operation, and it must be
replaced by another one of the same quality (granulation)
at the end of its useful life.
7.9
ENCODER MAINTENANCE
The correct installation of the encoder (if any) is very
important for its operation. Both disassembly and
assembly must be done by skilled and trained personnel,
according to the procedures contained in the specific
manual of the equipment manufacturer.
If any further explanations are necessary, consult WEG.
Shaft