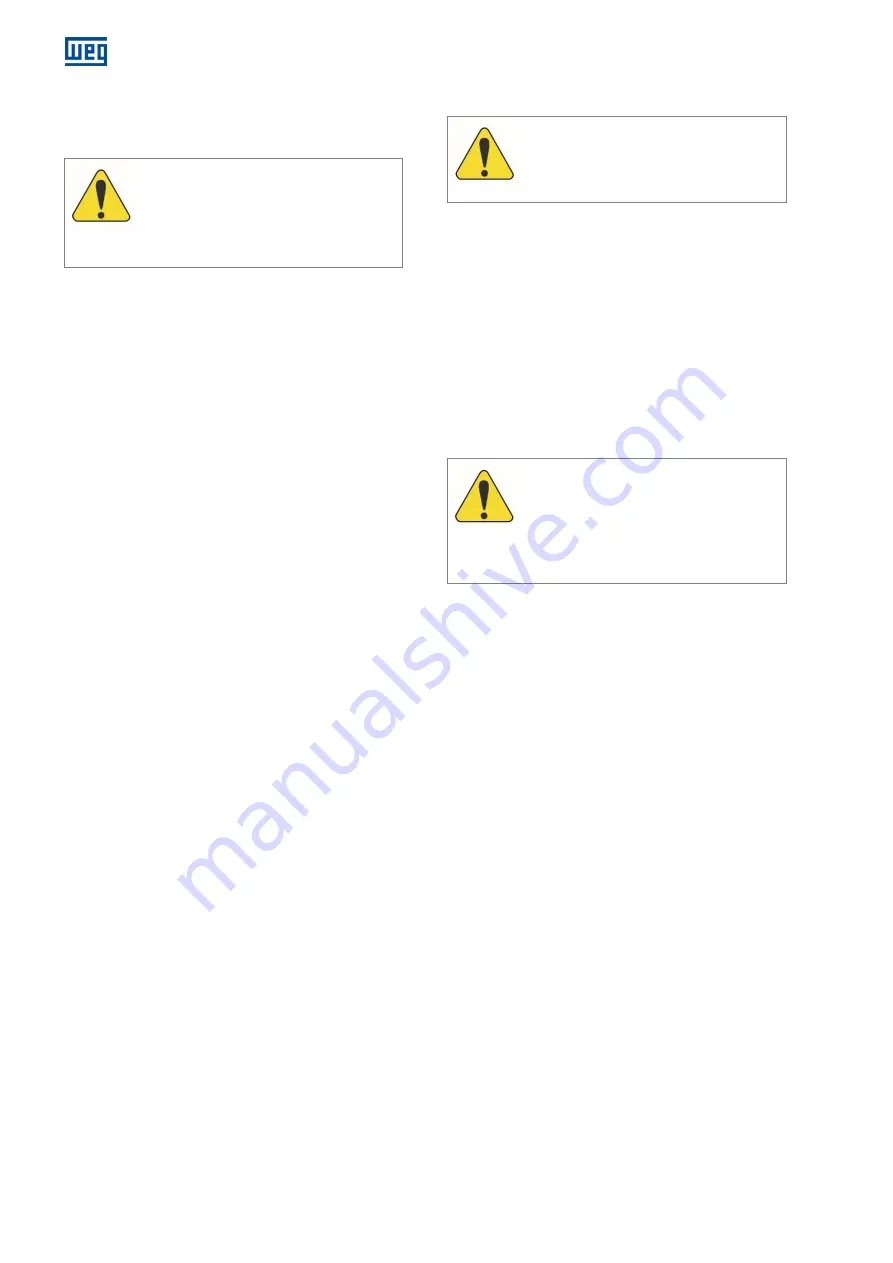
16 l
Installation, operation and maintenance manual – Squirrel cage motor – W Line - Horizontal and vertical 11239449
The extended storage instructions are valid for motors
that remain stored for long periods (two months or more)
before start-up or motors already installed that are in a
prolonged stoppage, considering the same period.
ATTENTION
For extended periods of stoppage or
storage, the water inside the frame must be
drained (WGM motors with water-jacket
cooling).
3.3.2.1
Storage location
In order to ensure the best storage conditions for the
motor during long periods, the chosen location must
strictly meet the criteria described in sections 3.3.2.1.1
and 3.3.2.1.2.
3.3.2.1.1
Indoor storage
In order to ensure better storage conditions for the motor,
the storage site must comply strictly with the criteria
described below:
The storage site must be closed, covered, dry, free of
air contaminants (moisture, vapor, dust, particles and
aggressive fumes) and free of flooding;
The site should be protected against sudden
temperature variations, humidity, rodents and insects;
Vibration-free location, to avoid damaging to the motor
bearings;
The floor must be of leveled concrete with resistant
structure to support the motor weight;
Must have system to fire detection and extinguishing;
Be provided with electricity for supplying the space
heaters with power failure detection system;
Exclusive site to store electrical machines (do not mix
with other equipment and/or products that could
prejudice the correct motor storage);
Site with facilities of cargo handling services, suitable to
allow the motor handling and removal;
There must be no gas present, such as chlorine, sulfur
dioxide or acids;
The site must have ventilation system with air filter;
Ambient temperature between 5°C and 50°C, and
should not present sudden temperature variation;
Relative air humidity <50%;
Must have prevention against dirt and dust deposition;
The motor should be stored on a suitable metal base
that prevents the absorption of moisture from the floor.
If any of these requirements is not met in the storage site,
WEG suggests that additional protections be added to the
motor package during the storage period, as follows:
A closed wooden crate or the like with an electrical
installation that allows the energization of the space
heaters;
If there is a risk of infestation and fungus formation, the
package must be protected in the storage place by
spraying it or painting it with appropriate chemicals;
The package preparation must be prepared carefully by
an experienced person.
3.3.2.1.2
Outdoor storage
ATTENTION
Outdoor storage of the motor is not
recommended.
In case outdoor storage is unavoidable, the motor must be
packed in specific packaging for such conditions, as
follows:
For outdoor storage (exposed to the weather), besides
the packaging recommended for indoor storage, the
package must be covered with protection against dust,
moisture and other odd materials, using resistant
canvas or plastic.
The package must be placed on platforms or
foundations that ensure protection against dirt and
moisture and prevent it from sinking into the soil;
After the package is covered, a shelter must be erected
to protect it against direct rain, snow and excessive sun
heat.
ATTENTION
In case the motor remains stored for long
periods (two months or more), it is
recommended to inspect it regularly as
specified in the section 3.3.3.9
of this
manual.
3.3.2.2
Separate parts
If parts are supplied separately (terminal boxes, heat
exchanger, end shields, etc.), these parts must be
mounted on motor to store it;
Spare parts must be stored in an adequate place, as
specified in sections 3.3.2.1.1 and 3.3.2.1.2 of this
manual.
The relative humidity inside the package must not
exceed 50%.
Rolling bearings must not be subject to shocks, falls or
storage with vibration or humidity, which can cause
marks on the internal tracks or on the balls, reducing
their useful life.
3.3.3
Preservation during the storage
3.3.3.1
Space heater
Space heaters must remain powered during storage to
avoid moisture condensation inside the motor and ensure
that the winding insulation resistance remains within
acceptable levels.
The space heaters drive circuit must be unique and the
voltage and current of this circuit must be measured and
recorded monthly.
It is recommended that a signal be installed near the
motor to indicate that the space heaters are energized.