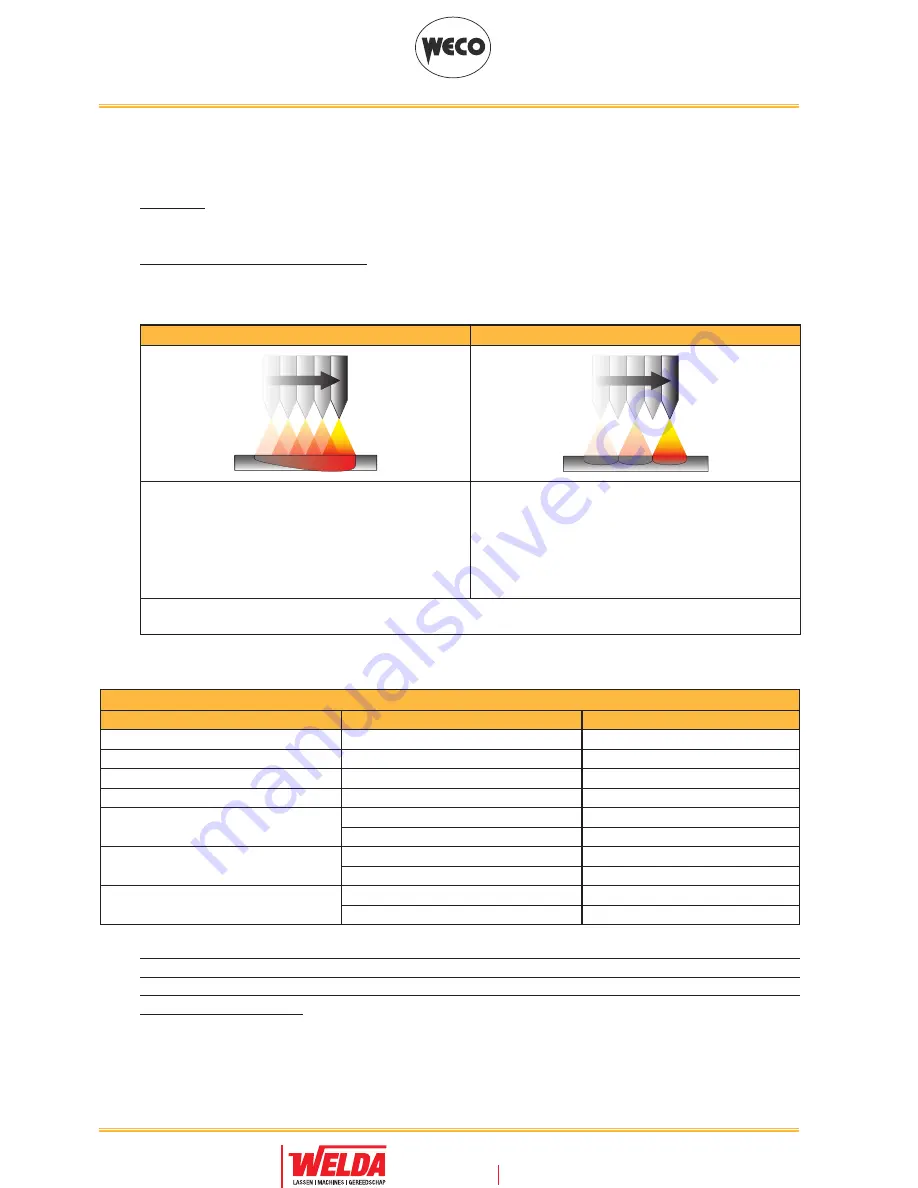
WELD THE WORLD
Cod. 006.0001.2000
19/07/2018 V.2.0
Discovery 221AC/DC Evo
Discovery 300AC/DC Evo
38
ENGLISH
- MULTI TACK
○ This consists of continual welding that allows optimum control of the thinnest gauge sheets/
bevels with irregular shapes.
-
Benefits:
•
Major reduction in oxidisation with the absence of deformations.
•
This parameter allows thin gauge sheet to be welded without deformation.
-
Consequences of a higher value:
•
Welding of thinner gauge sheet without deformation.
•
Less melting of material, slower welding process.
TIG DC WELDING CONTINUOUS
TIG DC WELDING WITH MULTITACK
Continuous TIG welding provides continuous energy
which prevents the cooling of the piece and does not
cause overheating with excessive penetration and ex
-
cessive distortion effects.
Using the pulsed TIG reduces the effect of overheating
but it does not solve it completely as the arc will remain
on and will still provide energy and heat.
The series of triggers repeated over time allow the piece
to disperse the beat between a trigger and another. By
adjusting the MultiTack frequency the weld penetration,
speed’ of execution and in particular the control of the
heat input can be optimised as well as any consequent
deformation of the piece.
When welding corner joints, the Multitack may be used with excellent results. The welding remains white and free of
any oxidation often avoiding the post welding cleanup treatment with acids.
Tab. 15 - Recommended MULTITACK parameters
CORNER/BUTT JOINT
Sheet thickness (mm)
Current (A)
Multitack FREQUENCY (Hz)
0.6 mm
40A - 60A
1.0 - 1.5
0.8 mm
60A - 80A
1.0 - 1.5
1.0 mm
80A - 100A
1.0 - 1.5
1.5 mm
90A - 110A
1.0 - 1.5
2.0 mm
110A - 130A
1.0 - 1.5
130A - 150A
1.5 - 2.0
2.5 mm
150A - 160A
1.0 - 1.5
160A - 170A
1.5 - 2.0
3.0 mm
170A - 180A
1.0 - 1.5
180A - 200A
1.5 - 2.0
○ It is recommended that a preflow time of between 0.3 - 0.5 seconds be used in order to have
optimum protection right from the start, thus avoiding the oxidation of the initial part of the weld.
This is also the same for the final part where it is recommended that a post gas time of not less
than 3 seconds is used.
- ELECTRODE DIAMETER
○ The parameter optimizes the DC TIG welding arc strike on the basis of the diameter of the chosen
electrode.
Antwerpsesteenweg 949 9041 Gent - Oostakker
[email protected]
www.welda.be
T
+32 (0)9 355 74 26
F
+32 (0)9 355 92 01