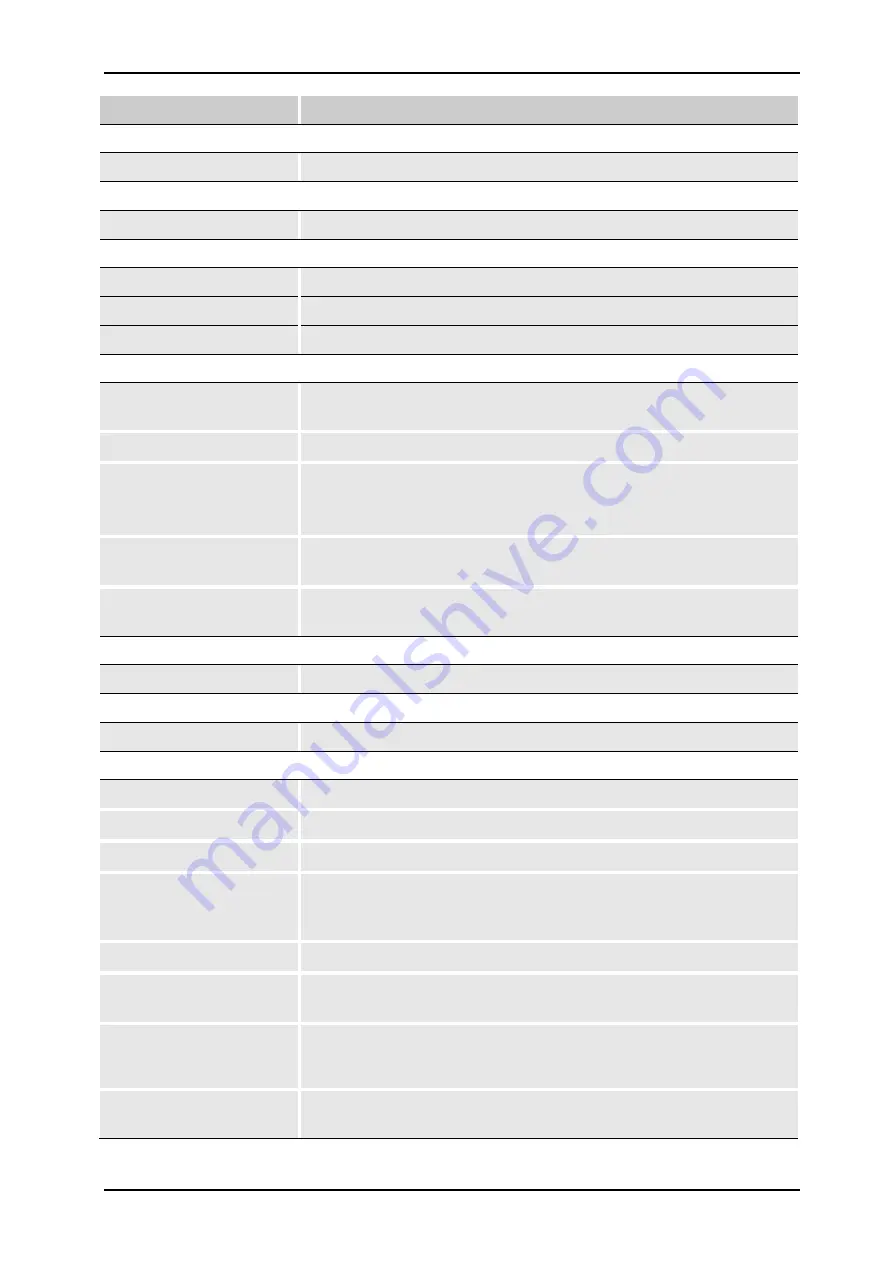
General
72800115 Markoprint X4JET
Seite 11 von 177
GB
Technical terms
Description
J
K
L
LED
Light emitting diode
LX
Lexmark
– Manufacturer for ink cartridges
LX Cartridge
Ink Cartridge from Lexmark
M
Maintenance station
Includes power supply, vacuum pump and catch tank for the MX
print head
Multiline MX
Print system with MX print heads 50 and 100mm
MX print head
Multiline
MX
head
Print head with Trident print head module Multiline MX family,
which can be connected to the X4JET
MX 50
Print head with Trident print head module Multiline MX family
with 50mm print height
MX 100
Print head with Trident print head module Multiline MX family
with 100mm print height
N
Nozzle plate
O
P
Piezo
A Piezo crystal changes its length with voltage
Piezo print head
A print head, which ejects ink by a piezo crystal.
ppi
Pulse per inch
Print direction
Print direction
indicates the direction of movement of the product
on the conveyor belt viewed from the controller in the print
direction
Print head
Exist of one or more print head modules, combined to one unit
Print head module
Consist of holding fixture for the ink cartridge, electronics and
connection socket and the connection to the controller
Print intensity
Contrast of the print image. If necessary this parameter must be
changed to optimize the print image.
A higher intensity gives greater
blackening and longer ink drying time.
Print speed
Print speed = Speed of the conveyor. The speed of the conveyor
must be keep constant
Summary of Contents for Markoprint X4JET
Page 2: ...Blank page ...
Page 82: ...Operation 72800115 Markoprint X4JET Seite 82 von 177 GB Menu structure ...
Page 120: ...Faults 72800115 Markoprint X4JET Seite 120 von 177 GB Fig 46 Extracting ink ...
Page 149: ...Appendix 72800115 Markoprint X4JET Seite 149 von 177 GB Electrical drawings for X4JET ...
Page 150: ...Appendix 72800115 Markoprint X4JET Seite 150 von 177 GB ...
Page 151: ...Appendix 72800115 Markoprint X4JET Seite 151 von 177 GB ...
Page 153: ...Appendix 72800115 Markoprint X4JET Seite 153 von 177 GB ...
Page 159: ...Appendix 72800115 Markoprint X4JET Seite 159 von 177 GB Print head HP MK2 Version 1 Single ...
Page 160: ...Appendix 72800115 Markoprint X4JET Seite 160 von 177 GB Print head HP MK2 Version 2 Single ...
Page 161: ...Appendix 72800115 Markoprint X4JET Seite 161 von 177 GB Print head HP MK2 Version 1 Twin ...
Page 162: ...Appendix 72800115 Markoprint X4JET Seite 162 von 177 GB Print head HP MK2 Version 2 Twin ...
Page 163: ...Appendix 72800115 Markoprint X4JET Seite 163 von 177 GB Print head LX MK2 Version 1 ...
Page 164: ...Appendix 72800115 Markoprint X4JET Seite 164 von 177 GB Print head LX MK2 Version 2 ...
Page 165: ...Appendix 72800115 Markoprint X4JET Seite 165 von 177 GB Druckkopf LX MK2 Version 1 Twin ...
Page 166: ...Appendix 72800115 Markoprint X4JET Seite 166 von 177 GB Druckkopf LX MK2 Version 2 Twin ...
Page 167: ...Appendix 72800115 Markoprint X4JET Seite 167 von 177 GB Print head MX 50 ...
Page 168: ...Appendix 72800115 Markoprint X4JET Seite 168 von 177 GB Print head MX 100 ...
Page 169: ...Appendix 72800115 Markoprint X4JET Seite 169 von 177 GB Mounting bracket Compact ...
Page 170: ...Appendix 72800115 Markoprint X4JET Seite 170 von 177 GB Mounting bracket Top ...
Page 177: ...Appendix 72800115 Markoprint X4JET Seite 177 von 177 GB ...