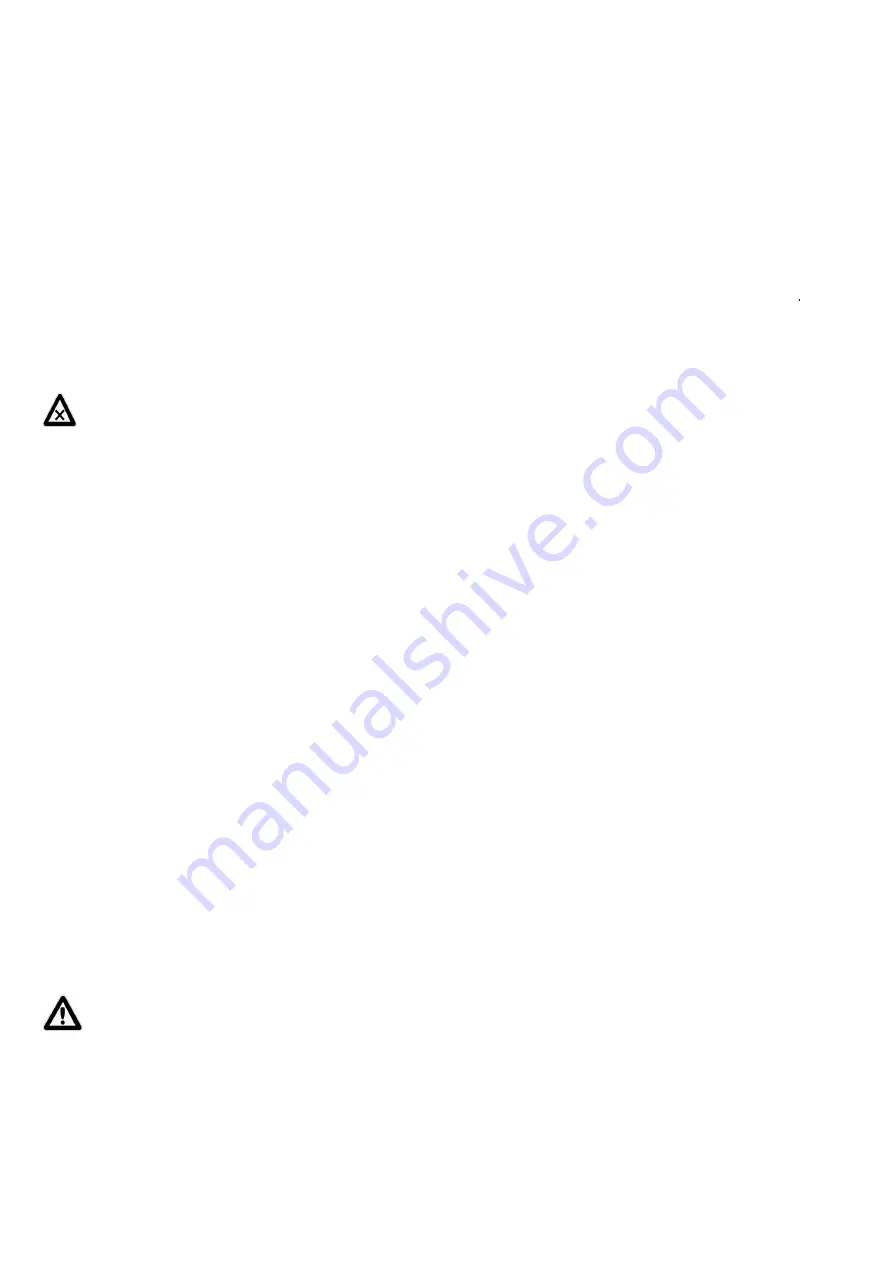
6
Prior to maintenance and repair work
Only use
original Weber spare parts
for maintenance or repair work to ensure reliable and safe
operation.
For repair, maintenance, or inspection work the engine of the roller must be safeguarded against
unintentional starting.
All pressurized lines, particularly hydraulic lines and lines of the injection system of the drive motor
must be depressurized before performing maintenance or repair tasks.
For maintenance and repair tasks the roller must be placed on a level and stable substrate and must
be secured from rolling off or tipping over.
Heavy components and assemblies must be secured to and lifted by hoisting machines that can
bear their weight when they are replaced. Ensure that no hazard is caused by raising components or
assemblies.
Do not position yourself or work under suspended loads.
Operation under difficult conditions
Never inhale the exhaust gas; it contains carbon monoxide, a colorless and odorless gas that is
extremely hazardous, which if inhaled even briefly can cause unconsciousness and death.
Therefore, never operate the engines in enclosed areas or in areas that are poorly ventilated
(tunnels, caves, etc.). Exercise particular caution when operating the engine in the vicinity of
people and livestock.
Hydraulic hose lines must be checked at regular intervals in accordance with standard engineering
practice, or they must be replaced at appropriate intervals, even if no signs of safety-relevant defects
are present.
Adjusting tasks, maintenance tasks, and inspection tasks must be carried out on schedule as
specified in this operating and maintenance manual. These activities should only be executed by
trained personnel.
Operation
Prior to starting work the owner of the roller must be familiar with the working environment. The
working environment includes obstacles in the work and traffic area, the bearing capacity of the
ground, as well as the necessary safeguarding of the construction site in the area adjacent to public
traffic; and it also includes compliance with traffic regulations.
The roller should only be operated when the protective fixtures are mounted. The protective fixtures
must all be in functional condition.
At least once per shift the roller must be checked for apparent defects. If there are apparent defects
then operation of the roller must be stopped immediately, and the responsible person must be
informed. Prior to restarting, roller malfunctions that have occurred must be corrected.
If lubricating oils and fuel come into contact with skin, they can cause skin cancer. Upon contact
with the skin, clean affected skin with suitable cleaning agent without delay.
Always maintain adequate clearance to the edges of pits and embankments.
Do not drive on slopes in the transverse direction in order to prevent the roller from tipping over.
After work has been concluded secure the roller in accordance with statutory regulations, particularly
in the area of public traffic surfaces.
Summary of Contents for 0140302
Page 1: ...1 Operating and Maintenance Manual DVH 655 E 2 0140302...
Page 2: ...2...
Page 30: ...30 Electrical circuit diagram...
Page 31: ...31...