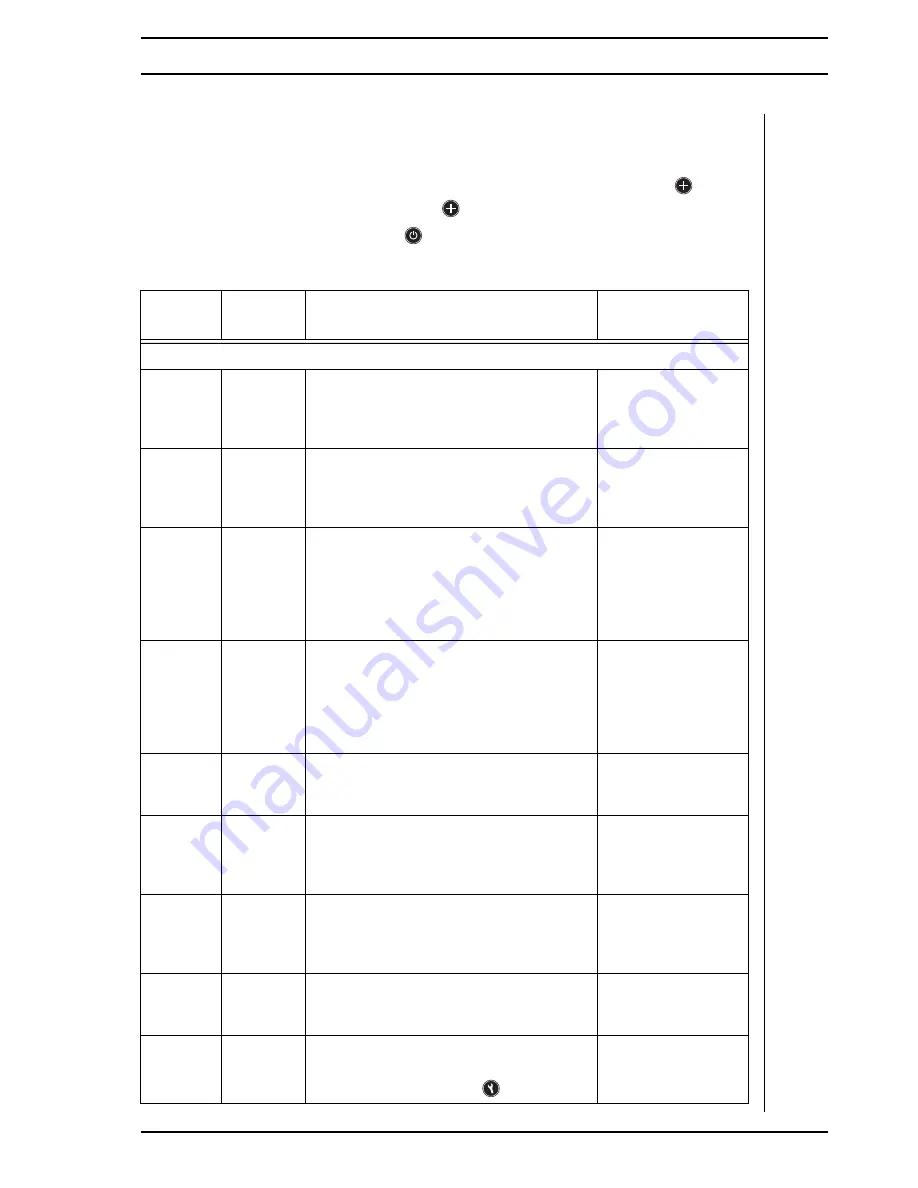
Webasto BlueCool Classic Series
PROGRAMMING
23
5.3
Re-initializing of Factory Default Settings
It is possible to force the program to reinitialize all program values to factory default settings by the
following procedure:
1. When reading the <b> line as above (through the 29 °C (84 °F) setpoint), push the
key until
the program version starts to flash. Keep the
key pushed down until the display shows <init>.
2. Leave programming mode by pushing
key - you are now back to the factory default settings.
Table 3
Description of Programming Codes - setpoint at 29 °C (84 °F)
Code #
Factory
Setting
Description
Optional Settings
Functions accessible by raising the setpoint to 29 °C (84 °F)
Code <0>
00 °C
(32 °F)
Lower setpoint temperature of the evaporator
coil when in cool cycle. This value gives the
compressor a cut-out point when the deicing
mode is activated (in cool cycle).
Adjustment range:
between
-4 and +15 °C
(25 and 59 °F)
Code <1>
05 °C
(41 °F)
Higher setpoint temperature of deicing
procedure. This value gives the restart point
of the compressor after a thermostatic
interruption when in deicing mode.
Adjustment range:
between
+2 and +18 °C
(36 and 64 °F).
Code <2>
45 °C
(113 °F)
Higher setpoint temperature of the “deicing”
procedure in relation to the evap. coil
temperature when in heat cycle (to avoid HP
cut-outs). Gives the cut-out point of the
compressor(s) when functioning in heat cycle.
Setpoint temperature
Adjustment range:
between
30 and 50° C
(86 and 122° F).
Code <3>
38 °C
(100 °F)
Lower setpoint temperature of coil
temperature cut in when in heat cycle. Gives
the cut in point of the compressor after an
interruption (“deicing” procedure) when
functioning in heat cycle. Setpoint
temperature
Adjustment range:
between
27 and 47 °C
(81 and 117 °F)
Code <4>
0.0
Calibration of the evaporator coil
temperature readout.
Adjustment range:
between
-9.9 and +9.9
Code <5>
15
Time delay in minutes before the digital
display goes into blank/sleep mode.
Cycle LED flashes discretely to indicate system
is operational.
05 - 99 min.
Code <6>
01
First start up delay in seconds after
connecting AC supply. To stage starting of
several Classic units when switching on AC
supply after an interruption.
01 - 20 sec.
Code <7>
0.0
Calibration of room temperature readout.
Adjustment range:
between
-9.9 and +9.9
Code <8>
00
Factory calibration of AC voltage 50 Hz as
displayed on the digital panel when accessing
the secondary commands -
key.
Adjustment range:
between -30 and +20
Volt.
Summary of Contents for BlueCool Classic Series
Page 38: ...THE RIGHT COOLING CAPACITY Webasto BlueCool Classic Series 38 ...
Page 39: ......