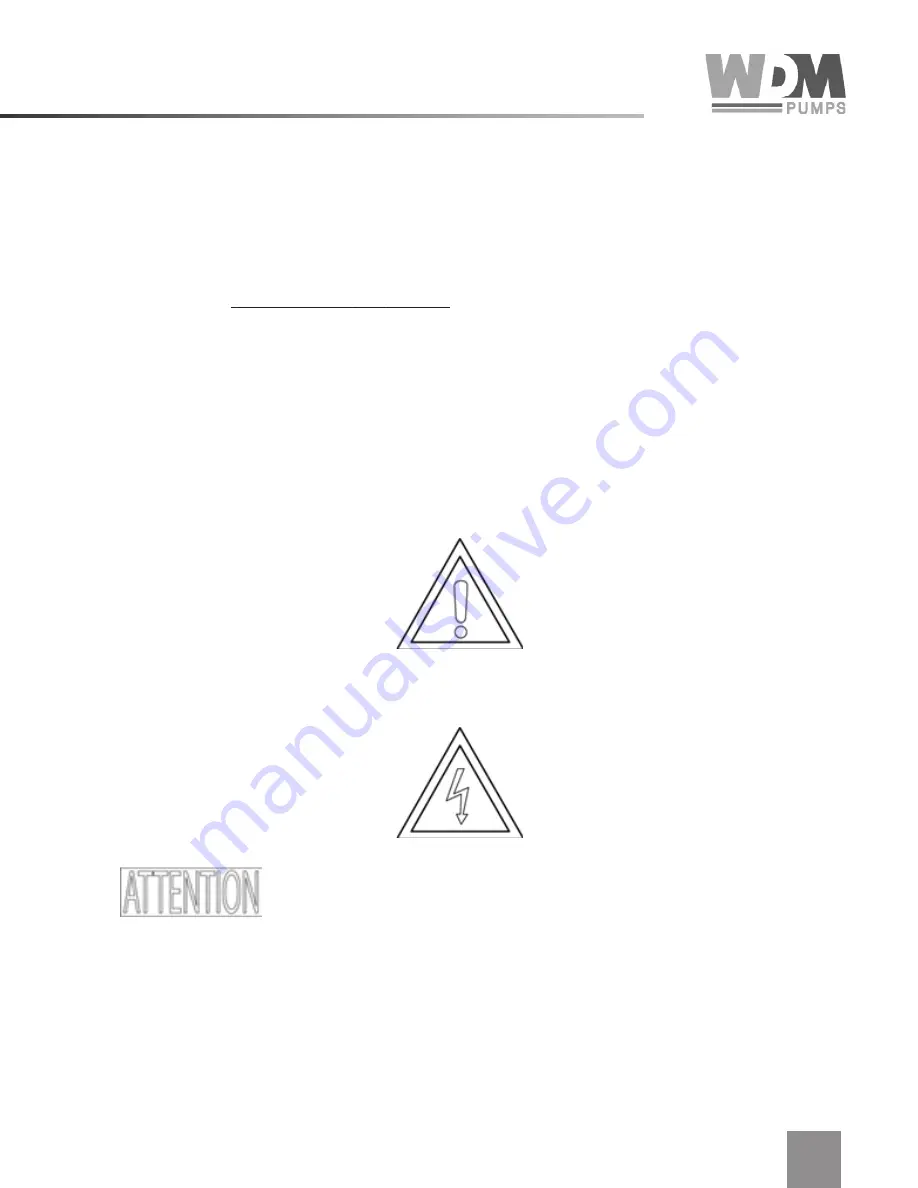
www.wdmpumps.com
7
PI Operation Manual
This operation manual gives basic instructions that should be observed during installation,
operation and maintenance of the pump. It is therefore imperative that this manual be read by the
responsible personnel/operator prior to assembly and commissioning.
It must always be kept available at the installation site. Not only are the general safety instructions
contained under this
SECTION TWO - SAFETY
that must be observed but also the specific
information provided in other sections.
Safety instructions given in this manual whose non-compliance would affect personal and
equipment safety are identified by the following symbol.
Where electrical safety is involved, the following symbol is shown.
The symbol is inserted in safety instructions whenever non-compliance
might endanger the machine or its function.
It is imperative that signs affixed to the machine are observed and kept legible, for example:
•
arrow indicating the direction of rotation
•
symbols indicating fluid connections
2. SECTION TWO - SAFETY
2.1 IDENTIFICATION OF SAFETY INSTRUCTIONS IN THE OPERATING MANUAL