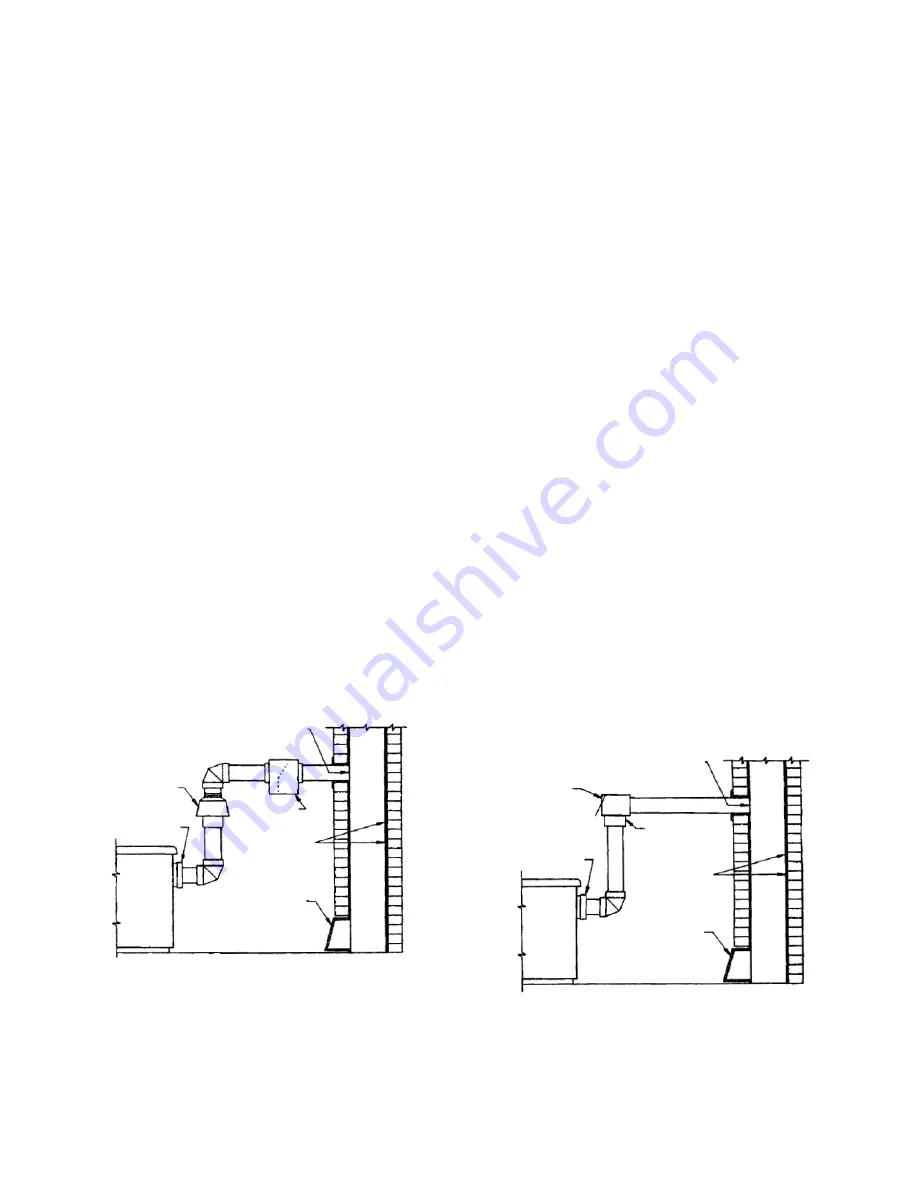
9
Where the chimney is unlined or where local experience indicates that flue gas condensate might be a
problem, the local gas company should be consulted.
The chimney should be examined and thoroughly cleaned, if necessary, before installation is made to make
sure it will freely conduct the flue gases to the outside.
Flue pipe should extend through the chimney wall to the inner face of the chimney liner but not beyond, and
should be firmly cemented to masonry. A thimble may be used to facilitate removal of flue pipe for cleaning, in
which event the thimble should be permanently cemented in place with mortar or other fireproof material that
will not crack or check the flue pipe or thimble, whichever is used, should be sealed into the chimney liner.
Flue connections from two or more appliances should not enter opposing or adjacent sides of the chimney at
the same level.
Under no circumstances should the flue pipe be connected to a flue of an open fireplace.
INSPECTION OF HEATING APPLIANCE
Clean the appliance heat exchanger interior, combustion chamber and flue connections. Remove all adhering
tars, scale, dirt, and soot. Inspect the heat exchanger for obvious and potential flue gas leaks. Cement all joints
around the appliance base and access openings to prevent air and/or flue gas leakage into or out of the
combustion chamber.
Warm Air Furnaces* - Make certain the electrical characteristics of the fan and limit switch correspond to those
required by this burner and that they are in proper working order.
Hot Water Boilers* - Make certain water temperature and altitude gauges, pressure relief valves are in proper
working order.
Steam Boilers* - Make certain the system is pressure tight and that the pressure gage and pop off safety valve are
in proper working order. Verify existing water sight glass permits clear observation of boiler water level.
*Where applicable, existing temperature of pressure limit switch or low water cut-off switch operation and
electrical characteristics shall be checked to determine their compatibility to the gas control circuitry of this burner.
NOTE:
For oil fired conversions consult boiler or furnace manufacturer. Appliance must maintain negative draft over
fire.
FLUE PIPE, DRAFT HOOD, AND BAROMETERIC DAMPER
Pitch Horizontal Run
1/4” (6.35mm) MIN.
per foot (0.305m)
Do Not Extend Flue
Pipe Beyond Inside
of Chimney
Cleanout
Reducer
Corrosion
Resistant Lining
Bull Head Tee
Single Acting
Barometric Draft
Control
Do Not Extend Flue
Pipe Beyond Inside
of Chimney
Pitch Horizontal Run
1/4” (6.35mm) MIN.
per foot (0.305m)
Vertical Draft Hood
Reducer
Horizontal
Draft Hood
Corrosion
Resistant Lining
Select either
Horizontal or
Vertical Draft Hood
Cleanout
Draft Hood Positions
Figure 3
Barometric Draft Control
Position
Figure 4
Summary of Contents for HSG200
Page 30: ...30 Figure 20 Flame Current Measurement Top Wayne control Bottom Honeywell control...
Page 48: ...48 Figure 29 continued Junction Box Assemblies Exploded Figure 30 Motor Assembly Exploded...
Page 49: ...49 Figure 31 Gun Assembly Exploded Figure 32 HSG Series Burner Exploded...
Page 52: ...52 NOTES...