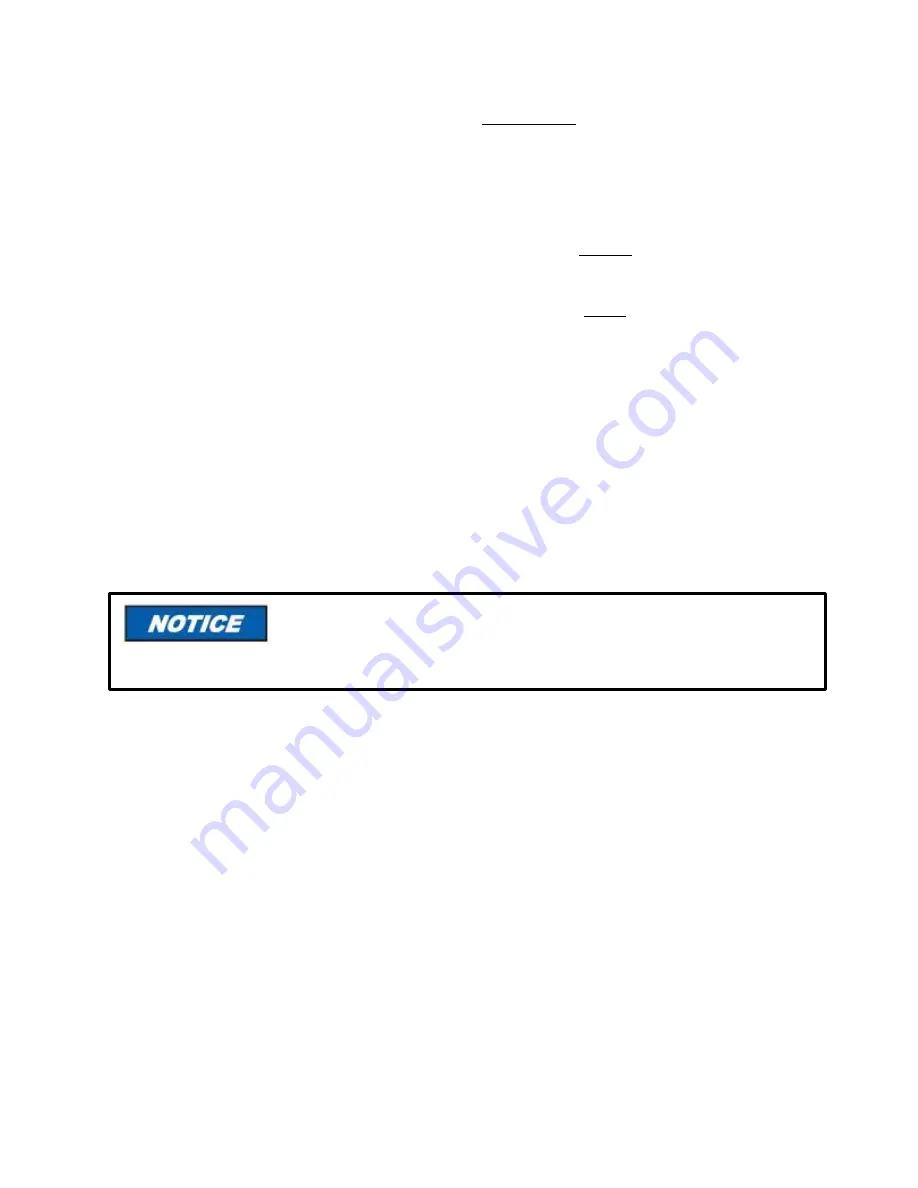
25
If an O
2
analyzer is used:
CO
AIRFREE
= x CO
PPM
If a CO
2
analyzer is used:
For Natural Gas:
CO
AIRFREE
= x CO
PPM
For LP Gas:
CO
AIRFREE
= x CO
PPM
Stack temperatures
for furnaces and boilers are recommended to be between 350 and 400 degrees
Fahrenheit.
NOTE:
Check overfire draft and adjust to NEGATIVE -0.01 (2.491 Pa) to -0.02 (4.982 Pa) inches w.c.
during burner operation.
If these values are not achieved with the initial settings listed in Figure 18, adjust the primary air
shutter to achieve these values. For the HSG400, if these values are not able to be achieved and the
burner is set to the low end of the firing range, adjust the off cycle damper to a lower setting to adjust
burner. For the HSG200, if these values are not able to be achieved, the off cycle damper setting may
need to be increased to adjust the burner.
3. After the air is adjusted, combustion meets the recommendations in step 2 and the burner is running
properly, be sure to record all set up information and leave it with the burner. With the burner shut off
and the manual control knob in the “OFF” position, remove the hose barb and replace the 1/8” NPT
pressure tap plug. Apply a small amount of thread sealant to the plug before replacing.
SECTION III: GAS CONVERSION
The HSG200 and HSG400 can operate on either natural gas or LP gas. To convert an HSG burner from
one gas to another requires changing the orifice, setting of the manifold pressure, and adjusting the air
shutter(s). The HSG200 and HSG400 conversion burners are shipped from the factory with a natural gas
orifice installed and a label on the burner which indicates the burner has a natural gas orifice installed. In
order to convert the burner to fire LP gas, refer to the chart in Figure 11 for selection of the proper orifice
for the desired firing rate. An orifice kit is provided with each burner. The kit also includes a gas
identification label that is designed to be placed over the gas identification label located on the burner.
Place the label for the new gas, natural or LP over the existing label when converting from one gas to
another. Follow the procedure outlined in CHANGING THE ORIFICE and SECTION II: INITIAL START
UP for making the necessary adjustments to the manifold pressure. Follow the procedure in
COMBUSTION ADJUSTMENT OF BURNER for any initial installation, after a change in rate, or a
conversion from one gas to another.
20.9
(20.9
– %O
2
)
11.7
% CO
2
13.8
% CO
2
IF THE BURNER Btu/hr (kW) INPUT IS CHANGED REPEAT COMBUSTION
ADJUSTMENT OF BURNER.
Summary of Contents for HSG200
Page 30: ...30 Figure 20 Flame Current Measurement Top Wayne control Bottom Honeywell control...
Page 48: ...48 Figure 29 continued Junction Box Assemblies Exploded Figure 30 Motor Assembly Exploded...
Page 49: ...49 Figure 31 Gun Assembly Exploded Figure 32 HSG Series Burner Exploded...
Page 52: ...52 NOTES...