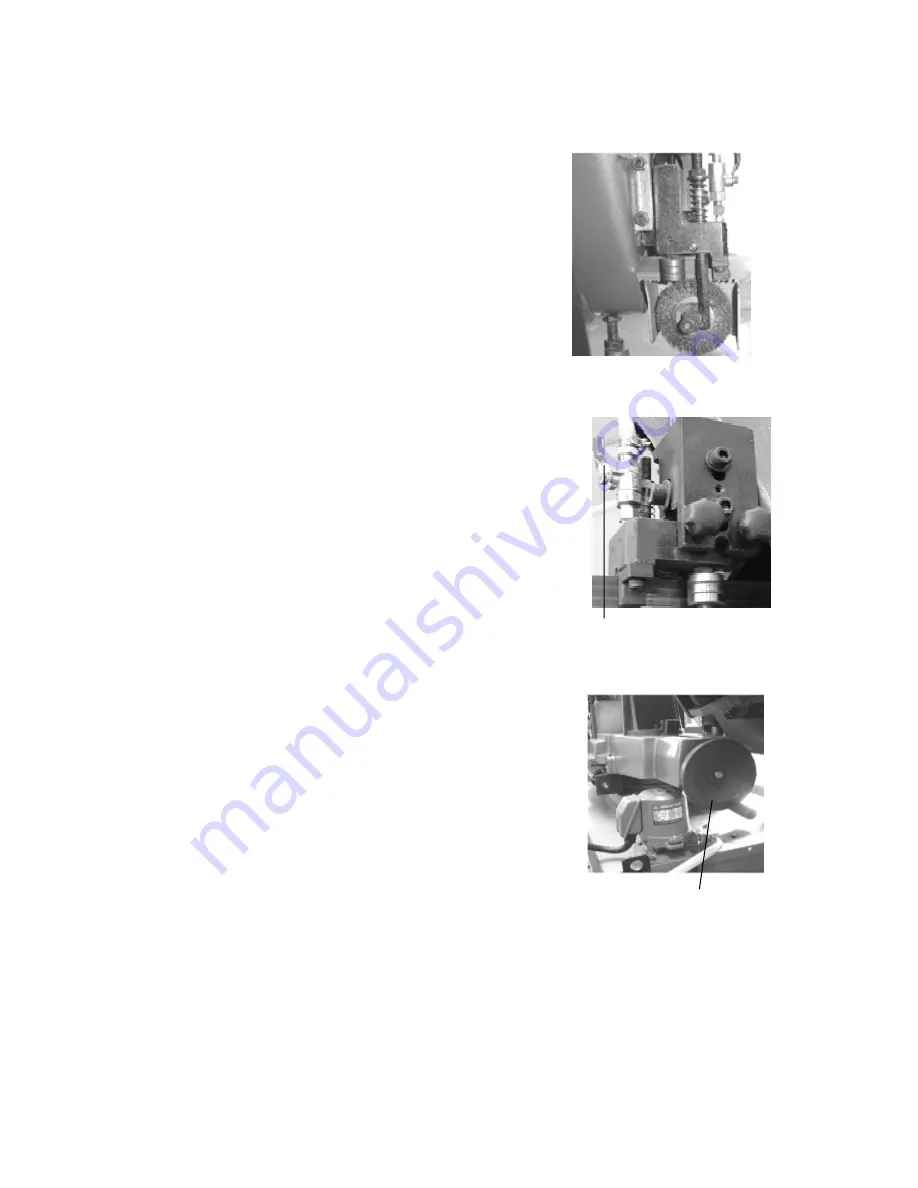
9-8.CLEARING THE CUTTTNG CHIP
Please use steel brush to clear the chip on the blade teeth (fig 11)
Fig.11
9-9.BLADE AND COOLING SYSTEM
The use of proper cutting fluid is essential to obtain
maximum efficiency from a band saw blade. The main cause
of tooth failure is excessive heat build-up. This is the reason
that cutting fluid is necessary for long blade life and high
cutting rates. cutting area and blade wheels should be kept
clean at all time.
A Fig.12
A
The rate of coolant flow is controlled by the stop valve lever
(A) (fig 12), which directs the coolant onto the blade.
The lever (A) is shown in the off position.
9-10.OPERATING AND ADJUSTING VISE
The work-piece is placed between the vise jaws with the
amount to be cut-off extending out past the blade. Your
machine is equipped with a "quick action" Vise jaw which
allows you to instantly position the moveable vise jaw B
(fig, 14).
Fig.13
Simply turn hand-wheel A
counterclockwise 1/2 turn and move the vise
jaw s to the desired
position. Then tighten the vise jaw B against the
work-piece by turning hand-wheel clockwise.
15
Summary of Contents for 250S
Page 1: ...METAL CUTTING BAND SAW MACHINE MODEL 250S INSTRUCTION MANUAL 250S 060505 R2...
Page 24: ...12 CIRCUIT DIAGRAM 22...
Page 25: ...OP 23...
Page 26: ...24...
Page 27: ...25...
Page 28: ...26...
Page 29: ...27...
Page 30: ...28...
Page 31: ...29...
Page 32: ...30...