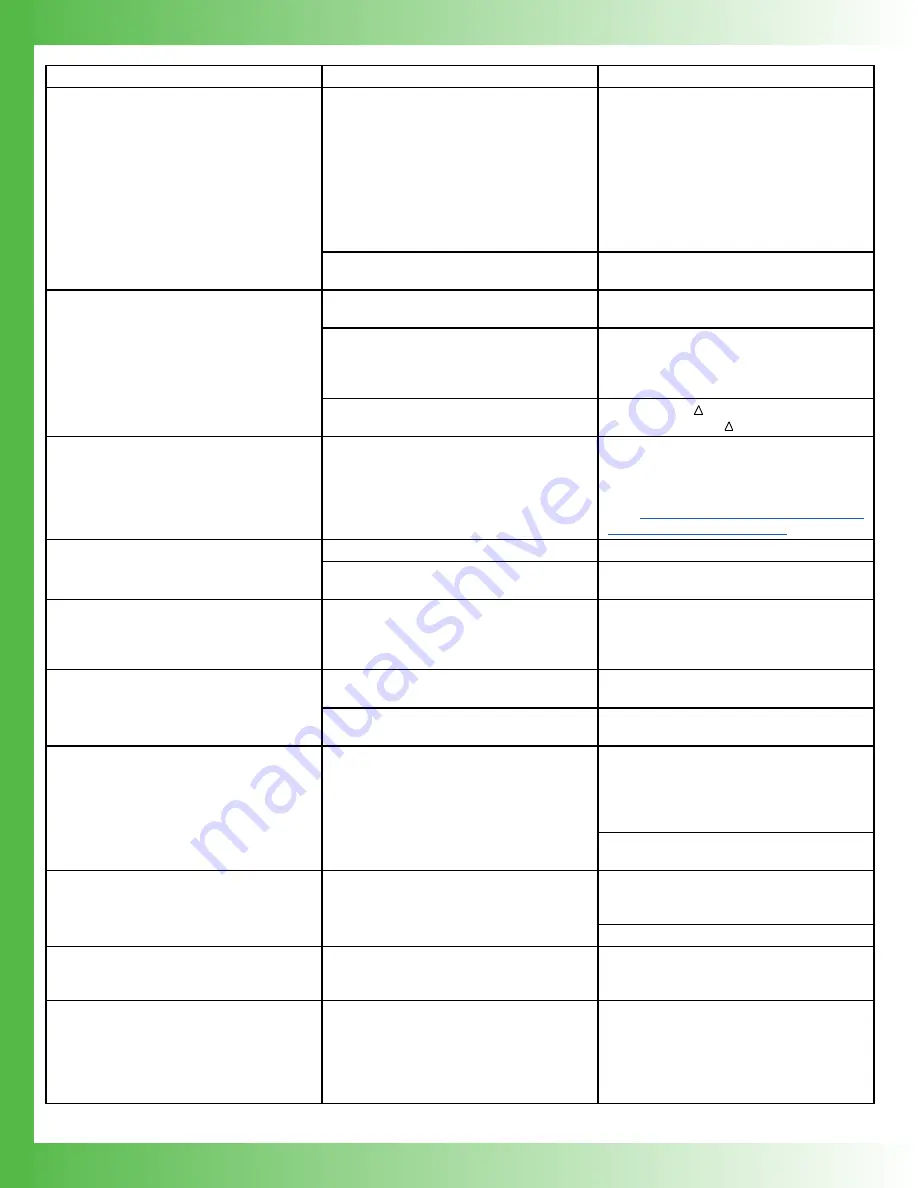
24
PROBLEM
POTENTIAL CAUSES
SOLUTIONS
Using a resistive heater, temperature
is slow to stabilize and is not within the
specifications.
Setpoint temperature is set too close to the
ambient temperature.
Set the temperature at least 10°C above ambient
when using a resistive heater. A resistive heater
is unable to precisely maintain temperatures
near ambient because once the temperature
overshoots the setpoint, the controller turns off
and relies on ambient temperature to cool the
load. If setting the temperature 10°C or more
above ambient is not possible, then choose
a thermoelectric, which can alternately heat
and cool the load to maintain a more precise
setpoint temperature.
Airflow across load is inadequate.
Use a fan to blow air across the load to
increase natural convection.
Temperature does not reach the setpoint.
Insufficient current driven to the TEC or
heater.
Increase the current limit, but DO NOT
exceed the specifications of the TEC/RH.
The controller does not have sufficient
compliance voltage to drive the TEC or
heater
Check the thermoelectric voltage and
determine if it is too close to the 15 V
maximum. If it is, choose a lower voltage
thermoelectric.
Temperature differential may be too great.
Check TEC T
MAX
. What is heatsink
temperature minus T?
Temperature increases beyond the
setpoint and will not come down.
The TEC and heatsink are not adequately
sized for the thermal load.
The system is in "thermal runaway."
The heat being generated by the load
may be too great for the TEC to pump to
the heatsink; a larger TEC or heatsink, or
airflow may be needed. Consult Technical
TN-TC01: Optimizing Thermoelectric
.
Actual temperature does not approach
setpoint after output current is enabled.
Thermoelectric wiring is reversed.
Reverse the leads to the thermoelectric.
The thermoelectric is generating too much
heat and has inadequate cooling.
Install a larger heatsink or a fan to cool the
heatsink.
I hear a beep and know there is an error,
but nothing is displayed on the instrument
screen.
A remote command
REMERR 1
needs to
be sent to the instrument to display errors.
Connect the LDTC LAB to a remote
computer and write the
REMERR 1
command. See the Remote Command set
document for more information.
My instrument doesn't show up in the list.
(REMOTE ONLY)
Instrument may not be turned on.
Power up the instrument and click
Refresh
on the
Choose Instrument
window.
Your instrument may not be plugged into
the computer.
Check that a USB cable is tightly connected
to the instrument and to the computer.
IntelliTune fails because of a sensor error.
Sensor voltage may be too high or too low,
which triggers a bias current change.
Choose a setpoint such that the sensor
voltage will be between 0.14 V and 10 V.
The sensor signal will be in range during
all of the sweeps and not trigger a bias
current change.
Use the remote command
TEC:BIAS
to
set a fixed sensor bias current.
IntelliTune fails because of a "load short"
error.
The load compliance voltage is too low
Put a resistor in series with the
thermoelectric to increase the load
compliance voltage.
Decrease Cable Resistance.
Can't clear an on-screen error message.
The cause of the error may not have been
fixed.
Clear the error on screen. If the cause
of the error is not corrected, the error
message is displayed again.
IntelliTune gives me different answers
when I run a scan.
System has not reached thermal
equilibrium.
The characteristics of the load will change
from initial start with all parts at room
temperature to when parts are at desired
operating temperatures. Run IntelliTune
once all elements of the system have
reached operating temperature.