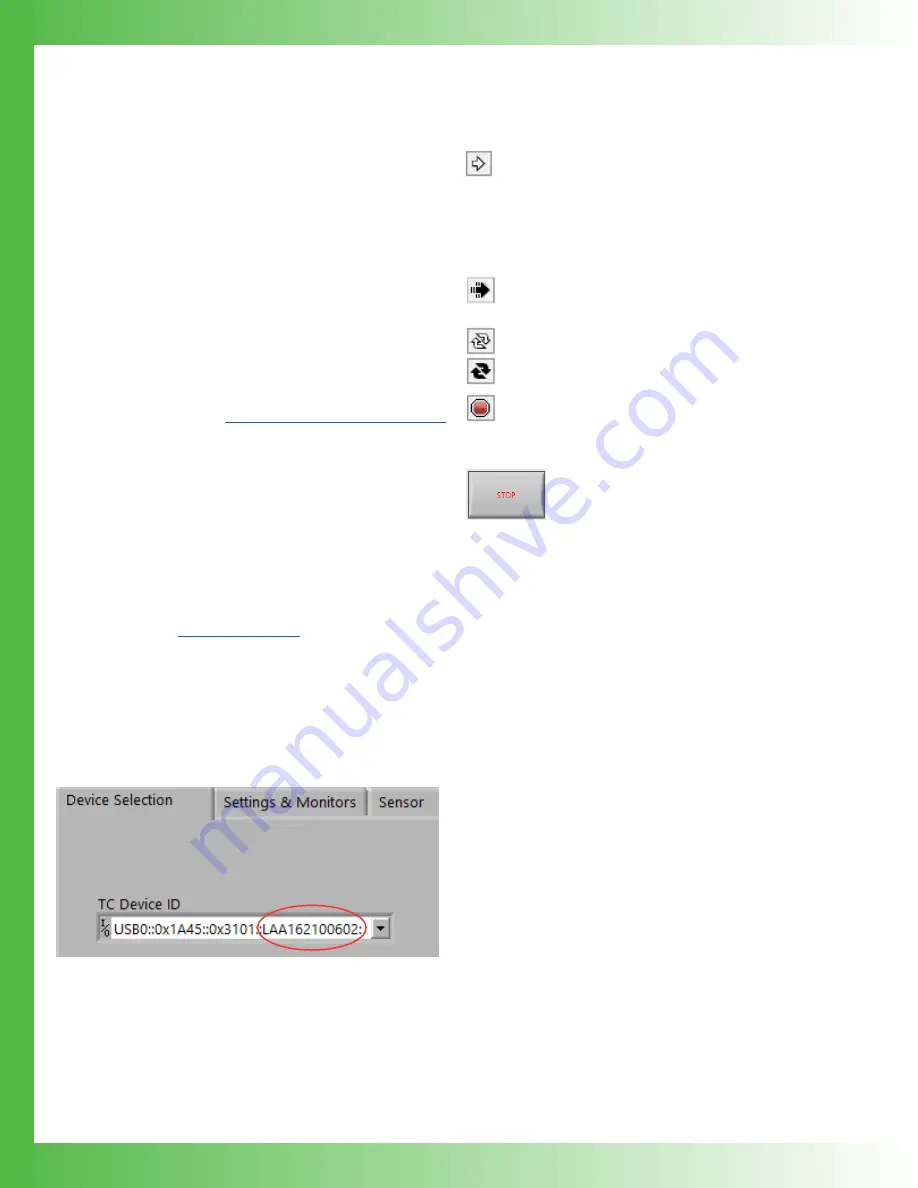
6
4. On the Virtual Instrument toolbar, click the
Run
icon to communicate with the instrument once you
have entered the operating values on the
Settings &
Monitors
tab and want to apply the settings. If this icon
is visible, the VI is not running, and any changes made
on screen will not be implemented.
ADDITIONAL CONTROLS
Running
: Indicates that the instrument and application
are communicating and commands to implement
settings are continuously sent.
Run Continuously
: This control is not used.
Running Continuously
: This control is not used.
Abort Execution
: This stops the application immediately,
interrupting any commands that are currently in process.
It is NOT recommended to use this method of stopping
the application. Instead, use the STOP button.
Stop
: Use the Stop button to gracefully end
remote control of the instrument. Any commands
in process are completed prior to ending remote
control. The TC LAB instrument will continue to
run in LOCAL MODE.
INSTALL THE NATIONAL INSTRUMENTS
RUNTIME ENGINE 2015
Prior to installing Wavelength's Virtual Instrument application,
the National Instrument (NI) Runtime Engine 2015 must be
installed on the remote computer.
When installing the Virtual Instrument .EXE file, if the Runtime
Engine is not already installed on the computer, a message
with a link to the NI website download page opens. Follow
the download instructions on the page. The Runtime Engine
can take several minutes to install and requires restarting the
computer.
INSTALL TC LAB VIRTUAL INSTRUMENT
APPLICATION
1. On the Wavelength
click the LabVIEW Interface for the TC LAB Series and
download it to the computer.
2.
Save the file to the computer, and open it.
3. Follow the prompts to install the application.
CONNECT THE TC LAB TO THE REMOTE
COMPUTER
1. Connect a USB or Ethernet cable from the instrument to
the remote computer and turn on the rear panel power
switch. See the
for other connections.
NOTE: If using an Ethernet connection, configure the
network settings with NI-MAX or similar.
2. On the computer, open the Virtual Instrument application.
3. On the
Device Selection
tab, in the
TC Device ID
field, choose the instrument to communicate with. The
instrument is identified by the Serial Number, as shown
in
.
Instrument Serial Number
Figure 6. Device Selection Tab
OPERATING INSTRUCTIONS - TC LAB