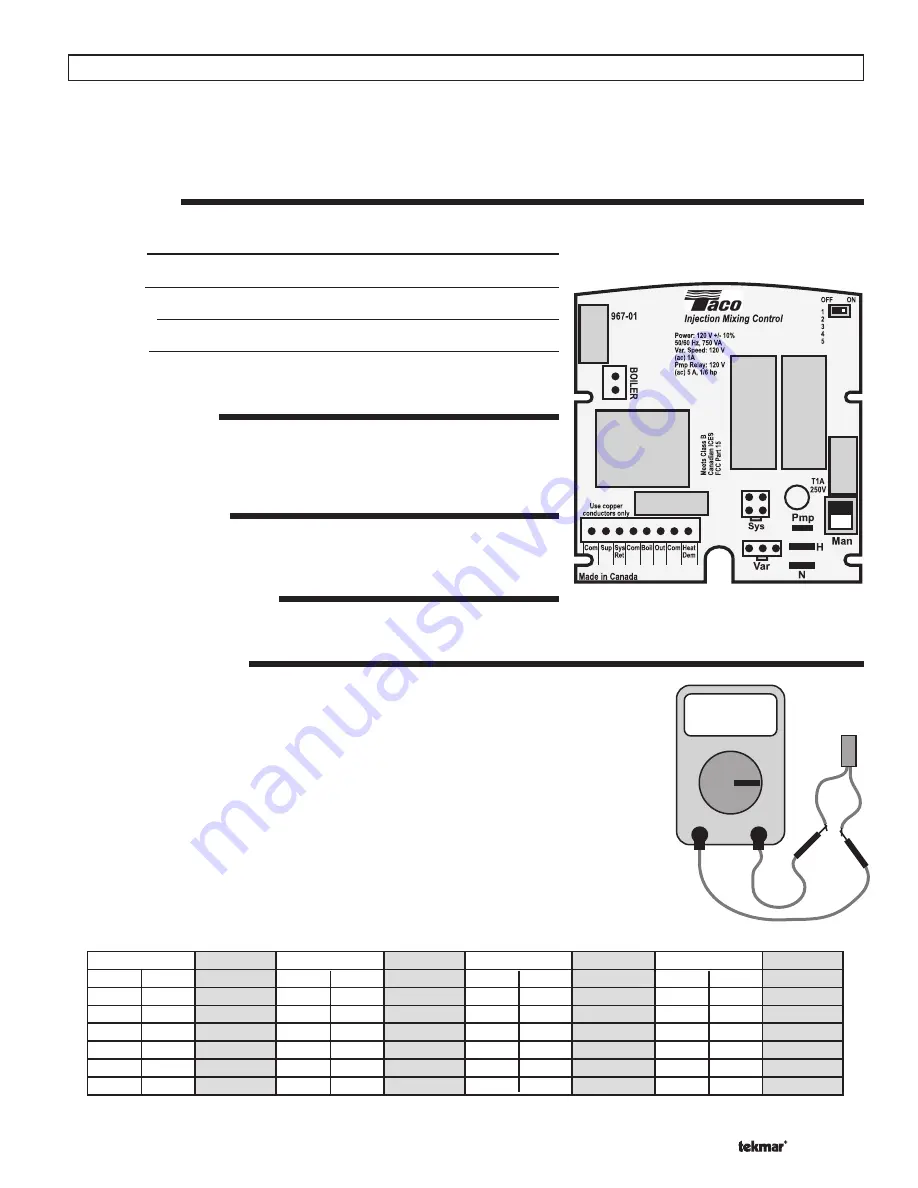
13 of 16
© 2005 D 704 - 04/05
As in any troubleshooting procedure, it is important to isolate the problem as much as possible. By using the Error Messages located on
page 14, the troubleshooting process can be greatly simplifi ed. When an error message is displayed on the RMC, refer to the error mes-
sages on page 14 to identify the cause of the error and use standard testing procedures to confi rm the fault. If you suspect an external
wiring fault, return to step three and carefully check all external wiring connections.
Once the fault has been corrected, press any button on the face of the control to clear the error message.
TEST ROUTINE
The main control functions of the RMC can be tested by pressing and holding the UP button for more than three (3) second. After the
UP button has been pressed for more than three (3) second, the RMC enters the following sequence.
Step One
The variable speed output is increased from 0% to 100% over 10 seconds.
Step Two
The variable speed output is decreased from 100% to 0% over 10 seconds.
Step Three
The System Pump is turned on for 10 seconds.
Step Four
The Boiler Contact is turned on. After 10 seconds, the Boiler Contact and the
System Pump contact are turned off. The RMC continues normal operation.
MANUAL OVERRIDE
In the event that the RMC fails to operate, a manual operation switch is located
on the RMC’s circuit board. When the manual operation switch is set to Man, the
variable speed injection pump and the system pump outputs are turned on. This
operation continues until the manual switch is returned to its original position.
FUSE REPLACEMENT
The Variable Speed output of the RMC is fused protected. This fuse is located on
the circuit board on the back of the RMC. This is a fi eld replaceable item.
Fuse rating: 1 A 1/12 hp, fuse T1 A 250 V
ADJUSTMENT OF SETTINGS
If the outdoor temperature is cold and the rooms are cold, increase the MIX DSGN
setting by 5°F (3°C) per day.
TESTING THE SENSORS
Do not apply voltage to the sensor or to the sensor input of the control as this will result in damage
to either the sensor, the control, or both the sensor and the control.
A quality testing meter capable of measuring up to 2,000,000 ohms and a good quality digital ther-
mometer are required to test the sensors. If a digital thermometer is not available, place a second
sensor next to the original sensor and compare the readings.
Begin by measuring the temperature at the sensor location using the digital thermometer. Next,
measure the resistance of the sensor using the testing meter. Ensure that the sensor is disconnect
from the control at the time of testing. Using the reference chart below, determine the sensor’s
temperature. Compare the sensor’s temperature to that measured by the digital thermometer. The
two temperature readings should be close.
If the sensors temperature is too high, this can indicate that there is a partial short in the sensor
wiring. If the sensor’s temperature is too low, this can indicate that there is a loose connection or
break in the sensor wiring. Isolate and repair the problem. If the problem is isolated to the sensor,
replace the sensor.
Troubleshooting
OHM
-30
-20
-10
0
10
20
30
40
50
60
70
80
90
100
110
120
130
140
150
160
170
180
190
200
-34
-29
-23
-18
-12
-7
-1
4
10
16
21
27
32
38
43
49
54
60
66
71
77
82
88
93
234,000
165,000
118,000
85,500
62,500
46,000
34,500
26,000
20,000
15,500
12,000
9,300
7,300
5,800
4,700
3,800
3,100
2,500
2,000
1,700
1,400
1,200
1,000
800
Temperature
Resistance
F
C
Ohms
Temperature
Resistance
F
C
Ohms
Temperature
Resistance
F
C
Ohms
Temperature
Resistance
F
C
Ohms