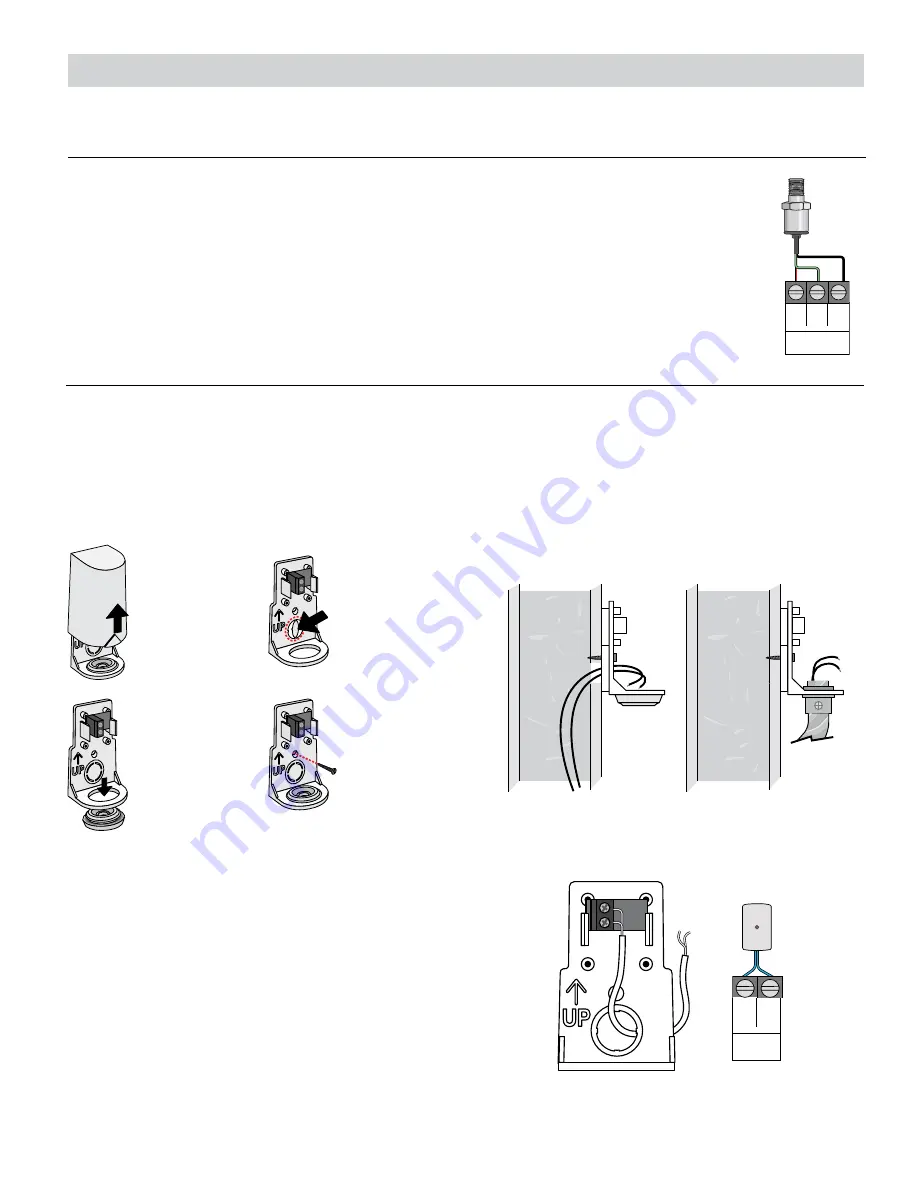
IOM-T-294
2205
© 2022 tekmar
7
Ref
Pressure
Sensor
In
2
3
Gnd
1
Pressure Sensor 088 (Terminals 1, 2, 3)
An optional Pressure Sensor 088 (sold separately) can connect to the 294 to provide pressure
monitoring for hydronic systems up to 150 psi (1034 kPa) . The pressure sensor requires the installation
of a tee with a
1
⁄
8
"-27 NPT port to be installed near the expansion tank .
• Connect the Red reference voltage wire to terminal 1 .
• Connect the Green pressure signal wire to terminal 2 .
• Connect the Black power common wire to terminal 3 .
Remove
cover by
sliding
upwards
away from
the base.
To wire from
the back,
remove the
knock-out in
the sensor
base.
S1
S1
If using
conduit,
remove the
flexible plug
from the base
bottom.
S1
S1
Attach the
base to
the wall,
soffit or
electrical
box.
S1
S1
• The 070 can be mounted directly onto a wall with the
wiring entering through the back or bottom of the enclosure .
Do not mount the 070 with the conduit knockout facing
upwards as rain could enter the enclosure and damage
the sensor .
• In order to prevent heat transmitted through the wall from
affecting the sensor reading, it may be necessary to install an
insulating barrier behind the enclosure .
• The 070 should be mounted on a wall which best represents
the heat load on the building (a northern wall for most buildings
and a southern facing wall for buildings with large south
facing glass areas) . The 070 should not be exposed to heat
sources such as ventilation or window openings .
• The 070 should be installed at an elevation above the ground
that will prevent accidental damage or tampering .
Outdoor Sensor 070 (Terminals 4, 5)
This section explains how to wire individual devices to the Smart Boiler Control 294 .
Wiring Instructions
• Connect 18 AWG or similar wire to the two terminals provided
in the enclosure and run the wires from the sensor to the
control . Do not run the wires parallel to telephone or power
cables . If the sensor wires are located in an area with strong
sources of electromagnetic interference (EMI), shielded cable
or twisted pair should be used or the wires can be run in a
grounded metal conduit . If using shielded cable, the shield
wire should be connected to the Com terminal on the control
and not to earth ground .
• Replace the cover of the sensor enclosure .
• Connect the 2 wires from the outdoor sensor to the Out
Sens terminals on the 294 (terminals 4 and 5) .
S1
S1
+
Outdoor
Sensor
-
5
4