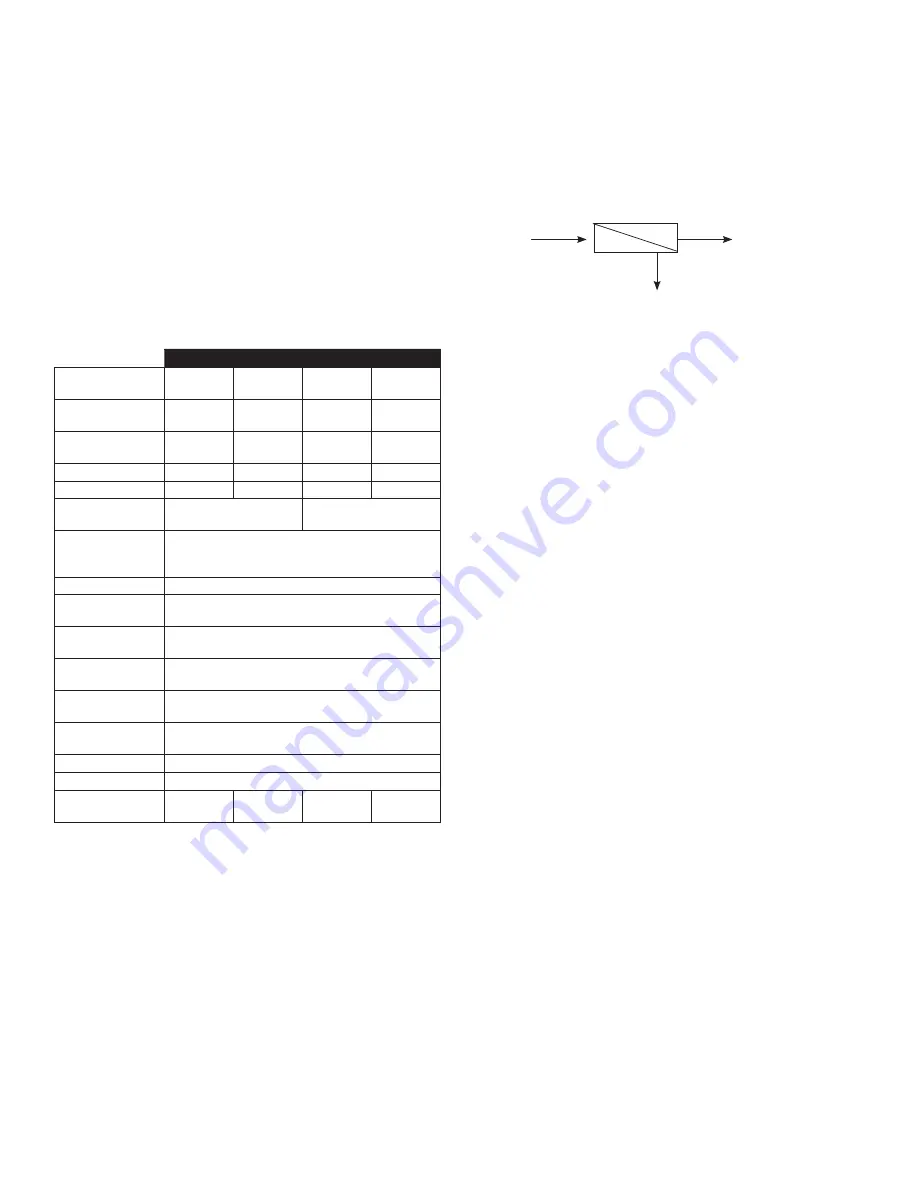
C. Pretreatment
The RO feed water must be pretreated in order to prevent mem-
brane damage and/or fouling. Proper pretreatment is essential for
reliable operation of any RO system.
Pretreatment requirements vary depending on the nature of the feed
water. Pretreatment equipment is sold separately. The most common
forms of pretreatment are described below.
Media Filter -
Used to remove large suspended solids (sediment)
from the feed water. Backwashing the media removes the trapped
particles. Backwash can be initiated by time or differential pressure.
Water Softener -
Used to remove calcium and magnesium from
the feed water in order to prevent hardness scaling. The potential
for hardness scaling is predicted by the Langelier Saturation Index
(LSI). The LSI should be zero or negative throughout the unit unless
approved antiscalents are used. Softening is the preferred method of
controlling hardness scale.
Carbon Filter -
Used to remove chlorine and organics from the
feed water. Free chlorine will cause rapid irreversible damage to the
membranes.
The residual free chlorine present in most municipal water supplies
will damage the thin film composite structure of the membranes
used in this unit. Carbon filtration or sodium bisulfite injection should
be used to completely remove the free chlorine residual.
Chemical Injection -
Typically used to feed antiscalant, coagulant,
or bisulfite into the feed water or to adjust the feed water pH.
Prefilter Cartridge -
Used to remove smaller suspended solids and
trap any particles that may be generated by the other pretreatment.
The cartridge(s) should be replaced when the pressure drop across
the housing increases 5 - 10 psig over the clean cartridge pressure
drop. The effect of suspended solids is measured by the silt density
index (SDI) test. An SDI of five (5) or less is specified by most mem-
brane manufacturers and three (3) or less is recommended.
Iron & Manganese -
Iron should be removed to less than 0.1 ppm.
Manganese should be removed to less than 0.05 ppm. Special me-
dia filters and/or chemical treatment is commonly used.
pH
- The pH is often lowered to reduce the scaling potential. If the
feed water has zero hardness, the pH can be raised to eliminate
CO2.
Silica:
Reported on the analysis as SiO2. Silica forms a coating on
membrane surfaces when the concentration exceeds its solubility.
Additionally, the solubility is highly pH and temperature dependent.
Silica fouling can be prevented with chemical injection and/or reduc-
tion in recovery.
2
I. Introduction
The separation of dissolved solids and water using RO membranes
is a pressure driven temperature dependent process. The membrane
material is designed to be as permeable to water as possible, while
maintaining the ability to reject dissolved solids.
The main system design parameters require the following:
• Internal flows across the membrane surface must be high enough
to prevent settling of fine suspended solids on the membrane
surface.
• The concentration of each dissolved ionic species must not exceed
the limits of solubility anywhere in the system.
• Pre-treatment must be sufficient to eliminate chemicals that would
attack the membrane materials.
PWR25111011 PWR25112011 PWR25113011 PWR25113021
Maximum Productivity
(gallons per day)
150
250
600
1200
Quality
(membrane rejection)
98 %
98 %
98 %
98 %
Recovery
(user adjustable)
15 - 75 %
15 - 75%
15 - 75 %
30 - 75 %
Membrane Size
2.5" x 14"
2.5" x 21"
2.5" x 40"
2.5" x 40"
Number Of Membranes
1
1
1
2
Dimensions W x H x D
(approximate inches)
22 x 32 x 12
22 x 52 x 12
Prefilter
(system ships with one
5 micron cartridge)
10"
Feed Water Connection
1
⁄
2
" NPT
Product Water
Connection (tubing OD)
3
⁄
8
"
Reject Water
Connection (tubing OD)
3
⁄
8
"
Feed Water Required
(maximum)
2.4 gpm
Feed Water Pressure
(minimum)
20psi
Drain Required
(maximum)
2.4 gpm
Electrical Requirement
120 VAC 60 Hz 8 amps
Motor Horse Power
1
⁄
2
Shipping Weight
(estimated pounds)
50
50
60
70
Notes:
• Maximum production based on a feed water of 77°F, SDI < 3, 1000 ppm TDS,
and pH 8.
Individual membrane productivity may vary (± 15%). May be operated on other
feed waters with reduced capacity.
• Percent Rejection is based on membrane manufactures specifications; overall
system percent rejection may be less.
A. Specifications
RO Membrane
Feed Water
Product Water
Reject Water
B. RO Overview
Reverse osmosis systems utilize semipermeable membrane ele-
ments to separate the feed water into two streams. The pressurized
feed water is separated into purified (product) water and concentrate
(reject) water. The impurities contained in the feed water are carried
to drain by the reject water. It is critical to maintain adequate reject
flow in order to prevent membrane scaling and/or fouling.