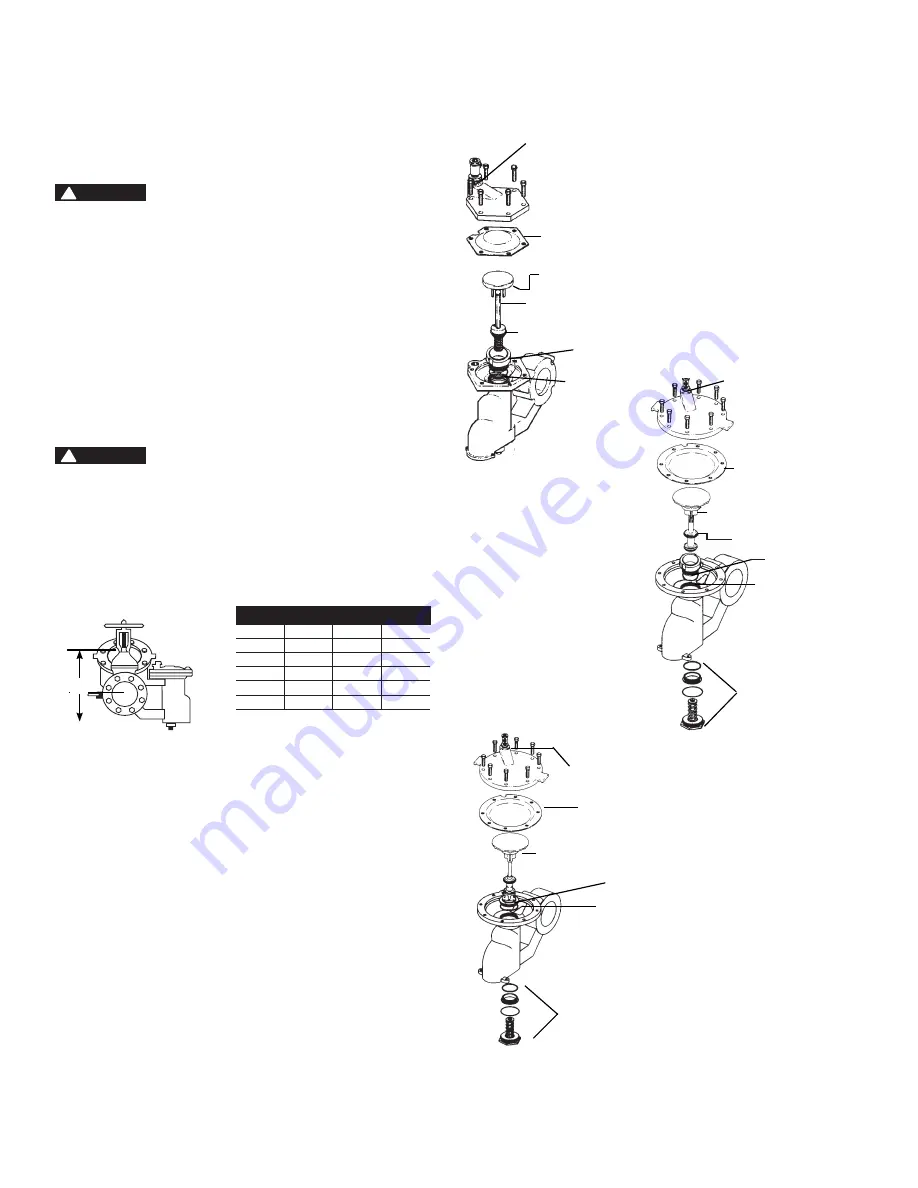
6
Servicing the Relief Valve
Sizes: 2
1
⁄
2
" – 10" (65-250mm)
1. Remove the relief valve cover bolts. Note the 909/LF909 is
designed so that when the bolts are backed off
1
⁄
2
" all the relief
valve spring load is retained by the bottom plug spring module.
CAUTION
!
Be sure to verify this before removing all the bolts.
2. Remove the cover and diaphragm. The relief valve piston
assembly can be lifted straight up and out.
3. Replace the wiper seal and piston O-ring and apply grease to
the O-ring.
4. To replace the relief valve disc, hold the upper guide fin and
unscrew the diaphragm pressure plate. It may be necessary to
lightly tap the cast webs and the pressure plate to loosen.
Replace with a new disc holder assembly and O-ring. Note: the
disc rubber is molded into the disc holder and is supplied as a
disc holder assembly.
5. Removal of the bottom plug and spring assembly. During nor-
mal field service there is no need to remove the bottom plug
spring assembly other than inspection. It can be removed by
simply unscrewing with a large pipe wrench.
CAUTION
!
The spring as retained on the bottom plug is highly loaded. NO
attempt should be made in the field to remove the spring. For
replacement, a complete bottom plug assembly must be obtained
from the factory.
For further details contact your technical sales representative, see
back page.
clEaRancE REQuiREd FOR sERVicinG
in.
mm
A
B
2
1
⁄
2
– 3
65-80
10"
11"
4
100
15"
14"
6
150
15"
16"
8
200
23"
21"
10
250
25"
21"
Relief Module
B
Adapter O-ring
Diaphragm
Relief Valve Disc
Relief Valve Piston
Assembly
Piston O-Ring
Seat
O-ring
Sizes
2
1
⁄
2
" – 3"
(65 – 80mm)
Diaphragm
Sizes 8", 10"
(200, 250mm)
Relief Valve Assembly
Seat
O-ring
Plug & Spring
Assembly
Adapter o-ring
Diaphragm
Sizes 4", 6"
(100, 150mm)
8"M1, 10"M1
Relief Valve Piston
Assembly
Piston seal
Seat
O-ring
Plug &
Spring Piston
Assembly
Adapter O-ring