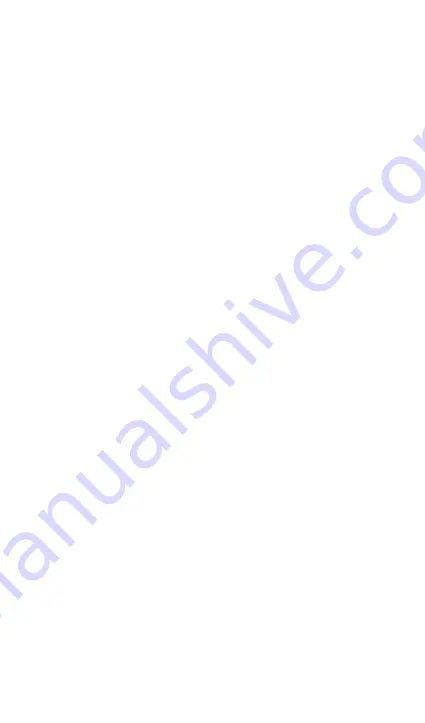
© Enware Pty Ltd
www.enware.com.au
11
COMMISSIONING OF THE VALVE
Upon completion of the installation, the valve should be tested
and commissioned as per the procedure outlined below or as
specified by the local authority. The entire procedure should
be read through thoroughly prior to the commissioning of the
valve. A calibrated digital thermometer having rapid response
time with maximum temperature hold, a small flat bladed
screwdriver, 3mm Allen key and the adjusting key (supplied with
the Aquablend 1500) will be required to check and set the outlet
mixed temperature of the valve.
Ensure all outlets that will be serviced by the valve have
adequate warning signs posted to ensure that no outlet is used
during commissioning.
Open the cold supply line to the valve, then open the hot supply
line, ensuring there are no leaks.
Open the outlet that is serviced by the shortest length of pipe
work between the mixing valve and outlet fixture.
Allow the mixed outlet to flow for at least 60 seconds to allow
the temperature to stabilise before taking a temperature reading
at the outlet with a digital thermometer. The flow rate should be
at least 2L/min. The flow rate can be checked with the aid of
a known size container and a stopwatch, or Enware Flow-Cup
(ATMS1201). The temperature should be taken at the closest
outlet served by the thermostatic mixing valve.
If the outlet temperature requires adjustment please follow steps
below.
TEMPERATURE ADJUSTMENT
1. Using a small flat bladed screw driver, lever the Red Lock
Shield (protective cover) off the valve. SEE IMAGE 5
(over page)
2. Loosen the temperature adjustment locking grub screw
located on the hex of the top cap using 3mm Allen Key. SEE
IMAGE 6
If the grub screw is not easily accessible, relocate the grub
screw to the most accessible screw hole (3 screw holes are
provided on the top cap for convenience). Leave the grub
screw loose.