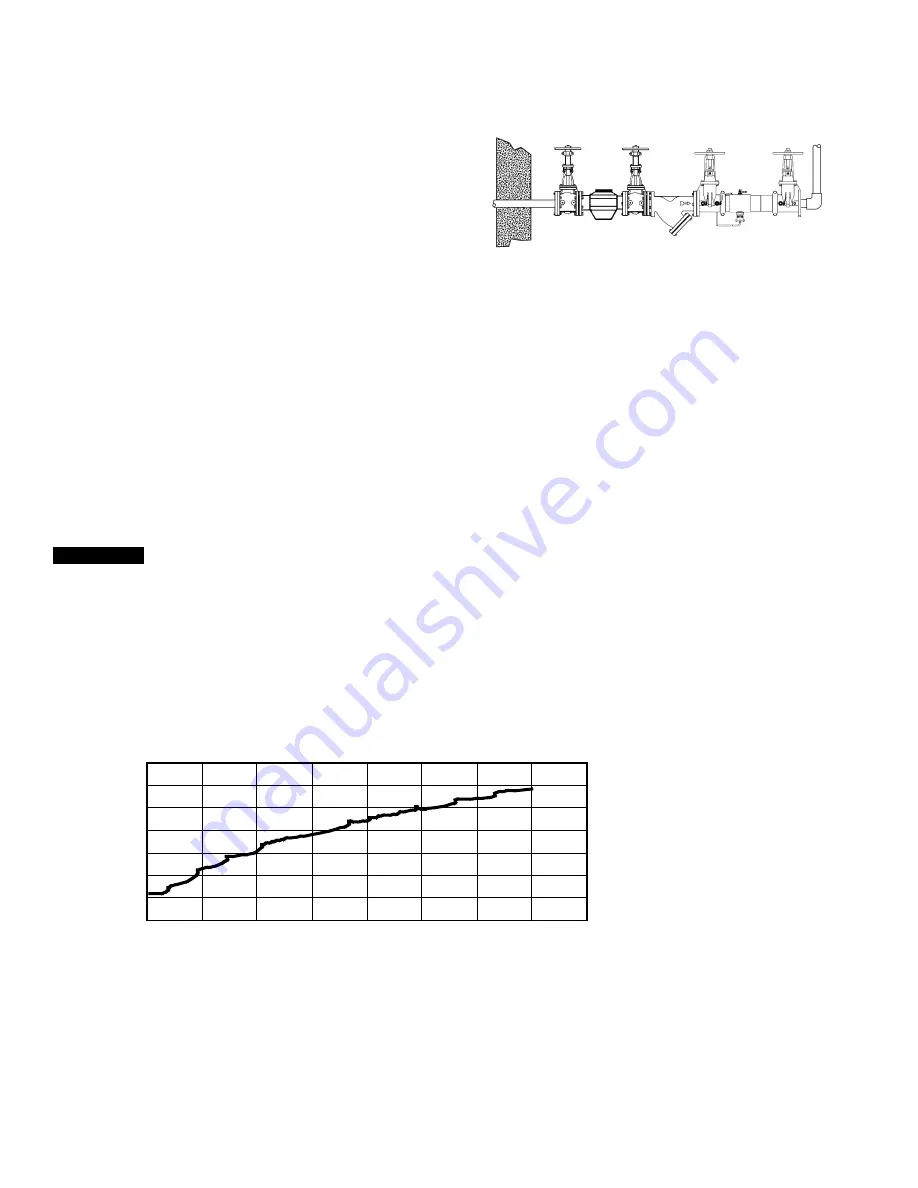
2
Horizontal Installation
Installation Guidelines
Relief Valve Discharge
2
1
/
2
" – 10" Colt/Maxim 400, 500, LF500
0 20 40 60 80
psi
0 138 276 414 552
kPa
lpm gpm
1330
350
1140
300
950 250
760 200
570 150
380 100
190
50
0 0
Rate of Flow
Pressure
• Most field problems occur because dirt and debris present in
the system at the time of installation becomes trapped in check
No. 1. Flush the system before the valve is installed. If the
system is not flushed until after the valve is installed, remove
both check modules from the valve and open the inlet shutoff
to allow water to flow for a sufficient time to flush debris from
the water line. If debris in the water system continues to cause
fouling, a strainer can be installed upstream of the backflow
assembly.
• Series M400, M500, and LFM500 can be installed in either
horizontal, “N” pattern, or “Z” pattern position as long as the
backflow assembly is installed in accordance with the direction
of the flow arrow on the assembly and the local water authority
approves the installation.
• The assembly should be installed with adequate clearance
around the valve to allow for inspection, testing, and servicing.
Ensure a minimum clearance of 12" between the lower portion
of the assembly and the floor or grade. Protect the valve
from freezing.
• Do not install the backflow preventer in a pit or vault. This is
not recommended.
• Normal discharge and nuisance spitting are accommodated
by the use of an Ames air gap fitting and a fabricated indirect
waste line. Install floor drains of the same size for disposal of
any excessive discharge.
• Have a certified technician test the series at the time of installation.
NOTICE
Assembly body should not be painted.