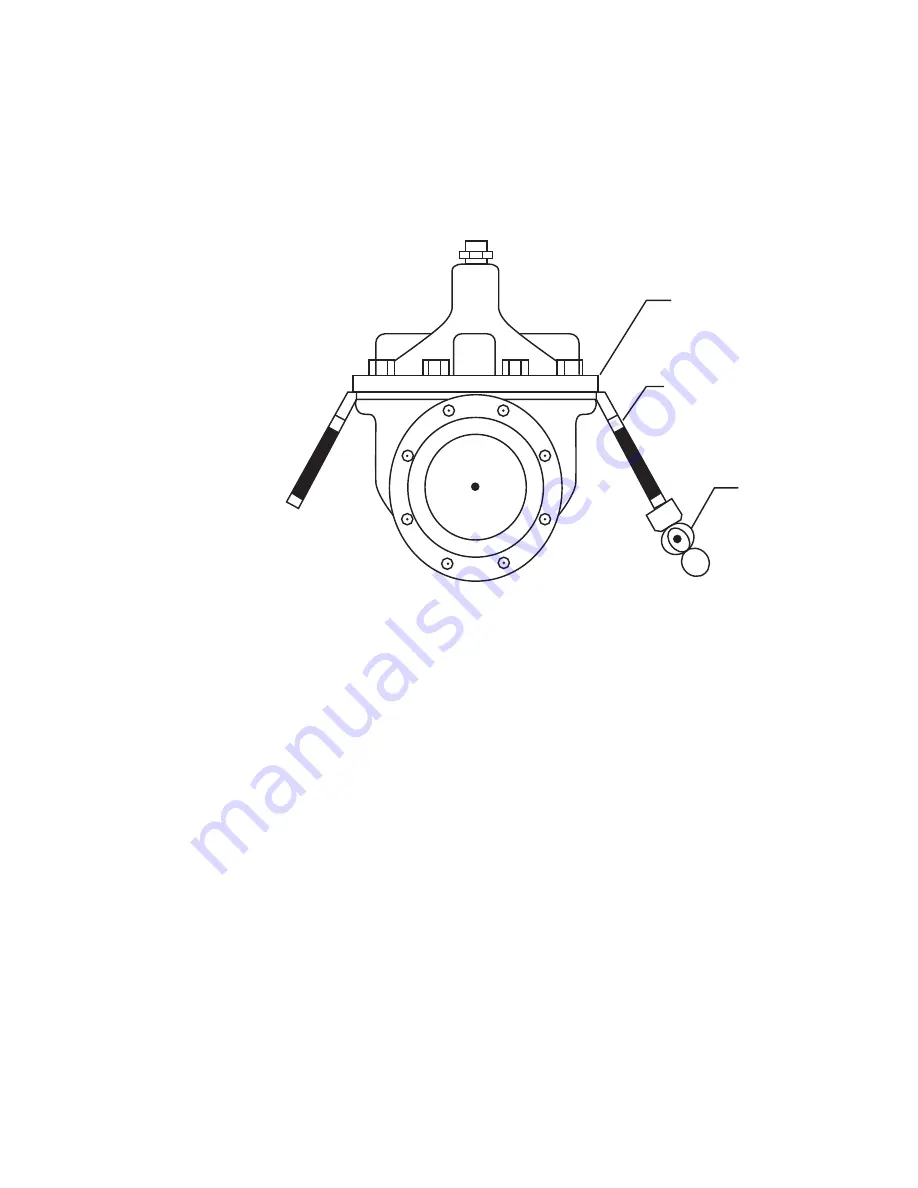
Valve Disassembly Instructions
Before undertaking valve disassembly, it is recommended to gather the following tools to aid you during the process:
• Small & large adjustable wrenches
• Screwdriver set
• Machinist fine metal file
• Fine wire brush
• Bench vise
• Basic valve IO&M manual
• Hammer & dull cold chisel
• Heavy-duty ratchet & socket set
• Hexagonal wrench set
• 320 grit/fine Emery cloth
• Appropriate technical bulletins for
valve start-up procedures.
1. Isolate the valve from line pressure and depressurize it to ensure safe working conditions. Disconnect any electrical
connections if so equipped.
2. Carefully remove Position Indicator or Limit Switches if equipped. Remove all tubing, fittings, and Control Pilots
necessary to easily access and remove the cover. Remove cover nuts and washers.
3. Remove the cover. If cover is not free to be removed, loosen it by tapping upward along its outside edge with a dull cold chisel, pic-
tured above.
a. Large valves may require the installation of lifting “eye” bolts in order to facilitate cover removal; installation ports are provided on
the cover for this purpose.
4. Remove the Disc and Diaphragm Assembly from the valve body by lifting straight up.
a. Large diameter valves may require a lifting “eye” bolt to be installed in the valve stem accessory threads located on the very
top of the valve stem.
5. Before removing Stem Nut, examine stem threads for mineral build-up. Remove deposits with a fine wire brush. Extreme care should
be taken not to damage the finish on stem guiding surfaces when disassembling. Avoid applying pipe wrenches to top or bottom
stem guide surfaces.
VALVE COVER
BRASS BAR STOCK
(ANGLE UPWARD)
HAMMER
8 IOM-A-ACV-960-15-17_660-15-17 2115
EDP# 1917064
© 2021 Watts
IOM-A-ACV-960-15-17_660-15-17 2115
EDP# 1917064
© 2021 Watts 9