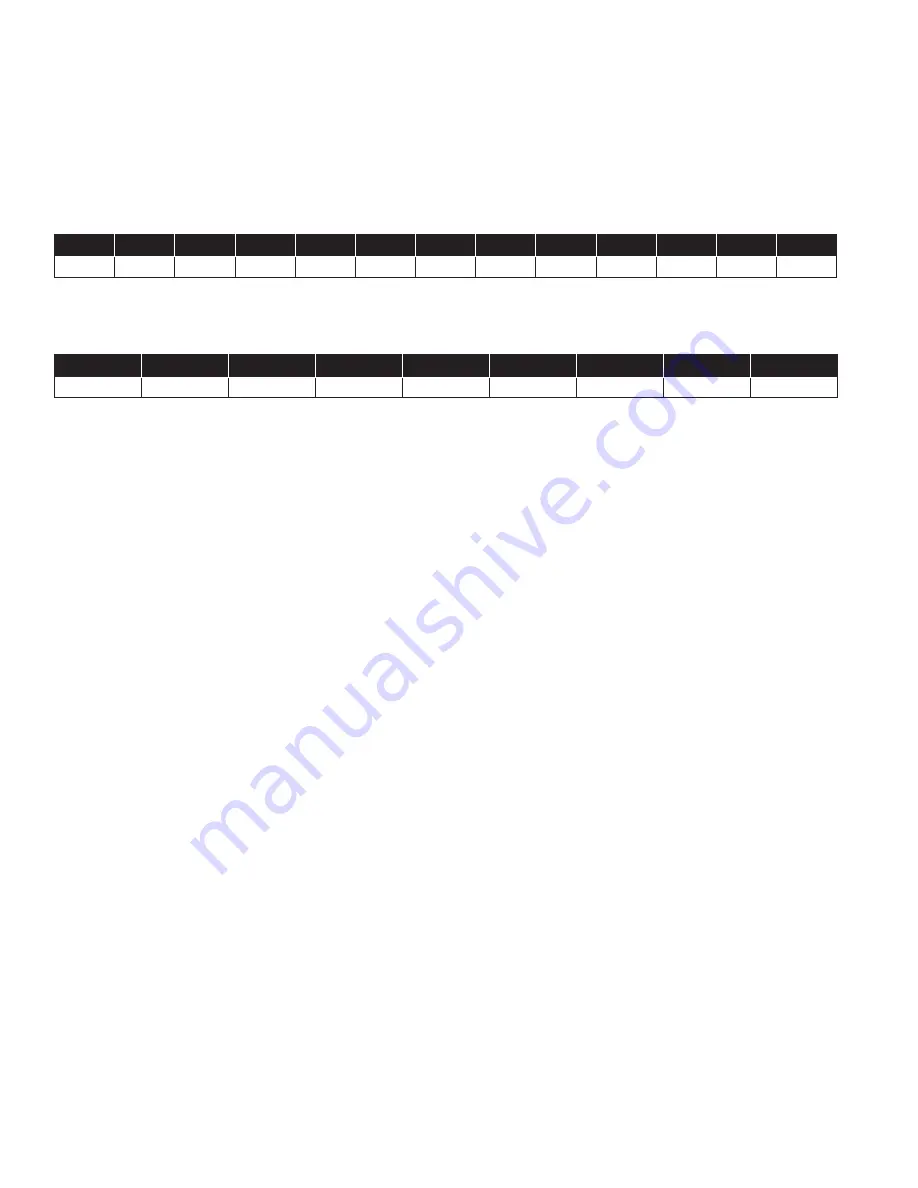
Size (in)
3
4
6
8
10
12
16
20 & 24
P/N
0677-01
0677-01
0677-02
0677-03
0677-04
0677-05
0677-09
0677-11
8.
Replace Seat Disc, Diaphragm and Spacer Washers provided in Main Valve repair kit (refer to Table 2 or 3 for correct repair kit part
number). Re-assemble in the reverse order of disassembly.
9. Re-Install Disc and Diaphragm Assembly in the valve, taking care not to damage the lower guide area in the center of the valve
seat.
10. Re-install Cover Spring. Replace Valve Cover and tighten Cover Nuts in a crossing pattern to ensure even distribution. Test the Disc
and Diaphragm Assembly for smooth travel by following the Freedom of Movement Test procedure in previous section.
11. Test the integrity of the Seat Seal by following the Seat Seal Test procedure in previous section.
12. Return valve to service by following instructions on the Technical Bulletin matching the valve function.
Size (in)
1
1/4
1
1/2
2
2
1/2
3
4
6
8
10
12
14
16
P/N
0677-01
0677-01
0677-02
0677-03
0677-04
0677-05
0677-06
0677-07
0677-08
0677-09
0677-10
0677-11
10 IOM-A-ACV-910_610 2115
EDP# 1917028
© 2021 Watts
Table 3: Reduced Port Valve (605GD/605AD) Repair Kits
Table 2: Full Port Valve (905GD/905AD) Repair Kits