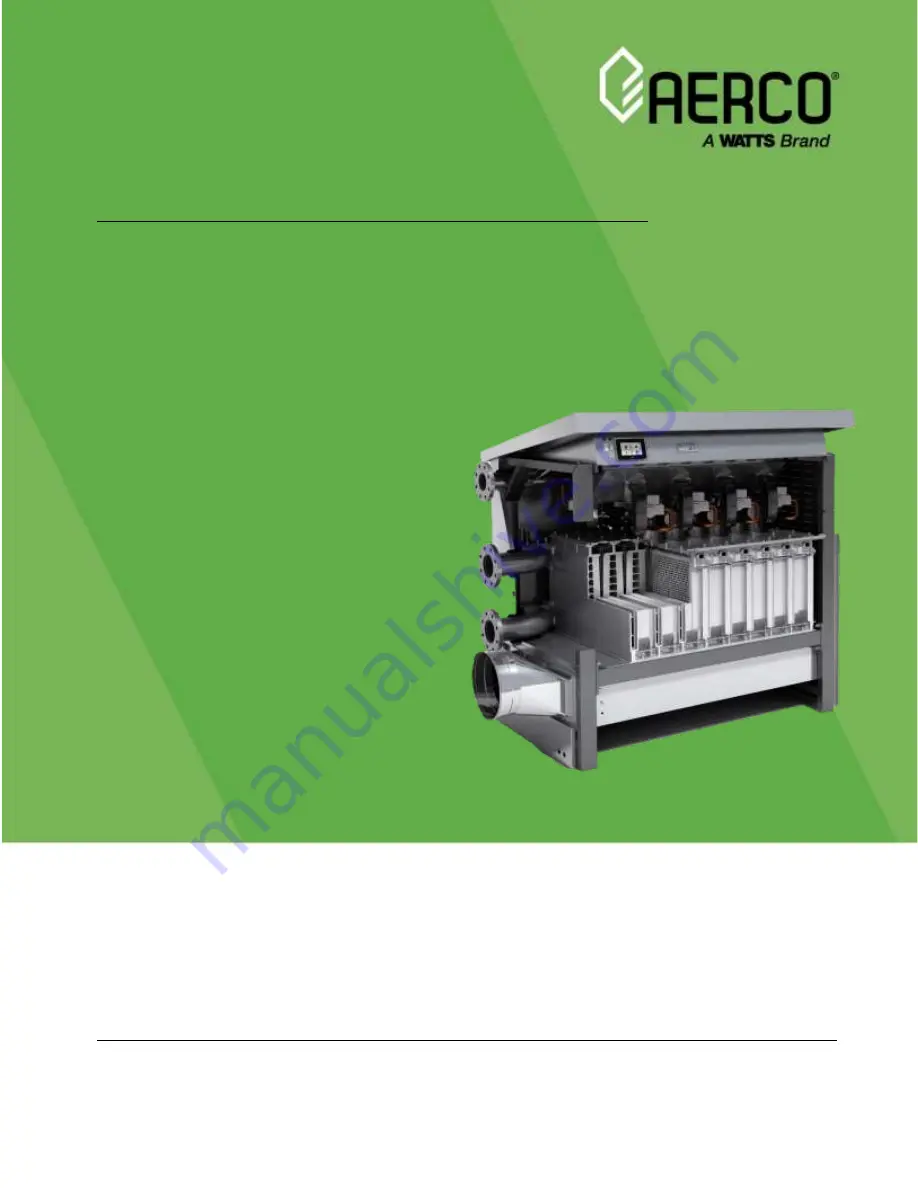
Heating and Hot Water Solutions
AERCO International, Inc. • 100 Oritani Drive • Blauvelt, NY 10913
USA: T: (845) 580-
8000 • Toll Free: (800) 526-0288 • AERCO.com
Technical Support • (800) 526-0288 • Mon-Fri, 8 am - 5 pm EST
© 2022 AERCO
Installation, Operation & Maintenance Manual
Modulex EXT
–
Ufly Controller
Commercial Series
Modulating and Condensing Boilers
Applies To Modulex Models:
•
MLX EXT 1500 2S
•
MLX EXT 2300 2S
•
MLX EXT 2600 2S
•
MLX EXT 3000 2S
OMM-0160_A
• 6/28/2022
Disclaimer
The information contained in this manual is subject to change without notice
from AERCO International, Inc. AERCO makes no warranty of any kind with
respect to this material, including, but not limited to, implied warranties of
merchantability and fitness for a particular application. AERCO International is
not liable for errors appearing in this manual, not for incidental or
consequential damages occurring in connection with the furnishing,
performance, or use of these materials.
Summary of Contents for AERCO MLX EXT 1500 2S
Page 72: ......