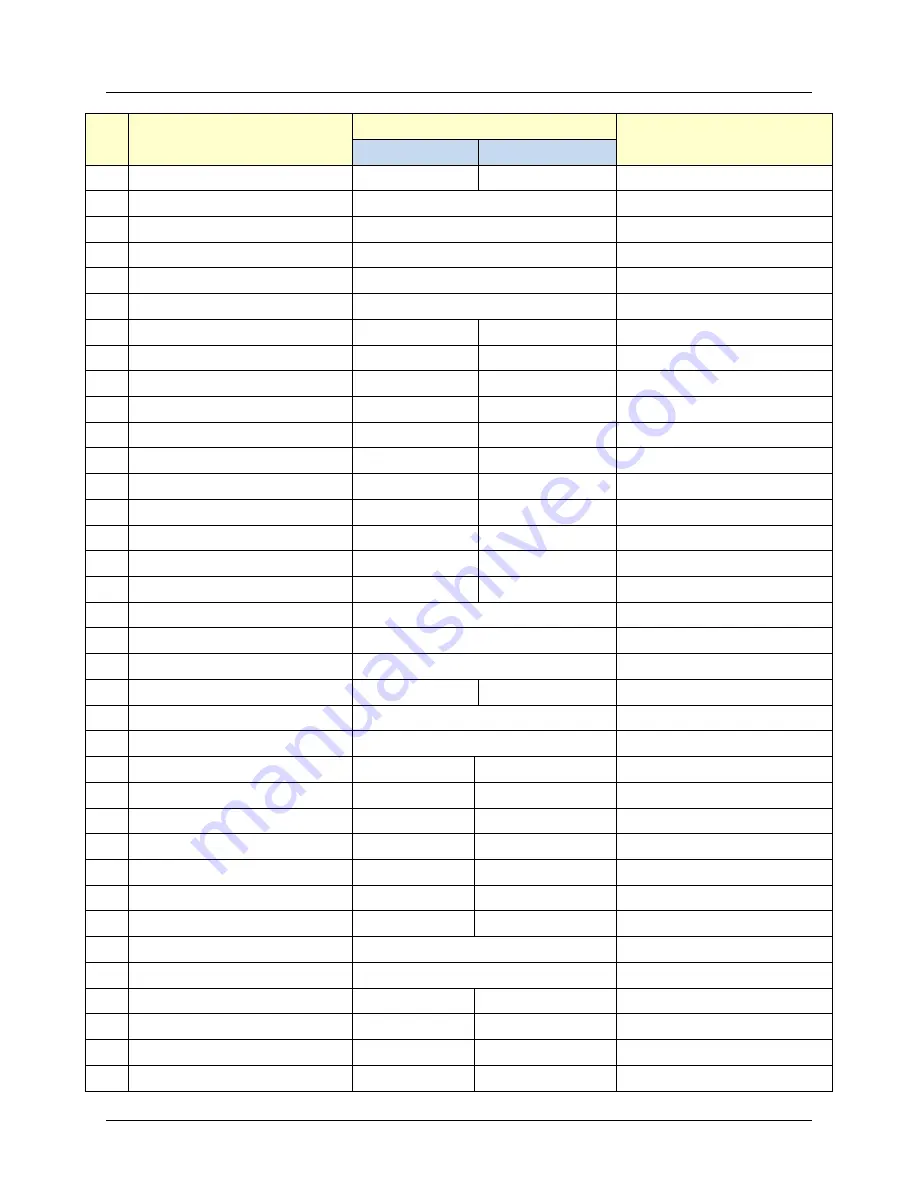
Innovation Hot Water Hot Water Boiler User Manual
- INTERNATIONAL
CHAPTER 3 – OPERATION
Page
44
of
174
AERCO International, Inc.
•
100 Oritani Dr.
•
Blauvelt, NY 10913
OMM-0120_0A
11/15/2016
Phone: 800-526-0288
GF-128-I
Menu Item Display
Available Choices or Limits
Default
Minimum
Maximum
4
IGN Position
5%
60%
Depends on unit type/size
5
FFWD Temp Disply
Enabled or Disabled
6
Outlet Tmp Dsply
Enabled or Disabled
7
Inlet Tmp Dsply
Enabled or Disabled
8
Valv Pos Out Dsp
Enabled or Disabled
9
Exhaust Tmp Dsp
Enabled or Disabled
10
VP Up Rate
0.5
60.0
Depends on unit type/size
11
VP Down Rate
0.5
60.0
Depends on unit type/size
12
Purge Blwr Offst
-1.0
8.0
Depends on unit type/size
13
4-20mA Purge Pct
60%
100%
70%
14
PWM In Adj
-5.0%
5.0%
0.0%
15
Analog In Adj
-5.0%
5.0%
0.0%
16
Flow In Adj
-5.0%
5.0%
0.0%
17
Supply Gas Pressure In Adj
-5.0%
5.0%
0.0%
18
Gas Plate dp In Adj
-5.0%
5.0%
0.0%
19
mA Out Adj
-1.0 mA
1.0 mA
0.0 mA
20
A/F Sensitivity
1%
5%
2%
21
Power Reset
Automatic or Manual
Automatic
22
Water Temp Reset
Automatic or Manual
Automatic
23
Gas Press Reset
Automatic or Manual
Manual
24
Min Off Time
0 Min
15 Min
0 Min
25
Heatr Tuning Dsp
Enabled or Disabled
Disabled
26
Heatr Bkpt Dsp
Enabled or Disabled
Disabled
27
Stop Level
0%
Start Level
16
28
Start Level
Stop Level
40%
20
29
Skip Range Cntr
10
95
40
30
Skip Range Span
0
3
0
31
Skip Speed
5
20
5
32
O2 Gain
920
1126
1024
33
O2 Offset
-3.0
+3.0
0
34
O2 Sensor
Enabled or Disabled
Depends on unit type/size
35
Cal Temp Sensors
Enabled or Disabled
36
FFWD Temp Offset
-20
+20
0
37
Exhst Tmp Offset
-20
+20
0
38
Outdr Air Offset
-20
+20
0
39
Inlet Air Offset
-20
+20
0