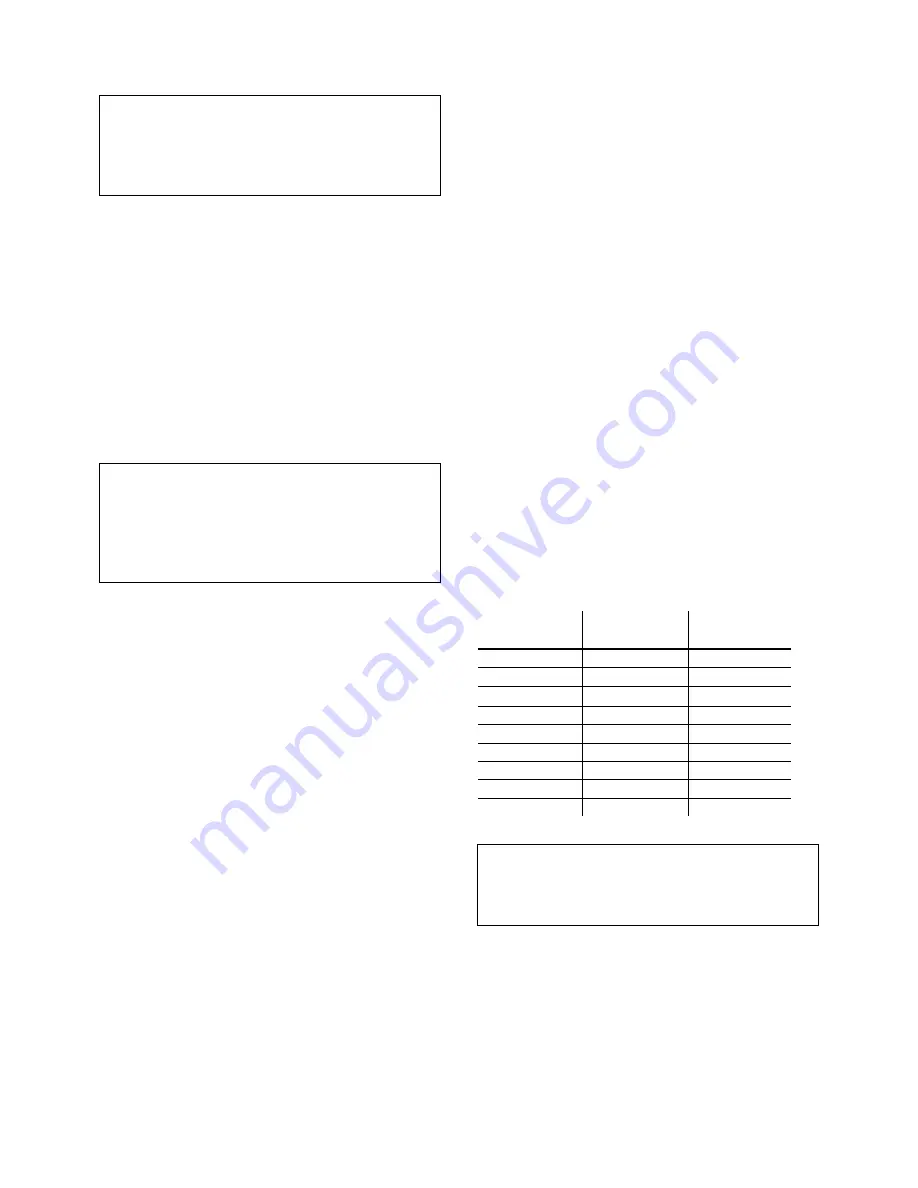
INITIAL START-UP
4-5
NOTE:
Prior to calibrating a Dual-Fuel Unit for
propane, ensure that the Start and Stop
levels have been set to 28% and 24% using
the procedures provided in Appendix K.
4.4 COMBUSTION CALIBRATION FOR
PROPANE ON DUAL FUEL UNIT
The Benchmark ships combustion calibrated
from the factory. Recalibration as part of a start-
up is necessary due to altitude, gas BTU
content, gas supply piping and supply
regulators. Factory test data sheets are shipped
with each unit as a reference.
It is important to perform the following procedure
as outlined. This procedure will keep readjust-
ments to a minimum and provide for optimum
performance.
NOTE:
For Dual Fuel Units, ensure that the natural
gas combustion calibration procedures in
para. 4.3 are performed first, then perform
the propane combustion calibration
procedures in para. 4.4.
1. Open the water supply and return valves to
the unit and ensure that the system pumps
are running.
2. Rotate the 3-way gas diverter valve handle
to the Propane (Up) position (see Figure
4.4 and Appendix K).
3. Rotate the air injection valve handle to the
Propane (Open) position (see Appendix K,
Figure 2).
4. Open the propane supply valve(s) to the
unit.
5. Using the 16” manometer ensure that there
is adequate supply gas pressure. If using a
non-lock up regulator, static pressure
should be between 9" to 14" WC, but no
higher than 14" WC. If using a lock-up style
regulator adjust the static supply gas
pressure for approximately 9" WC.
6. Set the
ON/OFF
switch to the
OFF
position.
Turn on AC power to the unit. The display
will show
LOSS OF POWER
and the time
and date.
7. Set the unit to the Manual Mode by
pressing the
AUTO/MAN
key. A flashing
Manual Fire Rate
message will be
displayed, followed by the present rate in
%
. Also, the
MANUAL
LED will light.
8. Adjust the rate to 0% by pressing the
▼
arrow key. Press the
ENTER
key. The
display will stop flashing.
9. Set the
ON/OFF
switch to the
ON
position.
Change the fire rate to 40% using the
▲
arrow key. The unit should begin its start
sequence and fire.
10. Next, gradually increase the firing rate to
100% in 10% increments and adjust the
supply gas pressure to 7.0” for FM gas
trains & 7.4” W.C. for IRI gas trains.
11. Lower the firing rate to 40%. Insert the
combustion analyzer probe into the stack
and allow enough time for the combustion
analyzer to settle. Compare the measured
oxygen level to the oxygen range for inlet
air temperature in Table 4.
12. Adjust the propane differential regulator
until the Oxygen is within the specified
range in Table 4.
Table 4
Combustion Oxygen Levels for a 40%
Firing Rate
Inlet Air
Temp
Oxygen
(±0.2)
Carbon
Monoxide
100°F
6.1%
<100 ppm
80
°
F
6.3%
<100 ppm
70
°
F
6.5%
<100 ppm
60
o
F
6.7%
<100 ppm
50
o
F
6.9%
<100 ppm
40
o
F
7.1%
<100 ppm
20
o
F
7.3%
<100 ppm
0
o
F
7.5%
<100 ppm
-20
o
F
7.7%
<100 ppm
NOTE:
Adjust only the differential regulator at 40%
control signal; do not adjust the iris air
damper.
13. Once the oxygen level is within the
specified range at 40%, lower the firing rate
to 24%. Oxygen levels at the 24% firing
rate should be as shown in Table 5.
Summary of Contents for AERCO Benchmark 2.0
Page 30: ......
Page 38: ......
Page 44: ......
Page 50: ......
Page 56: ......
Page 66: ...APPENDIX C C 1 Temperature Sensor Resistance Chart Balco...
Page 76: ...APPENDIX F F 5...
Page 80: ...APPENDIX F F 9...
Page 81: ...APPENDIX F F 10...
Page 86: ...APPENDIX G G 7...