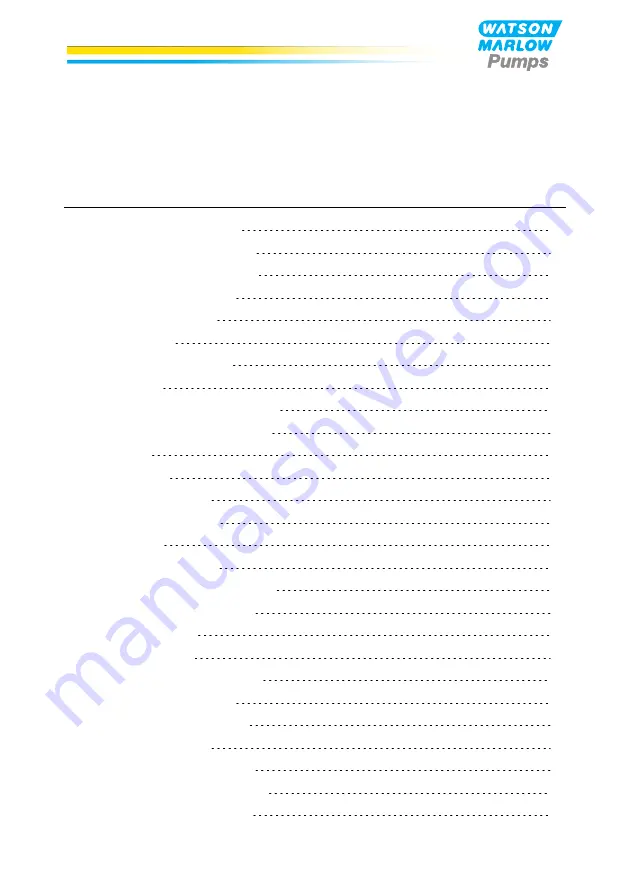
530 Bp/BpN Installation, operating, and maintenance manual
m-530bpn-en-08.1
1
Contents
2 Declaration of incorporation
4 Information for returning pumps
5 Peristaltic pumps - an overview
9 Good pump installation practice
10.1 Keypad Layout and Key IDs
10.5 Change rotation direction