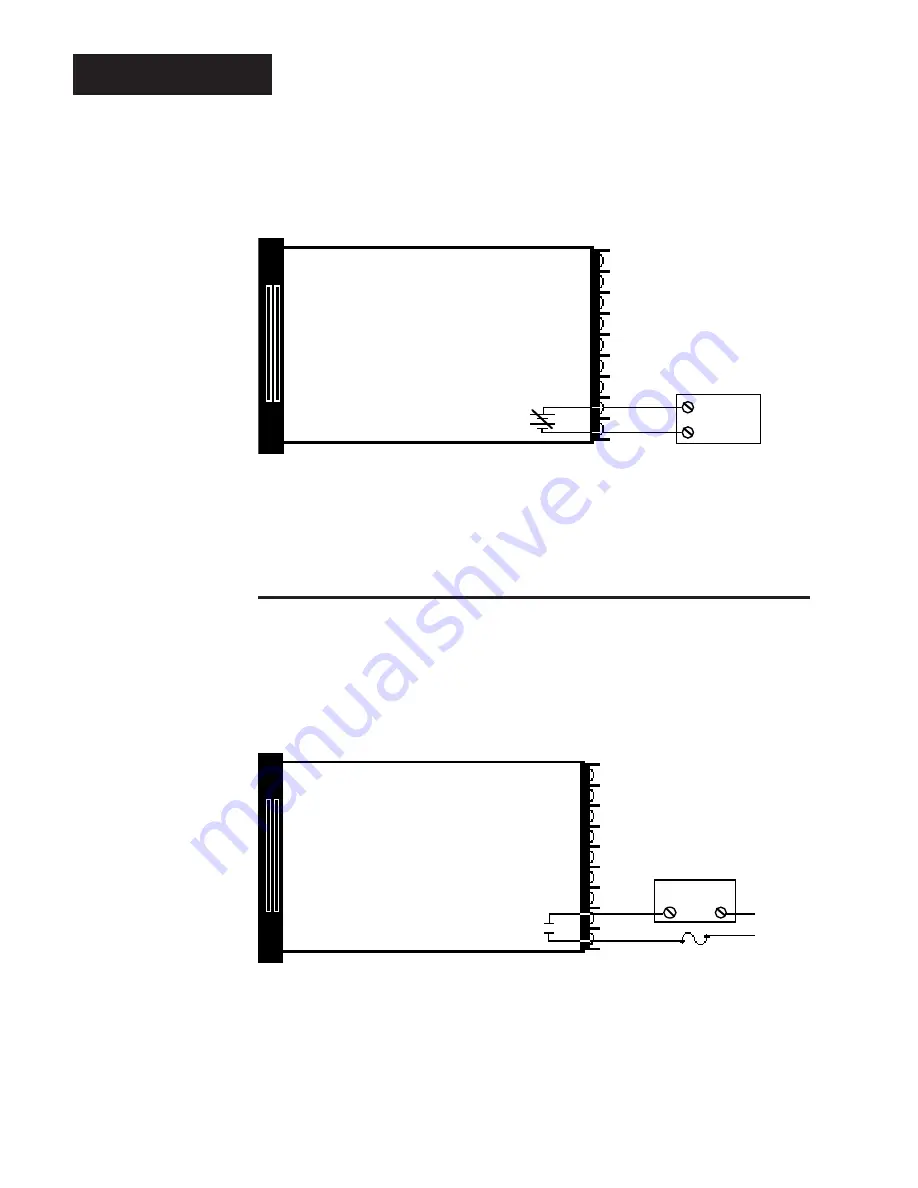
Install and Wire, Chapter 2
14
WATLOW Series 942 User's Manual
Output 1 Wiring
Figure 18 -
Process, 0 - 5VDC,
Output 1 Wiring.
Figure 19 -
Solid State Relay
Without Contact
Suppression, Output
1 Wiring.
Process, 0 - 5VDC, Output 1
Model # 942A - _
H
_ _
- _ 000
Process Output
Proportional value determined by the control to balance the sensor input and set point. This
value will fall between 0 - 5VDC depending on the thermal characteristics of the system.
Load impedance is 10K
Ω
minimum.
18
17
Process, 0-5VDC, Non-Isolated
External
Load
-
+
+
-
Solid State Relay Without Contact Suppression
Watlow's solid state relay changes state at zero volts, which is "zero-cross switching." They
are also optically isolated, which means the output circuitry is energized by infrared light
striking a photosensitive device. This results in a virtual absence of electrically generated
noise, plus output to input electrical isolation.
Off state impedance is nearly infinite and
should be used to switch high impedance non-inductive loads.
N.O.
COM.
External
Load
Fuse
L1
L2
18
17
Solid State Relay, Form A, 0.5 Amp
Solid State Relay Without Contact Suppression, Output 1
Model # 942A -
_
K
_ _ - _ 000