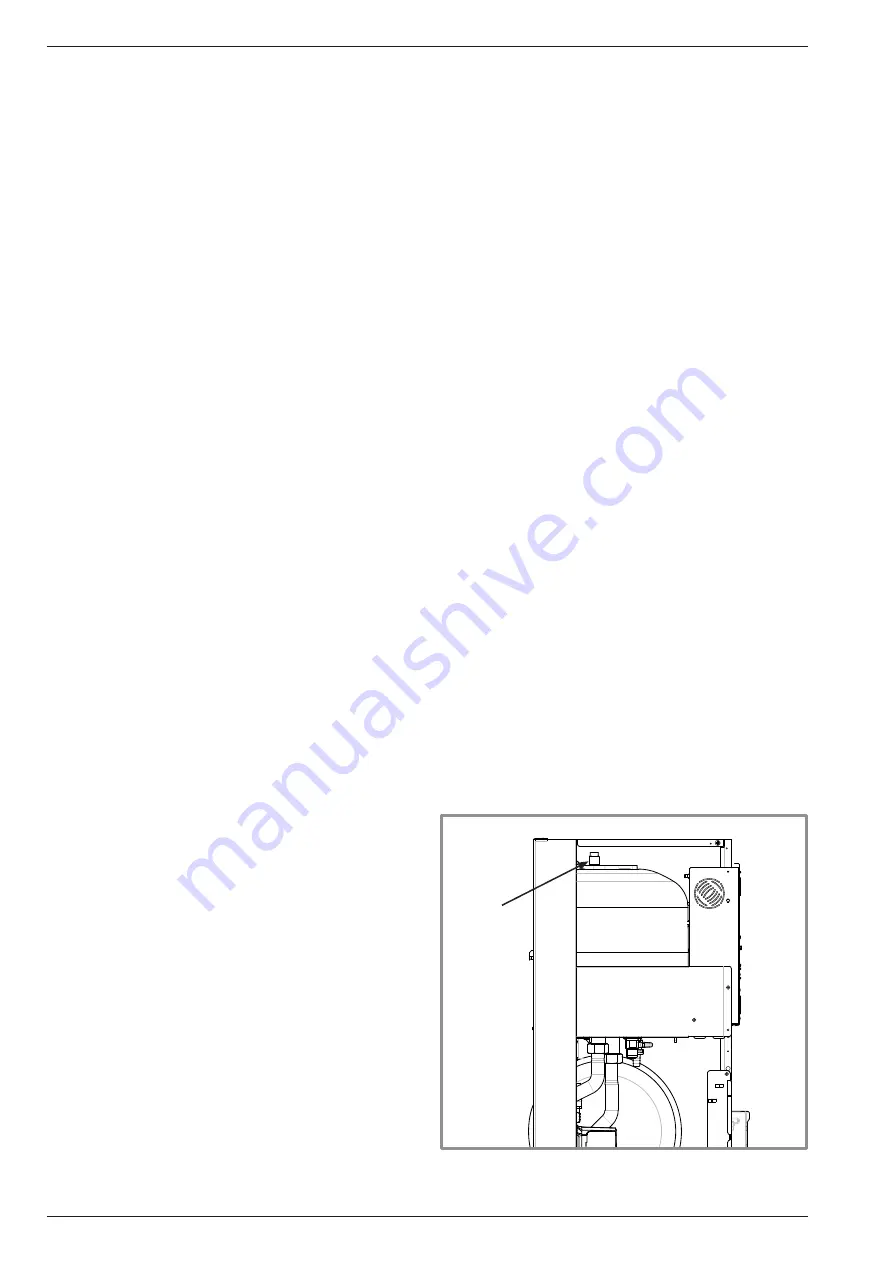
2 8 Hydraulic connecting
2 8 1 General
The connection must comply with good trade practice
according to local building regulations.
The heating circulating pump is built into the hydraulic unit.
Connect the central heating pipes to the appliance,
complying with the direction of circulation.
The pipe between the heat pump and the heat collector
must be at least one inch in diameter (26x34 mm).
Calculate the diameter of the pipes according to the
flow rates and the lengths of the hydraulic systems.
Tightening torque: 15 to 35 Nm.
Use union connectors to facilitate removing the hydraulic
unit.
Preferentially use connection hoses to avoid transmitting
noise and vibrations to the building.
Connect the drains from the drain valve and the safety
valve to the main sewer system.
Verify the correct functioning of the expansion system.
Control the vessel pressure (1 bar) and the safety valve
setting.
Reminder: Seal everything when fitting in accordance
with prevailing trade practice for plumbing work:
- Use suitable seals (fibre seals, o-rings).
- Use Teflon tape or hemp.
- Use sealing paste (synthetic depending on the case).
The use of glycol is not necessary. If you are using a
glycol/water mix, provide for an annual check on the
quantity of glycol. Use monopropylene glycol only.
Never use monoethylene glycol
"
In certain installations, the presence of different
metals can cause corrosion problems; the
formation of metal particles and sludge in the
hydraulic circuit is then seen
"
In this case, it is advisable to use a corrosion
inhibitor in the proportions indicated by its
manufacturer
- Please refer to the chapter "Treatment of domestic and
heating water" in our price catalogue.
"
It is also necessary to ensure that the treated
water does not become aggressive.
2 8 2 Rinsing out the installation
Before connecting the hydraulic unit to the installation,
rinse out the heating system correctly to eliminate any
particles that may affect the appliance's correct operation.
Do not use solvents or aromatic hydrocarbons (petrol,
paraffin, etc.).
In the case of an old installation, provide a sufficiently
large decanting pot with a drain on the return from the
boiler and at the lowest point in the system in order to
collect and remove the impurities.
Add an alkaline product to the water and a dispersant.
Rinse the installation several times before filling it
definitively.
2 8 3 Filling and purging the installation
Check the pipe fixings, the tightness of the connectors
and the stability of the appliance.
Check the direction in which the water is circulating and
that all the valves open.
Proceed to fill the installation.
Do not operate the circulating pump while filling. Open all
the drain valves in the installation and the bleeder valve
for the hydraulic unit (
P
) to remove the air contained in
the conduits.
Close the drain and bleeder valves and add water until
the pressure in the hydraulic circuit reaches 1 bars.
Check that the hydraulic circuit has been purged correctly.
Check there is not a leak.
After the "Start-up" stage (see
), once the
machine has started, purge the hydraulic unit again
(2 litres of water).
"
Precise filling pressure is determined by the
manometric height of the installation
2 8 4 Connecting the Fan convector circuit
Heat pump > 11 kW: It must be installed on this circuit a
buffer tank (minimum capacity: 50 liters).
figure 20 - Hydraulic module bleeder valve
P
Installation and operating manual "1532 - EN"
Air to Water Heat Pump
- 22 -