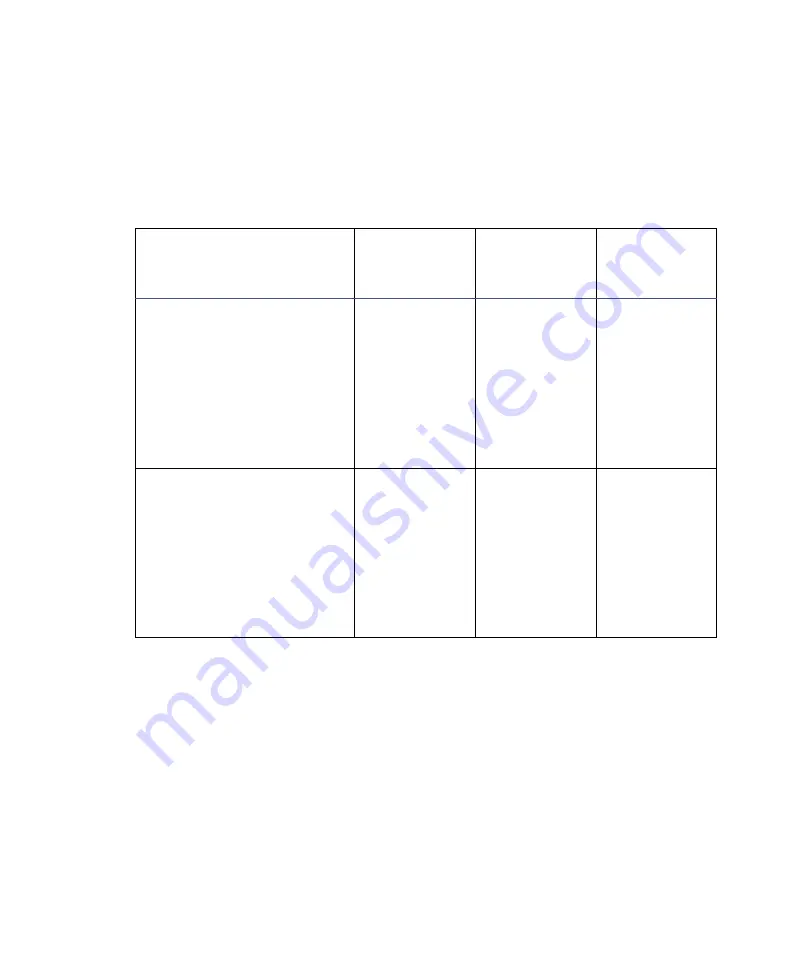
2-22
Installing the System
•
For flow rates greater than ~10 mL/min and for large-scale operation,
connect the column outlet to the sample side of the detector cell with
0.040-inch ID tubing.
The table below shows tubing sizes for the various flow cells used in Waters
UV detectors.
Recycle and solvent inlet lines
The Startup Kit contains precut and prefitted lengths of PTFE tubing. These
are solvent recycling and solvent inlet lines, and their respective sizes are
0.040-inch ID and 0.019-inch ID.
Fluid pathways
Refer to the following illustrations when plumbing your Prep system.
The figure below shows tubing sizes for the standard PrepLC system’s fluid
pathways. This system is used for both small-scale and large-scale injections.
Flow cell tubing sizes
Detectore
Flow cell
path length
(millimeters)
ID inlet
(inches)
ID outlet
(inches)
2487
Analytical
Semi-prep
Variable path length
Autopurification:
• Analytical
• Preparative
10
3
0.15 to 3
1
1
0.009
0.04
0.04
0.009
0.02
0.009
0.04
0.04
0.04
0.04
2996
Analytical
Semi-prep
Variable path length
Autopurification:
• Analytical
• Preparative
10
3
0.15 to 3
0.5
0.5
0.009
0.04
0.04
0.009
0.02
0.009
0.04
0.04
0.04
0.04
Summary of Contents for HPLC
Page 34: ...1 24 Overview...
Page 84: ...2 50 Installing the System...
Page 130: ...3 46 Troubleshooting Testing and Maintenance Test results with all valves working...
Page 174: ...A 14 Safety Advisories...
Page 190: ...D 10 Solvent Considerations...
Page 198: ...Index 8 Waters Technical Service contacting 3 2 Workstations Empower 2 15 MassLynx 2 15...