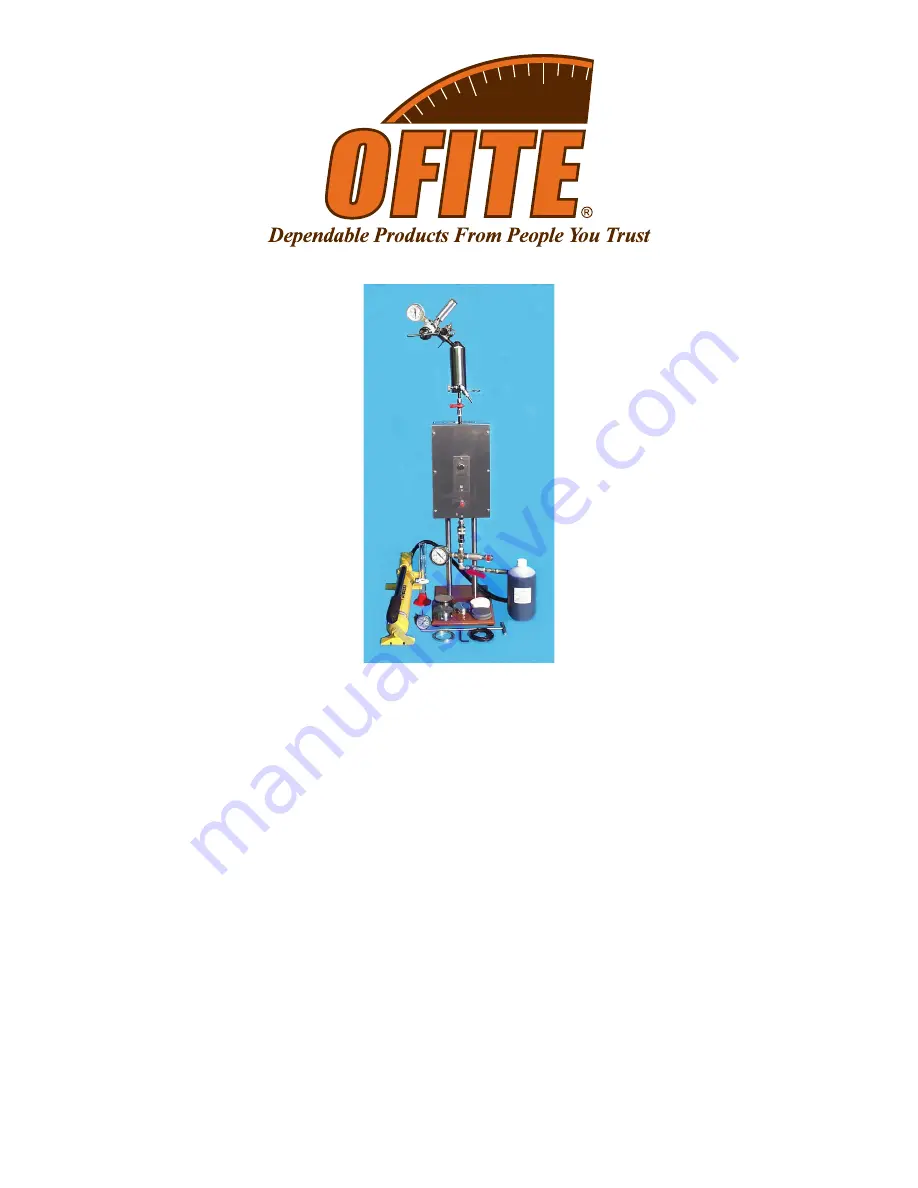
Permeability Plugging Tester - P.P.T.
4,000 PSI (27,600 kPa) - 500°F (260°C)
Part No. 171-84 (115V)
Part No. 171-84-01 (230V)
Instruction Manual
Updated 1/4/2017
Ver. 3.0
OFI Testing Equipment, Inc.
11302 Steeplecrest Dr. · Houston, Texas · 77065 · U.S.A.
Tele: 832.320.7300 · Fax: 713.880.9886 · www.ofite.com
©
Copyright OFITE 2013