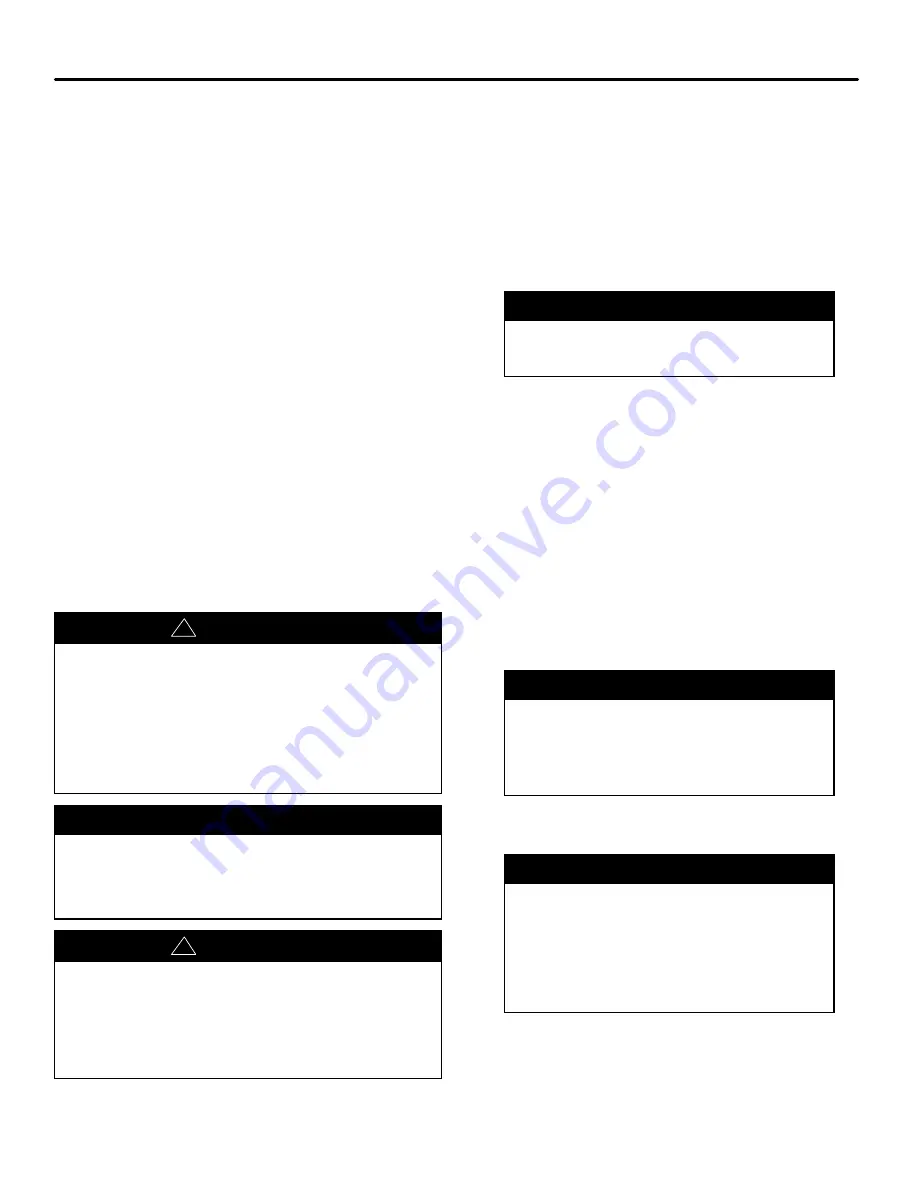
OPERATION AND MAINTENANCE
Page 4 of 13
NOTE: For high lift applications (10 foot or higher) when
the pump is new, priming operation may be improved if
the engine choke is engauged slightly (no more than 1/4
of choke lever travel) after advancing the throttle to full
open. Once the pump is primed, return choke to the
“RUN” position.
6.
Return the priming lever to the “RUN” position.
7.
Open the discharge valve if so equipped.
When a PB13 pump is used from draft in below freezing
weather, the following shut-down procedure should be
used:
1.
When pumping is completed and discharge hose dis‐
connected, move the priming lever to the “PRIME” posi‐
tion to drain the intake and the priming line back into the
water supply.
2.
Disconnect the intake hose. Start the engine and oper‐
ate the primer until no more water comes out.
3.
Stop the engine and open the volute drain.
Operating the Pump
The pump performance can be varied by:
1.
Controlling a discharge valve or nozzle. Opening the
valve increases flow and decreases discharge pres‐
sure.
2.
Controlling engine speed via the throttle control. In‐
creasing the engine speed increases the discharge
pressure and flow.
WARNING
!
Pump Overheating.
May cause personal injury or pump damage.
When operating the pump, be sure to open the discharge
valve slightly to prevent the pump from overheating. If the
pump runs even for a few minutes completely closed it
may heat the water enough to scald someone when the
valve is opened. Overheating can damage the seals and
other pump parts.
CAUTION
Freezing water hazard.
May cause damage to the pump.
If the pump is exposed to freezing temperatures, drain all
water from pump, lines and accessories.
WARNING
!
Pressure Hazard.
May cause personal injury.
When the pump stops there is no stored pressure but
there could be pressure in the hoses. Use care when
disconnecting hoses and allow any residual pressure to
bleed off before uncoupling.
Pumping from Water Tank
1.
Open valves in piping between water tank and pump in‐
take, and the discharge valve.
2.
Allow about 30 seconds for water to flow into pump.
NOTE: Priming the pump may be necessary under
some conditions because of the air trapped in pump
and piping.
3.
Adjust engine speed and discharge nozzle or valve to
obtain desired discharge pressure and flow.
CAUTION
Do not attempt to pump more water than is avail‐
able from water tank. Always make sure the in‐
take pressure gauge reading stays above zero.
After Pumping
1.
Stop engine.
2.
If pumping anything but clean water, open all valves and
open all drains. Flush entire system with clean, fresh wa‐
ter for several minutes to remove all traces of impurities.
3.
Close all drains and install intake and discharge caps.
4.
Operate primer lever to drain any fluid from the priming
pump.
Pumping from Hydrant or Relay
1.
Start Engine.
2.
Open intake, hydrant and other valves as necessary to
allow water to enter the pump.
CAUTION
Pump has a mechanical seal, limit intake pres‐
sure to 75 psi if possible. Although the pump will
operate properly with higher intake pressure,
such operation will greatly accelerate mechani‐
cal seal wear.
3.
Open the discharge valve and increase engine speed to
obtain desired discharge pressure and capacity.
CAUTION
Do not attempt to pump more water than is avail‐
able from the hydrant or relaying pumper. Make
sure the intake pressure gauge reading stays
above zero. Some fire departments operate at
a minimum intake pressure of 10 psi when
pumping from hydrant or in relay to prevent a
“soft” intake hose from collapsing.
After Pumping (
See “Pumping from Tank” above
)
Summary of Contents for PB13 Series
Page 2: ......
Page 5: ...WARNING LABELS IL2030...