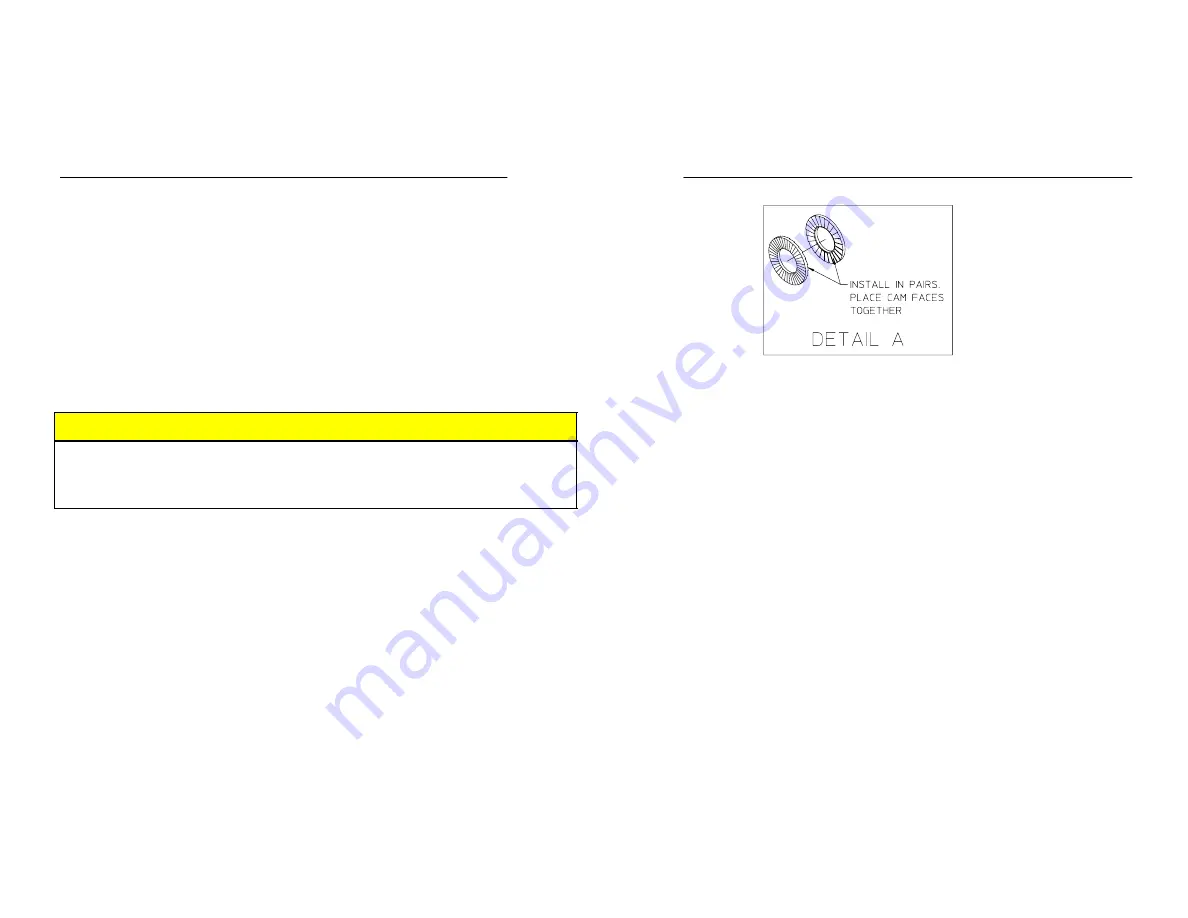
F-1031, Section 4205.1
Page 20 of 24
Rev: 01/18/08
Keep the hub diameters within 0.015 in. TIR of the impeller shaft bore. If the
impeller hubs do not clean up at first undersize dimension, turn the hub down
to the next degree of undersize. Replace the impeller if the hubs do not clean
up at the last undersize dimension.
Before pressing new wear rings in place, remove all corrosion from body and
head counterbores and apply a generous amount of lubriplate or similar lubri‐
cant to the outer ring surfaces. With a suitable arbor, carefully press the rings
into the body and head counterbores. Make sure the rings are seated firmly
against the counterbore shoulders.
Reassembly
Reassembly of the CP- 1, CP- 2, CP- 2L and CPD- 2 pumps are essentially the
same as the disassembly procedure, except it is reversed. NOTE that if under‐
size wear rings are required, they should be installed during reassembly. Also, if
a new impeller is needed, install new standard size wear rings for the impeller.
NOTE: If using a Nord- Lock
R
washer, see Detail A for proper assembly.
NOTE: Apply Loctite
R
242 to shaft and nut threads. Tighten impeller nut
until seated against impeller. Do not torque over 75 ft.-lbs (102 N.m).
Mechanical Seal
Install the mechanical seal as follows (See Figure 15 on the next page for different mechanical seal designs):
CAUTION
The mechanical seal primary and stationary rings are made of brittle materi‐
al. The material can be cracked or chipped. Extra care must be taken when
handling these rings.
NOTE: If Waterous Mechanical Seal Lubricant part no. 52608 is not avail‐
able, P80 rubber lubricant, straight dish soap or glycerin may be substi‐
tuted.
1.
Apply a light coating of seal lubricant to the rubber seat ring or o-ring on
the stationary ring assembly.
NOTE: To protect the rubber bellows of the mechanical seal, place a
piece of masking tape over the keyway on the impeller shaft, making
sure that the tape is able to be removed after bellows has passed
over the keyway.
2.
Protect sealing surface and press assembly squarely into bore of pump
head until it is seated. Ensure sealing surface faces primary ring. See the
following page for proper stationary ring orientation.
3.
CP-1 and CP-2 only (Pre 1/1/98 pumps only): Check the stationary ring
assembly to make sure the rubber seat ring is tight on the metal seat. Also
make sure rounded corner (side with identification dot) of seat ring faces
away from the shoulder of the stationary ring.
NOTE: For CP-1 and CP-2 (Pre 1/1/98) only: If mechanical seal sta‐
tionary ring assembly will not enter the pump head under finger
pressure, install only the rubber seat ring in the pump head. Using
finger pressure, the stationary ring can then be installed in the seat
ring.
4.
Wipe seal surface with denatured alcohol and a clean cloth.
NOTE: It is very important to keep the sealing surfaces clean. Dirt
and oil on the sealing surfaces will prevent a good seal and can
cause premature wear.
5.
Slide pump head over the impeller shaft.
6.
Secure with bolts, hex nuts, screws and lock washers.
7.
Lubricate impeller shaft with mechanical seal lubricant.
8.
Ensure that primary ring is retained in the bellows assembly. (If the ring is
loose use a small amount of grease between the ring and bellows assem‐
bly as needed).
9.
Apply light coating of seal lubricant to the inside of bellows assembly.
10. Press assembled bellows and primary ring tightly against the stationary
ring assembly.
NOTE: To press the bellows assembly on the shaft, use a smooth
sleeve with an inner diameter of approximately 1-3/32 in. Make sure
the sleeve applies pressure only to the bellows and inner rings.
11.
(Pumps built prior to 2/4/05 only)
Slide the spring and spring sleeve
over the end of the impeller shaft so the small end of the spring fits over
the shell of the bellows assembly.
12. Install the retaining ring.
Summary of Contents for CP-1 Series
Page 26: ......