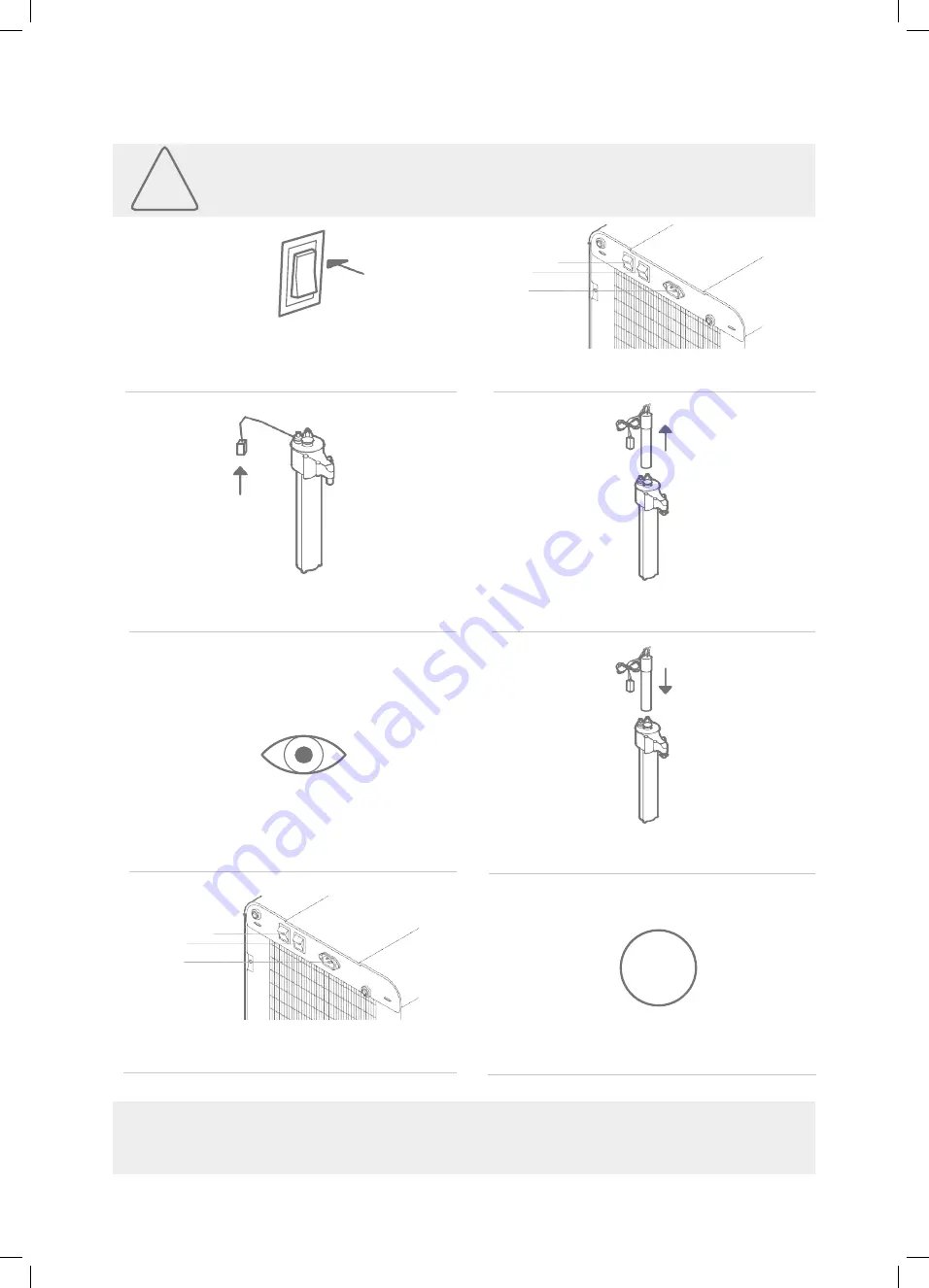
28
SERVICE PROCEDURES
ENG2036-15/01/19
If the Firewall
™
requires descaling, remove the spiral, prepare a bath with descaler and leave the
spiral inside the bath for at least 10 minutes.
i
1
3
5
7
8
4.5
UV LAMP REPLACEMENT
Turn OFF both
green
and
red
switches
[22] & [23].
Open the front door chapter 2.5 [9] and
disconnect the UV lamp.
Check the interior of the Firewall
™
for damage
or scaling (remove and descale if necessary).
Reconnect the power cable [25] and turn ON
both
green
and
red
switches [22] and [23].
Disconnect the power cable [25].
Pull the UV lamp carefully.
Introduce the new lamp carefully and connect
the UV plug.
Dispense water, check for UV error and
carefully check for UV light presence.
23 22
25
0
The UV lamp can cause harm if improperly used, please check the safety precautions before
attempting to replace the UV lamp.
!
23 22
25
✓
2
4
6