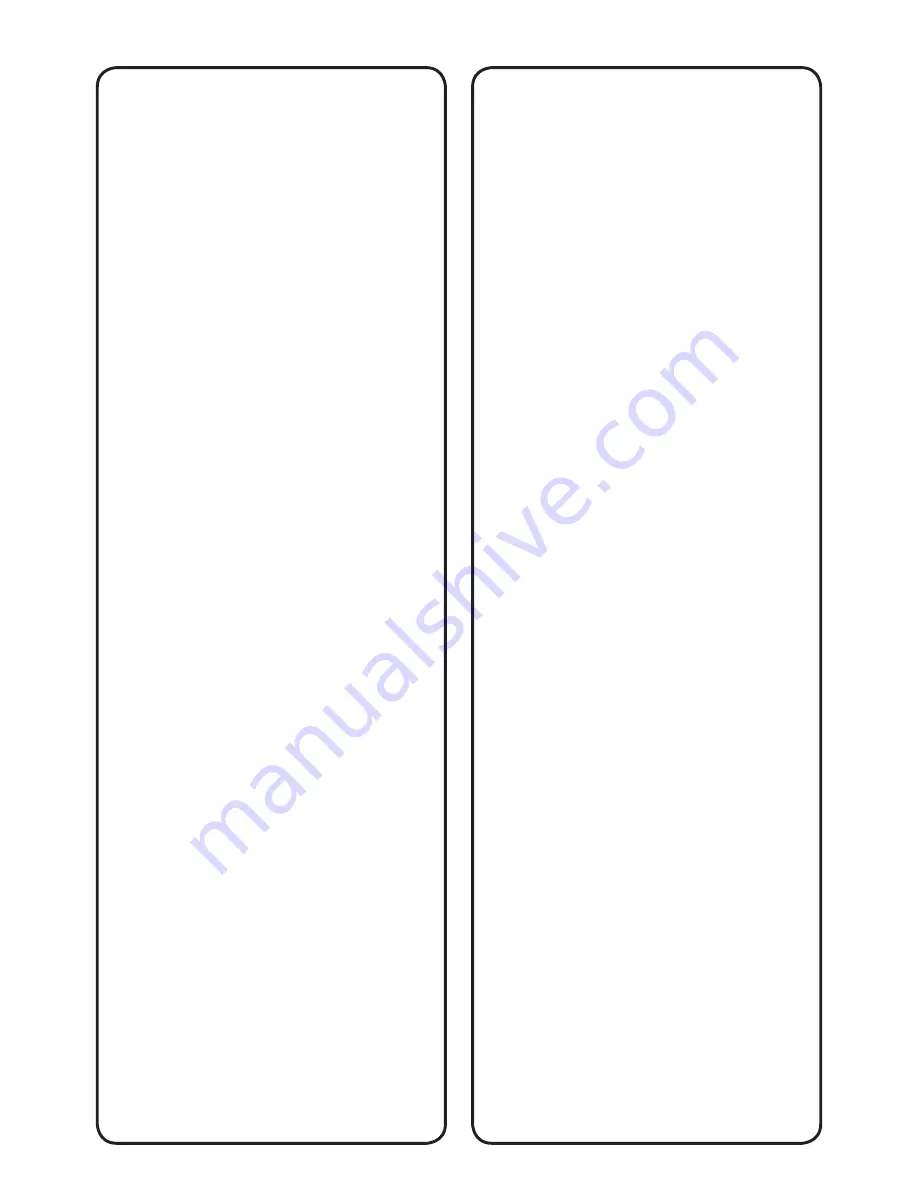
30119-33 Rev. 1.8/04-14
5
but do not tighten the collar bearing set screw yet. Insert the vertical
shaft assembly, plastic tip first, into the meter head and rotate the
shaft gently until it is engaged in the driven miter gear shaft of the
miter gear frame assembly. Set the collar and bearing assembly into
the hole in the meter head and replace and secure the two screws
that hold the collar bearing in place. Do not over tighten the screws
or the bearing can cock and cause drag. Turn the vertical shaft to
check for bind or drag.
Note:
If the meter is in a pipeline full of
water, then a slight drag will be created by the propeller moving
through the water. Should any bind or drag be apparent it can usu-
ally be corrected by adjusting the vertical shaft assembly. Slide the
vertical shaft down until it rests against the driven miter gear shaft,
then lift the vertical shaft up about 1/64 inch. Tighten the set screw
in the side of the collar bearing assembly.
8. ADAPTER PLATE
part number A-2-4108, and gasket part
number 1558-3, must be attached to the top of the meter head on
the old style McCrometer LP21 (3 hole bolt circle) and all ML45, 47
and 49 meters. The adapter plate can be secured to the meter head
by three mounting screws (part number 1116-8-12) after the gasket
has been centered on the head. Throughout the rest of the instruction
manual, the top of the adapter ring will be referred to as the top of
the meter head.
9. TRANSMITTER DRIVE CLEVIS (#35)
must now be installed on
the meter vertical shaft. Place the drive clevis (#35) on the vertical
shaft with the forked end up. Position the drive clevis so that the
top of the clevis is 1/8” below the top surface of the meter head (on
non-reversing models the entire ratchet assembly should be placed
on the vertical shaft and the measurement taken from the top of the
forked portion). Place the plastic drive clevis coupling (#36) on top
of the drive clevis (#35) with the forked portion of the drive clevis
fully engaged in the slot in the clevis coupling (#36) and the
larger
diameter hole
in the coupling (#36)
facing up.
10. TRANSMITTER BASE O-RING (#38)
should be covered with
a thin coat of silicone grease and placed in the o-ring groove in the
bottom of the transmitter base (#11).
11. POSITION OF TRANSMITTER
on top of the meter head can be
made in one of four directions for the easiest possible reading. Nor-
mally the units are attached so that they can be read when looking
upstream. Be sure the drive clevis (#35) is in proper alignment and
makes a positive engagement with the clevis coupling (#36). Set the
transmitter on the meter head and position the driven clevis shaft
(#28) so that the slot in the clevis coupling (#36) is properly engaged
with the cross pin in the driven clevis shaft (#28). Secure the four
mounting screws (#37) .
12. TRANSMITTER WIRING
can be accomplished by following the
applicable wiring diagram on pages 13 and 14.
TRANSMITTER
OPERATION AND MAINTENANCE MANUAL
V. MCCROMETER
products have been carefully designed to be as main-
tenance free as possible. Periodic preventive maintenance, however,
is highly recommended and should be practiced according to schedule
to assure continuous accuracy and trouble free performance of your
transmitter. The maintenance and inspection procedure can also be
used as a guide to locating a problem in the unit that may be the
cause of abnormal operation.
VI. WORKING AREA
chosen for cleaning and inspection of the internal
components should be clean to reduce the chance of dust or dirt
particles being introduced into the transmitter mechanism.
VII. TOTALIZER ASSEMBLY (#4)
service procedure should include
cleaning and inspection of the unit noting any excessive wear on the
change gears (#7 & #8) that may lead to operational problems in the
unit.
1. BONNET MOUNTING SCREWS (#3)
should be removed and
the entire bonnet (#1) lifted off of the meter.
2. TOTALIZER
is contained within the totalizer bonnet (#1) and
held in place by a base cup (#5). It should not be necessary to remove
the totalizer (#4) during inspection; however, removal of the base cup
(#5) is necessary for inspection of the totalizer change gears (#7 &
#8). Removal of the base cup (#5) can be accomplished by inserting
a small screwdriver into the two cutouts and prying upward under the
edge.
3. TOTALIZER CHANGE GEARS (#7 & #8)
should be inspected
for any sign of wear. Both the A-(drive) gear and B-(driven) gear are
attached to the lower portion of the totalizer assembly (#4). Spin the
floating totalizer driven magnet in the center of the totalizer bottom
(#4) to make certain it spins freely without bind or drag. The bottom
of the totalizer has the letter “A” molded next to the A-drive gear
shaft, and the letter “B” next to the B-driven gear shaft.
4. TOTALIZER DRIVE MAGNET ASSEMBLY (#9)
located in the
transmitter base (#10) at the top of the driven clevis shaft (#28)
should be checked and adjusted if necessary to position it 1/16 inch
below the top surface of the transmitter base (#10). Adjustments
can be made by loosening the socket head set screw in the side of
the totalizer drive magnet assembly (#9), and sliding it up or down
the driven clevis shaft (#28) as desired. Always be sure the set screw
is tightened into the flat on the driven clevis shaft (#28).
‡VIII. INDICATOR-TOTALIZER
service procedure should be practiced yearly
and should include removal, cleaning and inspection of the unit not-
ing any excessive wear on the gears and other wear points that may
lead to operational problems in the unit.
‡ For Indicator-Totalizers Only