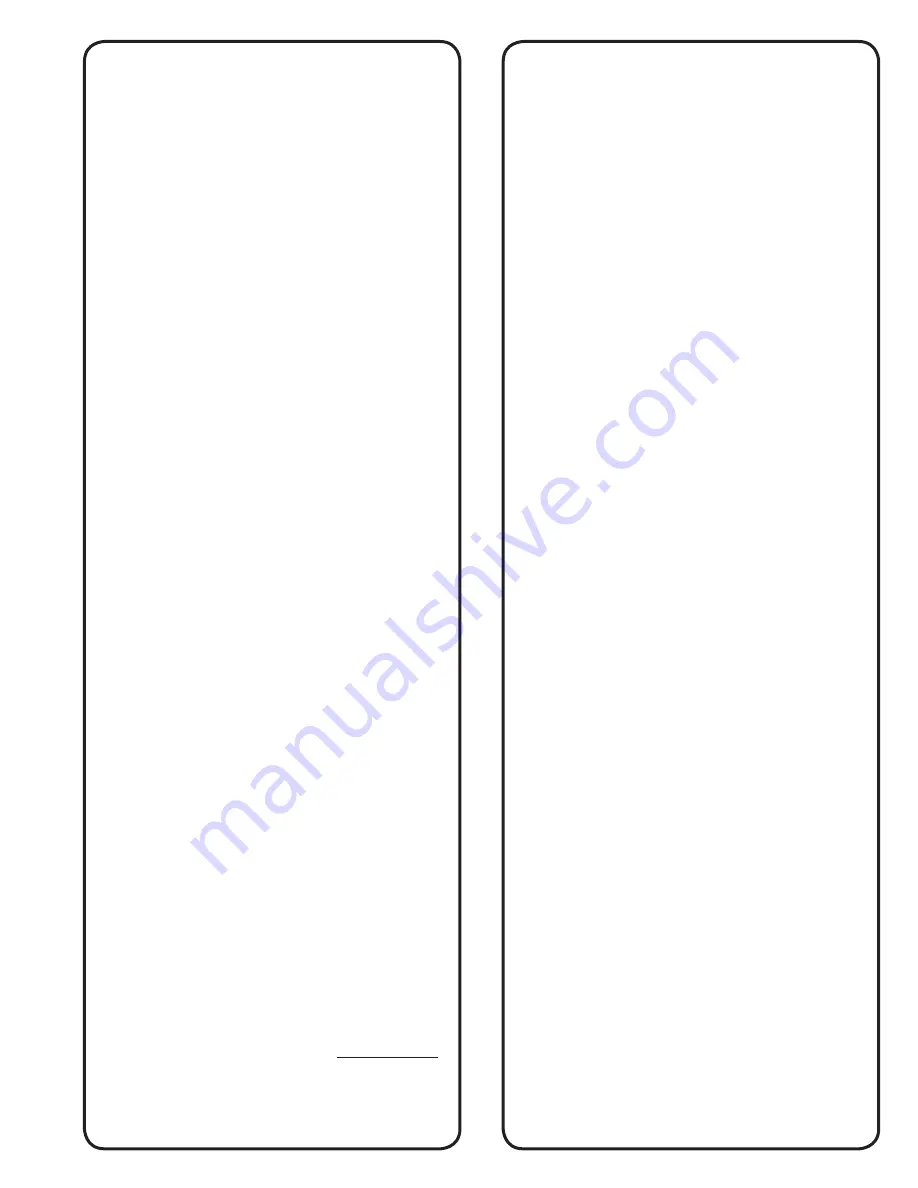
30119-02 Rev. 2.6/07-09
5
IX. MITER GEAR FRAME ASSEMBLY (#21)
can be pulled out of
the back of the gearbox (#17) after removing four screws
(#33). Spin the driven magnet (#24) to make sure the unit
runs freely and inspect the teeth on both the drive (#26)
and the driven (#27) miter gear assemblies for any sign of
excessive wear. If the assembly spins freely and the miter
gears (#26 & #27) are not worn, there should be no further
inspection or disassembly of the unit. Should this service
procedure show that the unit does not spin freely or that
the miter gears (#26 & #27) are worn, the miter gear frame
assembly (#21) should be disassembled as the following
steps indicate and all worn or damaged parts replaced.
1. DRIVEN MITER GEAR ASSEMBLY (#27)
can be removed
by loosening the allen head set screw, located on the side
of the gear hub, and pushing the driven miter gear shaft
(#29) out of the assembly. Note the location of the shim
washer (#28), if any, to be sure it is repositioned properly
when reassembling the miter gear frame assembly (#21).
When reassembling be sure the set screws go into recess in
the miter gear shafts (#24 & #29), or damage could result.
Be sure clevis end of the driven miter gear shaft (#29) is
at the same end as the miter gear is located or the meter
will subtract from the totalizer.
2. DRIVE MITER GEAR ASSEMBLY (#26)
can be removed
by loosening the allen head set screw, located on the side
of the gear hub, and pulling the driven magnet and shaft
assembly (#24) out the front of the miter gear frame (#22).
Note any shim washer (#28) that may be positioned behind
the drive miter gear (#26) when removing the shaft (#24).
3. COMPONENTS
of the miter gear frame (#22) as well as
the gearbox (#17) should be completely inspected at this
point of disassembly. Each part of the miter gear frame
assembly (#21) should be carefully inspected to determine
the origin of any operational problem and those parts that
are damaged or worn should be replaced. Clean the parts of
the unit and reassemble reversing steps (1) and (2) above.
X. PROPELLER ASSEMBLY (#39)
inspection includes cleaning
the ceramic sleeve bearing (#41), separator assembly (#34),
drive magnet (#43), and the propeller assembly (#39).
1.
PROPELLER REMOVAL
can be accomplished by first re-
moving the thrust bearing cartridge assembly (#50). Loosen
the set screw (#49) in the side of the nose of the propel-
ler. Remove the thrust bearing cartridge (#50) by turning
it counterclockwise while holding the propeller in place.
2. REVERSE THRUST BEARING CARTRIDGE (#46)
must
now be removed. Turn the propeller (#40) so that the al-
len wrench clearance hole is lined up with the set screw in
the side of the reverse thrust bearing cartridge (#47). The
location of the set screw is marked by a small hole drilled
in the face of the reverse thrust bearing cartridge. With a
5/64 inch allen wrench, loosen the set screw (#47) in the
reverse thrust bearing cartridge (#46) two to three turns,
which will allow the cartridge to be unscrewed without dam-
aging the spindle thread. NOTE: If the bearing area appears
to be clogged with dirt or sediment, making it difficult to
locate the set screw (#47) or to allow the allen wrench to
fit into the set screw socket, then the bearing area should
be flushed out with water. Insert Tool T-2402X-1 into the
propeller through the threaded nose. The tabs in the tool
should engage in the screwdriver slot in the end of the
reverse thrust bearing cartridge (#46). Remove the propeller
assembly (#39) and reverse thrust bearing cartridge (#46)
by turning Tool T-2402X-1 counterclockwise unscrewing
the reverse thrust bearing cartridge (#46) from the spindle
(#35). The propeller assembly with reverse flow cartridge
will now slide off the spindle.
WARNING:
If the reverse
thrust cartridge does not unscrew easily, it may be because
the set screw was not unscrewed enough. If unscrewing
the reverse flow cartridge is continued with the set screw
binding on spindle thread, damage to thread could occur.
3. WATER LUBRICATION
of the ceramic sleeve bearing
(#36) is achieved by means of two openings in the end of
the thrust bearing cartridge (#50) which allows air to be
purged from the bearing area. These should be cleared of
any foreign material by running a small wire through the
holes on either side of the screwdriver slot.
4. CERAMIC BEARING CARTRIDGE (#41)
and drive mag-
net (#43) should be cleaned of any foreign material and
inspected for damage. Using a bottle brush, thoroughly
clean the ceramic bearing surface (#41) and the magnet
inside diameter (#43). After cleaning the propeller, flush the
inside out with water. The outside surfaces of the propel-
ler should also be cleaned to assure a smooth, unrestricted
flow across the surface of the propeller. Do not use an
oil-based solvent in cleaning, as damage to the assembly
could occur.
5. SPINDLE CERAMIC SLEEVE (#36)
and the O.D. or surface
of the separator (#35) should be cleaned and inspected for
any substantial amount of wear. The thrust bearing (#50)
should be checked for any damage. If it is determined that
the spindle ceramic sleeve (#36) or separator (#35) are worn
sufficiently, the separator/support spindle assembly (#34)
should be replaced.
6. SEPARATOR/SUPPORT SPINDLE ASSEMBLY (#34)
can
be removed for replacement by removing the four mounting
screws (#37) which thread into the drop pipe. Separator
o-ring (#38) should be replaced and the new o-ring (#38)
covered with a thin coat of silicone grease. The separa-
tor/support spindle assembly (#34) can then be replaced in
the front of the drop pipe (#17) with a firm push, gently
rotating the assembly at the same time. Replace and tighten
the four mounting screws (#37).
7.
PROPELLER INSTALLATION
is accomplished by following
these steps:
a)
The reverse thrust cartridge set screw
(#47) should be protruding out of the reverse thrust bear-
ing cartridge so it will not bind up on the spindle thread.
NOTE: Look through the end of the propeller and hole in
the reverse thrust cartridge to be sure the set screw is not
showing.
b)
Slide the propeller assembly onto the support
spindle (#18) until the reverse thrust bearing cartridge (#46)
contacts the threads on the end of the spindle (#35). Using
Tool T-2402X-1, thread the reverse thrust bearing cartridge
onto the spindle. If you feel any resistance when threading